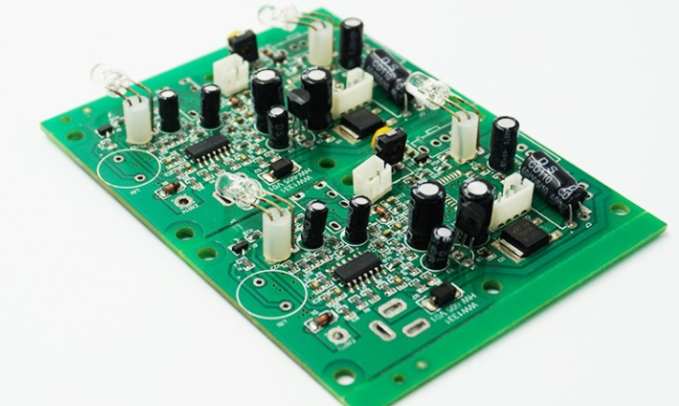
What are the reasons for PCB copper-clad laminates?
Signs: poor print adhesion, poor coating adhesion, some parts can not be etched off, and some parts can not solder.
Possible inspection methods
It is usually used for visual inspection by forming visible streaks of water on the surface of the plate.
Probable cause
Due to the very dense and smooth surface caused by the release film, the surface of the uncovered copper is too bright. Usually on the uncopper-covered side of the laminate, the laminate manufacturer does not remove the release agent. Pinholes in the copper foil cause the resin to flow out and accumulate on the surface of the copper foil, which is usually found on thinner copper foil than the 3/4 oz weight specification. Copper foil makers apply excessive amounts of antioxidants to the surface of copper foil. The laminate maker changed the resin system, the stripper, or the scrub method.
There are many fingerprints or grease stains due to improper operation. Wet with oil during punching, blanking or drilling operations.
Possible solutions:
Laminate makers are advised to use fabric - like films or other release materials. Contact the laminate manufacturer for mechanical or chemical removal. Liaise with laminate manufacturer to inspect each batch of copper foil for non-conformity; Ask for a solution to remove the resin. Ask the laminate maker for removal methods. General recommended the use of hydrochloric acid, followed by mechanical brush removal. Cooperate with laminate manufacturer and specify user test items before any changes are made to laminate manufacture. Teach all process personnel to wear gloves to handle copper-clad plates.
Make sure that the laminates are shipped with appropriate padding paper or bagged, that the padding paper is low in sulfur, that the packaging is free of dirt, that no one touches the copper foil while using detergent containing silicone, and that all laminates are degreased prior to plating or graphic transfer processes.
2. Classification and identification of solder paste for SMT plant
. The melting temperature of tin and lead welding paste is 178 ~ 183℃. With the different types and compositions of metals used, the melting temperature of solder paste can be increased to more than 250℃, or reduced to less than 150℃. According to the required welding temperature, the welding paste is called medium temperature, and those lower than their melting temperature are called low temperature welding paste, such as bismuth and indium base welding paste. Those above their melting temperature are called high temperature solder paste, such as Sn96 solder paste. Their alloy composition, melting temperature and use comparison.
Classified by flux activity
The flux usually contains halogen or organic acid components, which can quickly eliminate the oxide film on the surface of the metal to be welded, reduce the surface tension of the solder, so that the solder quickly spread on the surface of the metal to be welded. But too high activity of flux can also cause corrosion and other problems, which should be selected according to the requirements of the product.
According to the activity of flux can be divided into active (RA), medium activity (RMA), inactive (R), water washing (OA), no cleaning (NC) several categories.
Type R: Flux is the least active. It contains only rosin and no active agent.
RMA type: contains both rosin and active agent.
RA type: A fully activated rosin or resin system with higher activity than RMA type.
OA type: refers to organic acid flux, with high flux activity. OA flux is generally considered corrosive.
RMA and R flux do not necessarily need to be cleaned. The halogen content in RMA solder paste is usually lower than 0.05%, so the corrosion is very small. For civilian SMT products, it can not be cleaned, while the halogen content in RA solder paste is usually higher than 0.2%, so the welding performance of the solder paste is very good. RA/OA must be cleaned because the acid will eat away the solder joints; Free cleaning is introduced in recent years, the activator uses organic acids, so the corrosion is weak, the general product can not be cleaned. At present, in the production of electronic products, strong active solder paste is basically not used.
The range of viscosity
It is usually 100 ~ 600Pa•S, and the highest can be more than 1000 Pa•S. Use according to the different paste technology means to choose.
According to the viscosity of solder paste classification, in order to adapt to different technological methods to distribute solder paste needs.
The above several kinds of solder paste can be crossed to form different needs of solder paste.
For example, according to whether the use of rosin resin, welding paste can also be divided into fragrance and water soluble solder paste.