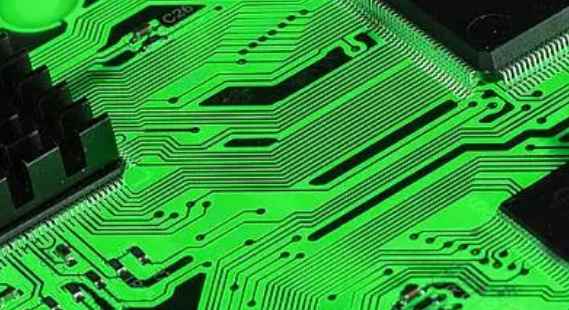
According to the conventional welding resistance engineering design, the size of the single-side welding resistance pad must be 0.05 mm larger than the size of the auxiliary welding pad. Otherwise, the welding aid layer may be covered by flux resistance. As shown in Figure 5, the width of single solder resistance is 0.05mm, which meets the requirements of welding resistance production and processing. However, the edge spacing between the two solder pads is only 0.05mm, which does not meet the requirements of the minimum solder bridge process. In the engineering design, the whole row of pins of the chip is designed as the group welding plate window design. As shown in Figure 6:
Actual welding effect
According to the engineering design requirements after the board, and finish SMT patch. The welding defect rate of the chip is more than 50% through the functional test. Again through the temperature cycle experiment, more than 5% defective rate can be screened. It is preferred to analyze the appearance of the device (20x magnifying glass) and find that there are tin slag and welding residue between adjacent pins of the chip; Secondly, the failure of the product is analyzed, and it is found that the failure chip pin short circuit burned. As shown in Figure 7:
PCB LAYOUT design optimization
Referring to IPC 7351 standard packaging library, the design of the aid pad is 1.2mm * 0.3mm, the design of the stop pad is 1.3 * 0.4mm, and the spacing between the center of the adjacent pad is 0.65mm. Through the above design, the size of 0.05 mm single-side solder resistance meets the PCB processing requirements, and the size of 0.25 mm spacing between adjacent solder resistance edges meets the solder resistance bridge process. Increasing the redundant design of solder resistance bridge can greatly reduce the welding quality risk and improve the reliability of products.
PCB engineering design optimization
According to Figure 8, the width of the welding aid pad was coppered, and the size of the welding block width pad was adjusted. Ensure that the edge between the two assist-welding pads of the device is greater than 0.2 mm, and the edge between the two resist-welding pads is greater than 0.1 mm, and the length of assist-welding and resist-welding pads remains unchanged. Meet the manufacturability requirements of PCB solder resistance single plate window design.
Design verification
In view of the problems mentioned above, the design of pad and solder shield is optimized through the above scheme. The edge spacing of adjacent pad is greater than 0.2mm, and the edge spacing of solder shield pad is greater than 0.1mm. The size can meet the requirements of solder shield bridge process. As shown in Figure 10:
Test yield comparison
After optimizing the solder resistance design from PCB LAYOUT design and PCB engineering design, the same number of PCBS are arranged to be replenished, and the mounting production is completed according to the same process. The parameters of the product are shown in Table 1:
According to the above data, the optimization scheme is validated and meets the manufacturability design of the product.
PCB baking specification for dry goods
First, PCB control specifications
1. PCB unpacking and storage
(1) PCB board can be directly put into use within 2 months of the manufacturing date without unpacking
(2) The manufacturing date of PCB board is within 2 months, and the unpacking date must be marked after unpacking
(3) The manufacturing date of PCB board shall be within 2 months, and the PCB board shall be put into use within 5 days after unpacking
2, PCB baking
(1) If the PCB is sealed and unpacked for more than 5 days within 2 months of the manufacturing date, please bake at 120 ±5℃ for 1 hour
(2) If the PCB is more than 2 months after the manufacturing date, please bake it at 120 ±5℃ for 1 hour before going online
(3) If the PCB is more than 2 to 6 months after the manufacturing date, please bake it at 120 ±5℃ for 2 hours before going online
(4) If the PCB is more than 6 months to 1 year after the manufacturing date, please bake it at 120 ±5℃ for 4 hours before going online
(5) The baked PCB shall be used within 5 days (put into IR REFLOW), and the PCB shall be baked for another 1 hour before it can be used on line.
(6) If the PCB is more than one year after the manufacturing date, please bake it at 120 ±5℃ for 4 hours before going online, and then send it to the PCB factory to spray tin again before going online
3. PCB baking method
(1) Large PCB (16 PORT or above including 16 PORT) shall be placed flat, with a maximum number of 30 pieces in a stack. After baking, open the oven within 10 minutes, take out the PCB and place it flat for natural cooling (pressure proof board bay fixture).
(2) Small and medium-sized PCB (including 8PORT below) is placed flat, a maximum of 40 pieces in a stack, the number of upright is not limited, after baking 10 minutes open the oven to take out the PCB flat natural cooling (pressure anti-board bay governing equipment)
2. Preservation and baking of PCB in different regions
The specific storage time and baking temperature of PCB are not only related to the production capacity and production process of PCB manufacturers, but also have a great relationship with the region.
The shelf life of PCB made by OSP process and pure gold sinking process is generally 6 months after packaging. Baking is not recommended for OSP process.
PCB preservation and baking time has a great relationship with the region, in the south of the general humidity is relatively heavy, especially in Guangdong and Guangxi, in March and April every year there will be a "south day" weather, rainy every day, at this time is very humid. PCB must be used up within 24 hours after exposure to air, otherwise it is easy to oxidize. After normal opening, 8 hours is the best. For some PCBS that need to be baked, the baking time is longer. In the northern region, the weather is generally dry, PCB storage time is longer, baking time can also be shorter. Baking temperature is generally 120 ±5℃ baking, baking time according to the specific situation to decide.