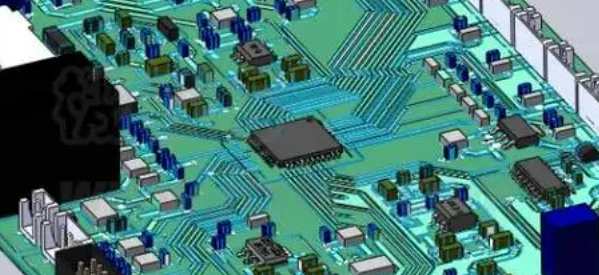
The normal thickness of PCB finished board thickness is between 0.8mm and 1.6mm, and the more common board thickness is designed by default according to the metric unit 1.6mm (the British unit is about 63mil). Many connectors are also adapted to the standard of 1.6mm. How does the thickness standard come about?
According to the chapter "History of PCB Development" in the column of PCB Design Board Success, PCB industry was still in its infancy in the era of electronic tube. Due to the high heat content and bulky volume of electronic tube components, it was not convenient to install them on printed circuit boards (requiring certain mechanical strength). At that time, the production and manufacturing of electronic products were basically manual scaffolding installation. Of course, this is also related to the development of PCB substrate materials, as PCB substrate epoxy resin (see the column of PCB substrate resin chapter), PCB substrate reinforcement materials, copper foil and other manufacturing technologies have not realized commercial production.
In the 1920s, circuit developers used bakelite (phenolic), drywall, cardboard, and even thin wood chips to build circuit boards (similar in form to hole-boards or breadboards, as opposed to printed circuit boards). They drilled holes into the material, then riveted or bolted flat copper wires to circuit boards to form interconnecting circuits.
TRF radios made by Signal in the 1920s were built on wooden breadboards
Bakelite, also known as phenolic resin, was first synthesized in 1872 by the German chemist Adolf von Baier (1835-1917). In 1907, the Belgian-born American chemist Leo Hendrik Baekeland (1863-1944) improved the production technique of phenolic resin and made it practical and industrial. In 1910, he founded General Bakelite and gave the phenolic resin brand name "Bakelite" after his name.
In the early 20th century, relying on Baekeland's patent for phenolic resin manufacturing, the industrial production of phenolic resin was realized successively in Germany, Britain, France and Japan. Phenolic resins also began to be widely used in radio knobs, turntables, circuit boards for mounting components (non-printed circuit boards), and even radio product casings.
By 1921, laminates made by Formica had been incorporated into the manufacture of domestic and Marine radios. In 1927, Formica discovered that by adding decorative paper through the lithographic process, their laminates could be made into patterns that mimicked wood grain and marble. The market for laminates expanded rapidly as they became more colorful and decorative, and many countertops used phenolic laminates as decorative panels for countertops.
Phenolic laminate is a kind of strong and well insulated polymer material, with heat resistance, water resistance, chemical resistance and withstand high current characteristics, although it is not specially developed as a circuit board, more widely used in decorative panel use, but phenolic laminate drilling performance or as a support for the installation of vacuum tube, its strength relative to gypsum board, cardboard, Or wood chips are much better, and phenolic laminates are a natural replacement for cardboard or wood boards.
But punching holes in the phenolic laminate and wiring the wires to hold all the electronics together is still a laborious task, more laborious than playing with the cave-board, which is pre-punched, after all. It wasn't long before someone figured out a way to glue a sheet of copper foil onto a phenolic laminate and etch the interconnections between the components into the copper foil (in 1913, Berry in England invented the technique of coating the foil with an resist and etching the uncoated part to form a conductive pattern), thus creating a single-sided printed circuit board. Soon, the development of interconnecting systems between multiple boards created a related need for board-to-board connectors.
1/16 inch or 63mil was the manufacturing thickness of phenolic laminates, and the planet-to-plate connectors were designed to be 1/16 inch (63mil or 1.6mm) thick, forming the industry chain, and 1/16 inch (63mil or 1.6mm) thickness became the default industry standard.
Today, the development of substrate materials has been very diverse, but 1.6mm(or 63mil in imperial units) is still the default finished board thickness of PCB board manufacturers, but the standard board thickness range has been extended to 0.8mm~1.6mm. (The specific process of the plate factory shall prevail, and some plate factories are 0.6mm~2.5mm)
Of course, if you want to produce thinner or thicker (such as 20-layer board) PCB, it is also OK, such as 0.4mm or 3.0mm, but you need to pay extra board cost, so PCB design needs to be considered.