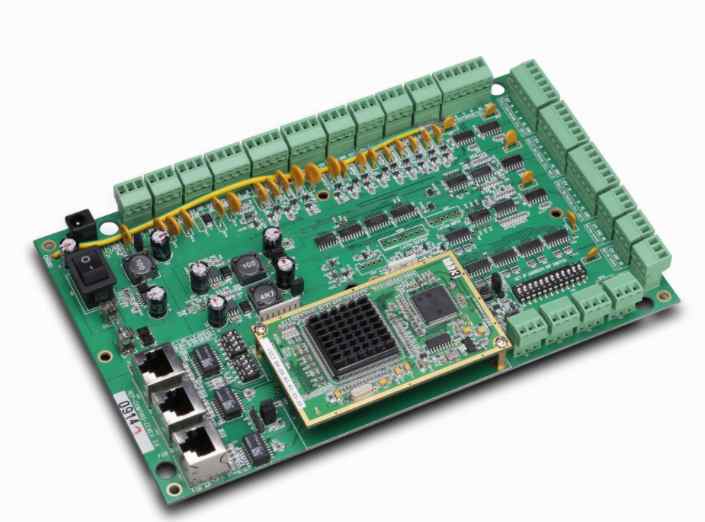
1. In the welding process of smt patch processing, substances that can purify welding metal and welding surface and help welding are called flux, or flux for short. Flux is an indispensable process material in the process of soft brazing. Liquid flux is used in wave soldering and manual welding process. Flux and solder are used separately. In reflow soldering process, flux is an important part of solder paste. The welding quality is fast. In addition to the quality of solder alloy, components, PCB and welding process, it also has a very important relationship with the performance of flux and the selection of flux. What are the requirements for the chemical properties of the flux?
The physical characteristics of flux mainly refer to melting point, surface tension, viscosity, mixing and so on, which are related to welding performance.
To help the flux has a certain chemical activity, good thermal stability, good wettability, the expansion of the solder has a promoting effect, retained in the substrate of the flux residue on the substrate is non-corrosive, with good cleaning, the amount of chlorine contained in the prescribed range.
The general requirements are as follows:
First, the appearance of the flux should be uniform, transparent, no precipitation or stratification, no foreign matter. Flux should not emit toxic, harmful or strong pungent odor gases and dense smoke, in order to help protect the environment. Its color should not change during the effective storage period.
Two, viscosity and density than molten solder is small, easy to be replaced. The flux density can be diluted with a solvent, 0.80-0.95g/cm3 at 2 or 3 degrees. Clean free flux should be within the range of (100±1.5) % of its nominal density.
Three, the surface tension is smaller than the solder, the wetting expansion speed is faster than the molten solder, the expansion rate is > 85%
Four, the melting point is lower than the solder, before the solder melts, the flux can give full play to the role of welding aid.
Five, the content of non-volatile matter should not be more than 15%, welding does not produce welding bead splash, do not produce gas and strong irritating odor.
Six, after welding residue surface should be non-viscous, not touch, the surface of the chalk powder should be easy to be removed.
Seven, no cleaning type flux requires solid content <2.0%, no halide, less residue after welding, no moisture absorption, no corrosion, good insulation performance, insulation resistance > 1*10 square ohm.
Eight, water cleaning, semi-water cleaning and solvent cleaning type flux requirements easy cleaning after welding.
Nine, stable storage at room temperature.
2. Identification of resistance and capacitance in smt patch processing
Since 2014, there has been more and more demand for large patch resistors from consumer electronics, small device products and vehicle electronic products. Especially for the electronic demand of the automobile industry, the products processed by SMT have increased significantly. However, the trend of automobile data towards new energy electric vehicles has intensified, resulting in the resistance need for patch processing.
In addition to the application of consumer electronics in various small fields, in addition to the high efficacy of patch resistance, high demand, thin, miniaturization is an important highlight. In 2018, the minimum patch resistance size is 01005. The commonly used patch resistance, patch inductance and patch capacitance are difficult to distinguish in appearance. So how to quickly identify common SMT patch components in our daily life? This is a difficult problem that many new people face when they enter the industry.
I. Identification of patch resistance and patch capacitance:
Look at the color - all the patch capacitors are not silk-printed, since the production process is sintering at low temperature, but printed on the outside. Its color is mostly cyan gray.
Look at the mark - the patch capacitor is marked "C" in the circuit and the patch resistance is marked "R".
Look at the silk screen - there is a silk screen is usually resistance.
Second, the discrimination between the chip capacitance and the chip inductance: look at the color - different usually as long as the detailed tantalum chip capacitor is black, other is not black at all. And the patch inductors are all black.
Look at the model code -- the chip inductance starts with L, and the chip capacitance starts with C. From the shape is round beginning to conclude that should be inductance.
Look at the external layout - find the same components can or split components to look at the external layout, with coil layout for the chip inductor.
Three, the discrimination of patch resistance and patch inductance: according to the shape -- the shape of the inductance has a multilateral shape, and the resistance is mainly rectangular. Especially when it is round, the anomaly is usually identified as inductance.
The resistance value of the measurement -- the resistance value of the inductor is relatively small, and the resistance value of the resistance is relatively large.
2. How to control the feeding error of SMT patch processing?
How to control smt patch processing feeding error? Continuous innovation in the electronics industry challenges suppliers at all levels of the industry to make devices that are increasingly powerful in terms of size and performance. In such cases, the gap between board design development and actual production tends to increase, especially because designers often have no first-hand experience with production. For this reason, it is critical to identify potential errors as soon as possible during the pcba proofing phase, especially during smt placement.
When we faced the challenges of new technology, the front and back end teams of Jingbang did not do what they should have done. We took the initiative to look for an attack point. Upgrade equipment, introduce training, from equipment and technology two aspects to improve the comprehensive strength. We have worked with Smart Manufacturing to introduce Industry 4.0 management systems and tools into the production line and implement intelligent manufacturing
Now, besides the traditional AOI and SPI equipment, we have completely upgraded 3Dspi, 3DAoi, X-ray, selective wave soldering, etc., and add smt loading and anti-error equipment. In particular, this anti-error system will be used to reduce quality problems associated with human error.
smt patch processing anti-mismaterial system operation key steps:
This system can replace most manual SMT feeding inspection operations to prevent manual errors, such as:
1. The system imports the working position table of the SMT machine with one key, automatically compares the BOM of the system, identifies the material list is wrong, the actual quantity is insufficient, and the material tray is wrong;
2. The position of the material plate is wrong, the order of the material plate is wrong, etc.
3. When loading and unloading, the production line personnel scan the station number on the machine with a scanning gun, and then scan the bar code label on the material. The system will automatically check whether the feed is correct. Staff private alarm stop line, instead of manual inspection;
4. The scanned and confirmed stations of the production line will prompt the measured values on the IPQC computer, and the measured data of IPQC will be transmitted to the system through the bridge instrument, and the system will automatically judge the measured results. The system automatically records feeding process information, check process action, spot check process, refueling process and other information;
5, the system to check the error of instant alarm, prompt the implementation of corrective measures;
6. Information sharing of machine feeding Settings, and can be printed at any time for material preparation, feeding, personnel refer to the implementation of the material, the standard is consistent;
7. Prevent engineering change data from not being timely notified to all relevant personnel;
8. Traceability of feeding process, convenient for material tracking, personnel tracking, machine running status tracking, etc.
Such equipment can not only identify problems in advance during the sampling phase, but also prevent the transition to mass production. Even before smt starts, quality anomalies due to improper use of components are eliminated. In this way, we can improve our direct rate and enable customers' products to enter the market as early as possible.