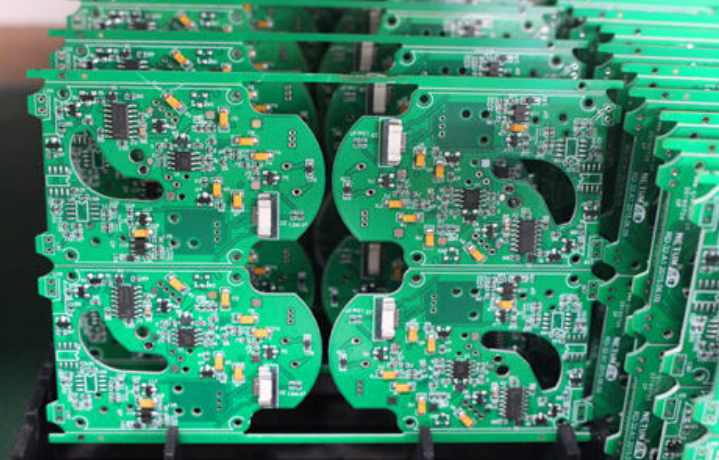
Today, the society is changing with each passing day, product upgrading is very fast, such as the development of the mobile phone field is proof, in this rapid development today, we have missed in all the technological progress -- a good PCB automatic wiring device.
One, the real problem faced by automatic wiring device
Although PCB automators have been around as long as engineers have known about CAD, engineers involved in designing dense boards have almost completely ignored the implementation of automated technology. No wonder. Automatic routing algorithms have changed little since they were first introduced.
Combine stagnant technology with EDA vendors that offer varying degrees of performance and configuration with auto-wiring technology, and it's no wonder that auto-wiring can't keep up. Technologies that would have saved design time and enhanced workflow have not progressed substantially enough to match the expertise and efficiency of experienced PCB engineers. Is that really all the auto-wiring has to offer?
Two, early automatic wiring technology
The results and performance of the first batch of automatic wiring devices produced by EDA manufacturers were poor. Most of these wiring devices do not provide guidance or configuration for signal integrity and often add too many holes to the process. Early technical problems also included automatic wiring limited to strict X/Y grid requirements, but with deviations between layers.
Because of these limitations, board space is often wasted, and engineers have to clean up the mess of uneven board layouts. In order to fix poor layout caused by automatic wiring, engineers often need to invest longer time than manual wiring. From the beginning, automatic wiring lacked a good start.
Three, the 80's progress of automatic wiring
With the passage of time, automatic wiring technology has been only minimally improved, and the quality is far from what PCB engineers expected. The problems continue to be improper layout of circuit boards, misaligned layers, and too many holes. To move this problematic technology forward, EDA vendors are adopting new components and circuit board technologies to easily meet signal integrity requirements.
If there is one way to describe the development of automatic wiring technology in the current era, hardware limitations are also an obstacle. Without a dedicated CPU and additional memory to support the required data, the auto-routing algorithm cannot reduce the grid size to provide better wiring quality. Without a hardware-based solution, EDA vendors began exploring other approaches, including shape-based automated wiring.
These new shape-based automatic wiring devices do meet board fabrication and signal integrity requirements in the following ways:
1. Establish effective interconnection between components
2, in the process of automatic wiring using fewer holes, thus reducing the cost of PCB
3. Use fewer layers on the PCB board and increase the spacing
Despite these advances, automatic wiring technology is still objectively mediocre. Although EDA vendors have overcome hardware limitations, PCB engineers remain skeptical about the adoption of automatic routing technology.
The lackluster progress of the 1990s
Near the turn of the millennium, automatic cablers continued to improve with new features, including optimizing angles, pushing wiring patterns, using fewer holes, and even trimming techniques that removed extra line segments. In addition, there are some automatic wiring techniques to eliminate any layer deviation.
While all these new advances sound promising, have they had the necessary impact on the PCB design community? Unfortunately, no. The more EDA vendors impose automatic routing technology on reluctant PCB designers, the more side effects occur, including:
1, the output of circuit boards increased, but the wiring is incomplete and poor.
2. It increases the complexity of automatic wiring configuration and requires expert configuration.
3. PCB designers need to spend more time fixing bad automatic wiring paths.
4. The 1990s saw a continuing trend of manual wiring being king as the design nears completion.
Will the 2000s bring new hope?
The millennium arrived, bringing with it new components and board technologies that changed the way PCBS were manually routed. Now in most designs, the number of holes must be reduced to maintain signal integrity. Signals began to require delay/time management, differential pairs began to become the standard for high-speed applications, and BGA became the preferred option for many larger pin number packages. These changes in design consciousness led to the era of River-Routing.
The river wiring method is surprisingly efficient and greatly reduces the number of holes on the board, evenly uses each board layer, and has no wiring board layer deviation. Despite these advances, they have been rarely adopted. Why? This time it's not because of technology, but because of the habits of PCB designers. Because PCB designers in the process of placing components, constantly in their mind to the circuit board wiring simulation, which directly affects how/where the components are placed, thus affecting the wiring implementation. For many engineers, trying to interrupt the middle of this workflow with river wiring is not feasible.
As an alternative method of river network routing, there is a new trend of route planning. This approach provides a complete set of tools for designers to configure automatic wiring Settings, including layer stack definitions, design rule constraints, signal masking, and more. All of this is set up to ensure automatic wiring, but configuring properties still takes more time than the manual wiring process.
Six, the goal is the same, but the method is different
Despite all the advances in automatic wiring over the past three decades, it is still rarely adopted by most engineers. Is there a problem with the technologies themselves, or is there a conflict between the PCB designer's expectations and the automatic routing machine?
In particular, PCB engineers collaborate on component layout and wiring, often identifying logical component placement and interconnect points in a 10,000 ft circuit board layout view. An automatic cabler, on the other hand, deals with the same wiring problem from the bottom up, interconnecting one place at a time.
For more dense board layouts, engineers typically sketch the bus system and subsystems on paper, which they then use as a guide to the manual wiring process. Engineers often consider several other variables as they place components, including delivery date, design complexity, and product cost.
And, of course, there is the dreaded Engineering Change Order (ECO). ECO can trigger nightmarish chain reactions, especially when it affects complex design components such as BGA. For these types of tasks, an automatic routing device is an efficient tool only if it can optimize line escape or fan out without adding additional holes. Although good designers can reduce the problem with this process by optimizing pin allocation, the problem still exists, with or without an automatic routing device.
Seven. What does the EDA industry really need
Thirty years later, we're still waiting for an interactive cabler that instantly translates desired cabling topologies into reality with a single click. What does the future of automated wiring need to involve in order to be taken seriously?
1. Agility. The technology needs to be flexible enough to give PCB designers complete control over wiring direction, location, and choice, regardless of design complexity.
2. Efficiency. The technology takes less time to wire and is more efficient than manual wiring.
3. Simplicity. The technology needs to be easy to configure, allowing PCB designers to edit paths as needed.
4. Quality. This technique is required to ensure the quality of signal integrity and no board deviation when routing and distributing paths with multiple boards.
5. Reliability. This technology needs to consistently produce reliable results and be successful on the first release.
6. Integration. This technology needs to be integrated with our existing design solutions and associated with our design constraints.
7. The price is reasonable. For widespread use, make sure all PCB designers can afford it.
It is believed that with the continuous development of PCB automatic wiring technology, it will be more humanized and gradually accepted by engineers. In the future, the wide application of PCB automatic wiring will benefit PCB manufacturers as well as PCB processing plants.