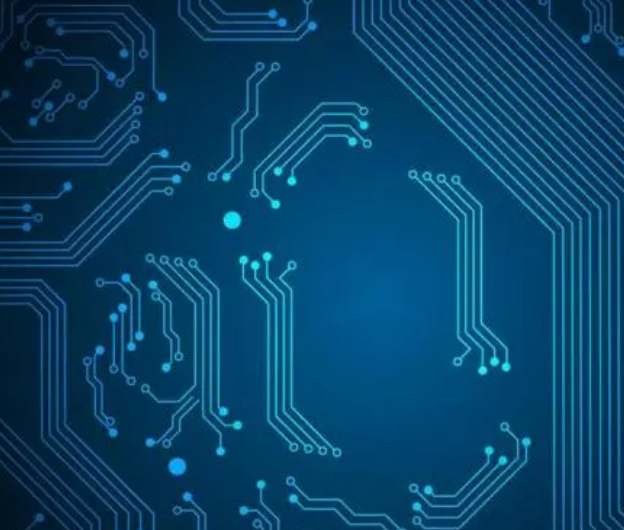
The Laminates specimen is filled with high temperature saturated steam and high pressure can be applied to it to place the laminates sample in it for a period of time to force the water gas into the plate, and then takes out the plate and lays it on the surface of the high temperature solder to measure the "lamination resistance" characteristic. The word "Pressure Cooker" is also commonly used in the industry. In addition, there is a high temperature and high pressure carbon dioxide "cabin pressure method" in the process of laminate compaction, also belonging to the Autoclave Press.
2, Cap Lamination pressure method
The term refers to the traditional laminating method used in the early days of multilayer PCB boards, when the "outer layer" of MLBS was laminated and pressed with thin, single-sided copper substrates. It was not until the end of 1984, when the production of MLBS increased significantly, that the current large or mass laminating method (Mss Lam) was used. This early MLB process, using a thin, single-sided copper substrate, was called Cap Lamination.
3. Crease
In the laminate pressing, often refers to the copper in the treatment of improper wrinkles. Thin copper under 0.5oz is more prone to this defect when pressed in multiple layers.
4, Dent sag
It refers to the gentle and uniform sag on the copper surface, which may be caused by the local punctured protrusion of the steel plate used for compression. If the fault type edge drops neatly, it is called Dish Down. If these shortcomings unfortunately remain on the line after copper erosion, it will cause the impedance of high-speed transmission signal instability, and Noise. Therefore, the copper surface of the substrate should be avoided as far as possible.
5. Caul Plate separator
When the multilayer plate is pressed, in each Opening of the press bed (Opening), often stacked many "volumes" of the loose material (such as 8~10 sets), between each set of "loose material "(Book), must be separated by flat, smooth and hard stainless steel plate. This kind of mirror stainless steel Plate for separation is called Caul Plate or Separate Plate, currently commonly used AISI 430 or AISI 630, etc.
Keyou Circuit specializes in the production of PCB rapid proofing and batch, with high precision single side/double side/multilayer circuit board (1-26 layers), thermoelectric separation copper substrate, multilayer industrial control circuit board, medical circuit board, security PCB board, communication PCB board, automotive circuit board, composite bus copper substrate, foldable metal substrate, etc.
6, Foil Lamination copper foil pressing method
Mass Lam refers to a mass-produced multilaminate, in which the outer layer of copper foil and film is pressed directly into the inner layer of skin, to become mass Lam, which replaces the earlier traditional single-sided thin substrate pressing process.
7. Kraft Paper
When multilayer or substrate board is pressed (laminated), kraft paper is used as heat transfer buffer. It is placed between the hot plate (Platern) and the steel plate of the pressing machine to ease the temperature curve closest to the bulk material. Between sheets of substrate or multilayer plate to be pressed. Try to minimize the temperature differences between the layers, commonly used specifications of 90 lb to 150 lb. Because the fiber in the paper has been broken after high temperature and high pressure, it is no longer toughness and difficult to play the function, so it must try to replace. This kraft paper is the mixture of pine wood and a variety of strong alkali boiled together, until the volatiles escape and remove acid, then wash and precipitate; When it becomes pulp, it can then be pressed into rough, cheap paper.
8, Kiss Pressure
After the plates in each Opening are positioned, the multilayer plate is heated and lifted from the bottom hot plate with a strong hydraulic top column (Ram) to press the loose material in each opening for bonding. At this time, the combined film (Prepreg) began to soften and even flow, so the pressure used for the top extrusion can not be too large, to avoid the slide of the plate or the amount of glue out too much. This initial low pressure (15 to 50 PSI) is called "kiss pressure". However, when the resin in each film loose material is softened and gummed by heat and is about to harden, it needs to be raised to the full pressure (300 ~ 500 PSI), so that the loose material can be closely combined and formed into a solid multilayer board.
9. Lay Up
Before pressing the multilayer circuit board or substrate, it is necessary to align the inner board, film, copper and other loose materials with steel plate, kraft paper cushion, etc., up and down, down, or alignment work, so that it can be carefully sent into the pressing machine for hot pressing. This kind of preparation is called a Lay Up. In order to improve the quality of multilayer panels, not only this "composite" work should be carried out in a clean room controlled by temperature and humidity, but also for the speed and quality of Mass production, Mass Lam construction is generally adopted for those below eight layers, and even an "automatic" composite method should be used to reduce human errors. In order to save plant and shared equipment, the general factory will be "composite" and "folding plate" two combined into a comprehensive processing unit, so its automation engineering is quite complex.
10. Mass Lamination (Lamination)
This is a new construction method in which the multilayer plate compression process gives up the "alignment tip" and adopts multiple rows of plates on the same surface. Since 1986, when the demand for four - and six-layer panels increased, the pressing method of multilayer panels has changed greatly. Earlier, a piece of process plate to be pressed on only one shipment plate, this one-to-one arrangement has been broken through in the new law, according to its size can be changed into a pair of two, or a pair of four, or even more row for pressing. The second new law is to cancel all kinds of loose materials (such as inner sheet, film, outer single-sided sheet, etc.). The outer layer is changed to copper foil, and the "target" is made on the inner layer plate first, and the target is "swept" after pressing, and then the tool hole is drilled from the center, which can be set on the drilling machine for drilling. For six - or eight-layer plates, the inner layers and the film can be riveted first, and then pressed together at high temperature. This simplification allows for rapid and increased area compaction, as well as increased "High" and "Opening" based on the plate approach, reducing labor and doubling production, and even automation. The platen method of this new concept is called "mass platen" or "large platen". In recent years, there have been many professional OEM pressing industry.