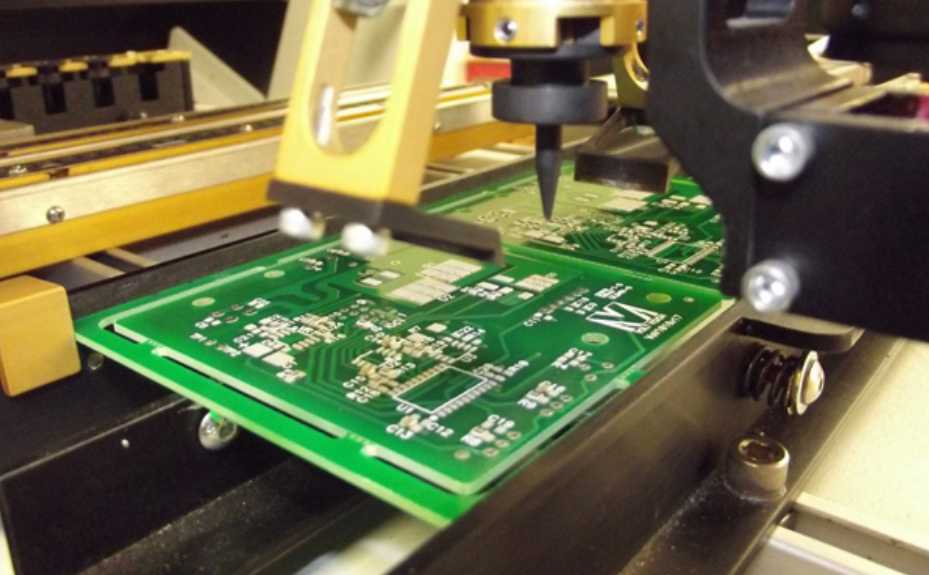
Reflow welding is a very important and complicated process in SMT process. Due to improper operation in printing process and mounting process, as well as unreasonable parameter setting of reflow welding, many common welding defects will appear, leading to high defect rate of products and increasing maintenance cost.
Common welding defects and prevention in reflow welding
1. Bridge connection: Welding heating process will also produce solder collapse, this situation appears in preheating and main heating two occasions, when the preheating temperature in the range of dozens to one hundred, as one of the components of the solder solvent will reduce viscosity and outflow, if the outflow trend is very strong, will at the same time the solder particles extrusion outside the welding zone to form gold particles, in the melting if can not return to the welding zone, Trapped solder balls will also form.
Prevention: The main cause of bridging is excessive welding paste or welding paste after printing dislocation, edge collapse.
(1) A 0.15mm thickness template can be selected for printing, and the hole size is determined by the minimum pin or chip element spacing.
(2) When printing the printed board with the spacing between pins or chip elements less than 0.65mm, optical positioning should be adopted, and the reference point should be set at the diagonal of the printed board. If optical positioning is not used, printing dislocation will occur due to positioning errors, resulting in bridging.
(3) In order to prevent edge collapse, to choose higher viscosity solder paste; Using laser cutting template; Reduce scraper pressure. Adjust the mounting pressure and set the descending position of the mounting nozzle including the thickness of the element itself. Set the appropriate welding temperature curve (temperature, time) and prevent mechanical vibration of the conveyor belt.
2. Tin ball: Tin ball is mainly caused by the flying of solder caused by the rapid heating in the welding process. It is related to solder paste viscosity, solder paste oxidation degree, solder particle thickness (particle size), flux activity, etc.
Prevention: To increase the viscosity of solder paste, the oxide of solder paste should be controlled at about 0.03%, and the maximum value should not exceed 0.15%. The thickness of solder particles generally requires that the number of particles below 25um shall not exceed 5% of the total number of solder particles. Adjust the temperature curve of reflow welding so that the welding paste can be fully preheated before welding. Proper form hole shape and size will also reduce the production of solder balls. In general, the size of the template holes should be 10% smaller than the corresponding pad.
3. Erect tablet: The warping of tablet elements under the condition of rapid heating.
Prevention: (1) Choose solder with strong adhesion, and the printing accuracy of solder and the mounting accuracy of components should also be improved.
(2) The external electrode of the component needs to have good wetting stability. Recommended: Temperature below 400C, humidity below 70%RH, the service life of components into the factory should not exceed 6 months.
(3) Adopt a small width of the welding zone to reduce the surface tension on the end of the component when the solder melts. In addition, the printing thickness of solder can be appropriately reduced, such as 100um.
(4) Setting of welding temperature management conditions is also a factor for component warping. The general objective is to heat evenly, especially before the formation of welded fillets at the two connecting ends of the element, so that the equilibrium heating does not fluctuate.
4, cold welding: incomplete reflux will form solder joints.
Prevention: Adjust the reflow welding temperature curve to increase the preheating time of the heating zone.
5. Virtual welding: refers to the unstable state caused by improper production technology in the production process. The other is that after long-term use of electrical appliances, some of the more serious heating parts, the welding spot at the welding foot is very easy to appear aging stripping phenomenon caused by.
Prevention: Take good care of QFP chip to prevent deformation and oxidation of pin, preheating temperature should not be too high during welding, and heating speed should be appropriate and uniform.
6, popcorn phenomenon: some plastic sealing components due to moisture absorption and welding temperature, heat expansion, the formation of popcorn phenomenon.
Prevention: pay attention to storage, prevent moisture, and dry components with water vapor before use.
7, components offset: after reflow welding will find some components offset phenomenon.
Prevention: For the parts pasted by the mounter, the mounting accuracy and placement position of the mounter can be adjusted, and the new welding paste with strong adhesion can be replaced. If it is due to reflow welding, it is necessary to consider whether there is vibration on the conveyor belt in the reflow furnace and check the reflow furnace. Adjust the heating curve and preheating time; Eliminate the vibration of the conveyor belt; Change the active agent; Adjust the solder paste supply.
8. PCB distortion: PCB distortion is a common problem in SMT mass production.
Prevention: (1) If the price and space allow, choose better quality PCB or increase PCB thickness to achieve the best aspect ratio.
(2) Design the PCB circuit board reasonably, the area of double-sided copper foil is balanced, and preheat the PCB before the patch; Adjust the fixture or clamping distance to ensure the PCB expansion space under heat.
(3) welding process temperature as low as possible.
(4) When mild distortion has occurred, it can be placed in the positioning fixture and reset by heating to release the stress.
The defects of reflow welding are caused by many reasons. In order to reduce the defects of reflow welding and improve the yield of products, it is necessary to deeply study all aspects of welding process.