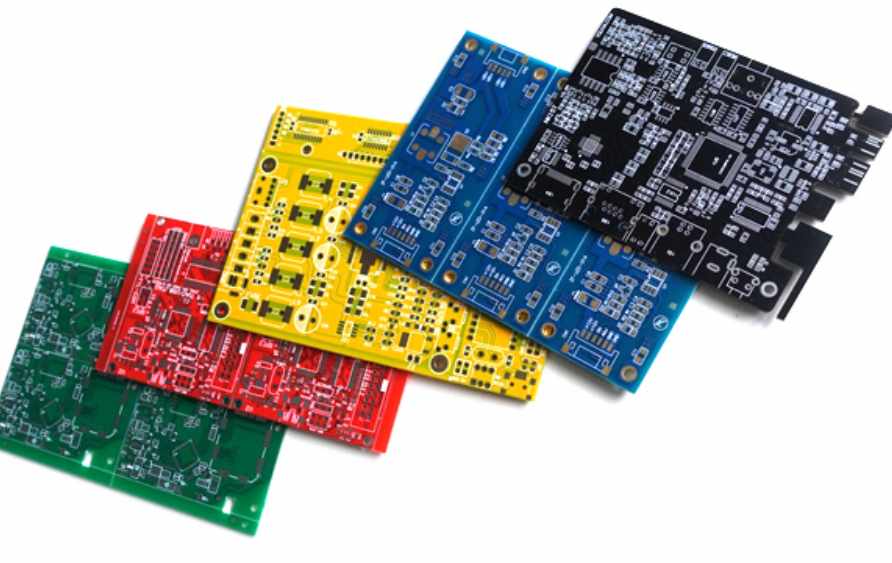
The color of PCB board (printed circuit board) is mainly the color of solder resistance coating. To prevent the oxidation of the copper layer in the PCB board, to separate the welded and non-welded parts and to protect the PCB surface, the design engineers will apply a special coating on the PCB board surface. The coating is named solder resistance layer. The material used is solder resistance paint, and the color of the PCB board depends on the color of the solder resistance paint.
When you get a PCB board, the most intuitive color to see the oil on the board is the color of PCB board we generally refer to. Common colors include green, blue, red, black and so on.
1 green ink is by far the most widely used, the longest history, and in the current market is also the cheapest, so green is used by a large number of manufacturers as the main color of their products.
2. Usually, the whole PCB board product has to go through the process of board making and SMT. In the process of board making, these several processes must go through the yellow light room, because the effect of green in the yellow light room is better than that of other colors, but this is not the main reason.
When SMT is welding components, PCB should go through the process of solder paste, patch and final AOI verification. These processes need optical positioning and calibration. Green background color is better for instrument identification.
3. Common PCB colors are red, yellow, green, blue and black. But at present, due to the production process and other problems, many lines of quality inspection process must rely on workers to see and identify with the naked eye (of course, most of the current use of flying needle testing technology). In the case of bright light eyes keep staring at the board, this is a very tiring work process ah, relatively speaking, green least hurt the eyes, so most manufacturers on the market are using green PCB.
4. The principle of blue and black is that they are respectively mixed with cobalt and carbon and other elements, with certain conductive properties, in the case of power is likely to short-circuit problems, and green PCB is relatively environmentally friendly, used in high temperature environment, generally will not release toxic gases.
Some people think that black PCB board represents high-end, but actually this perception is not correct. The reason why "color represents high or low", that is because manufacturers like to use black PCB to make high-end products, with red, blue, green, yellow and other low-end products resulted.
In addition, black PCB, because its surface line is almost completely covered, causing great difficulties for copying board and later maintenance, so it is not very convenient to manufacture and use a color, and black PCB is the most difficult to hole, so the quality rate is relatively lower than other color PCB board, so the price of black will be a little more expensive.
5. Since about the middle and late period of the last century, the industry has begun to pay attention to the color of PCB board, mainly because many high-end board types of first-line manufacturers have adopted green PCB board color design, so people gradually believe that the PCB color is green must be high-end.
In fact, for various reasons, it is generally better to use green PCB.
So, how to judge the PCB circuit board surface process by color?
1. Gold
Gold is the most expensive. It's real gold. It's only a thin layer, but it still accounts for nearly 10% of the cost of the board. Gold is used for two purposes, one is to facilitate welding, and the other is to prevent corrosion. Gold coating is widely used in the parts of the circuit board welding pad, gold finger, connector shrapnel and other positions. In consumer electronics, mobile phone motherboard is mostly gold plate, computer motherboard, audio and small digital circuit board is generally not gold plate.
2. Silver
The silver is not silver, but tin. The silver circuit board is called a tin-spray board. Spraying tin over copper wiring can help with welding, but does not provide the same long-term contact reliability as gold. The tin spray plate has no effect on the welded components, but for the welding pad exposed to air for a long time, the reliability is not enough, long-term use is easy to oxidation rust, resulting in poor contact. Small digital products of the circuit board, without exception is spray tin plate.
3. Light red
OSP, an organic soldering film, is cheaper than the tin-spraying process because it is organic, not metal. The only function of this organic film is to ensure that the inner copper foil does not oxidize before welding. The film evaporates when you heat it up during welding. Solder can be used to weld copper wire and components together. But corrosion resistance, an OSP circuit board, exposed to air for more than ten days, can not be welded components. Many computer motherboards use the OSP process.