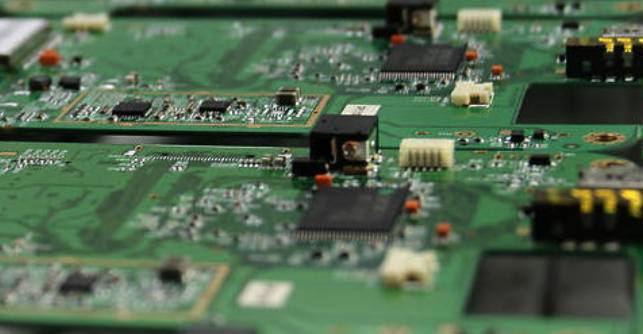
At present, the industry of hot air reflow welding technology generally relies on two technologies: furnace temperature tester and real-time monitoring system.
artificial temperature test
That is, the traditional furnace temperature test method, that is, the production shutdown line manual test furnace temperature, including human, thermometer, temperature plate (consumables), temperature line (consumables), normal 12 hours test once, once 20 minutes (excluding abnormal conditions).
At present, the use of furnace temperature tester is commonly used in the industry. The longer the time from the last test, the more likely the curve is to exceed the process rules. More and more users are aware of the limitations of the current periodic curve test. Any product produced before the next test is likely to be defective.
intelligent temperature testing system
At present, most of the production data of SMT workshop has been connected to MES system, and the data receipt of reflux furnace cannot be completely associated with the data of each PCB board. For the future industry 4.0, the open integrity of data is a necessary link, and the monitoring of furnace temperature data of each PCB board should be strengthened in this part of the reflux furnace. And in the furnace temperature abnormal when the need for timely feedback alarm data, automatic response to stop the corresponding plate operation, prevent the production of large quantities of defective products, for the occurrence of mass production problems play an early warning role.
The intelligent furnace temperature test system is exempt from the regular artificial temperature curve test. Every time the product is replaced, you only need to call out the program and click the run will automatically test the furnace temperature curve to reduce the downtime. Each machine type only needs to measure the reference curve once, and the subsequent system will automatically measure the temperature curve of each product, saving the temperature measuring plate, temperature measuring line and labor, and reducing the production cost. When the production starts, the system will continuously record the temperature curve of each product in real time, so that the data that may lead to excessive can be captured in advance during the production process, so as to avoid the production of defective products.
Function features of intelligent furnace temperature test system
1. Simplify furnace temperature test personnel.
2. Reduce the scrap of temperature measuring plate and temperature measuring line.
3. Reduce SMT shutdown time during furnace temperature test.
4. With industry 4.0, real-time Profile recording of each board can be realized.
Intelligent furnace temperature test system contains built-in high-precision thermocouple probe tube, divided into two groups of probe tube, a total of 30 temperature measuring points, namely 30 thermocouples. The probe pipe is installed on the track, and then connected to the data processing module of the self-used furnace temperature test system. The entryway sensor detects that the product has entered the furnace and starts recording data, which is then transmitted to a computer.
The data of 30 temperature measuring points can be viewed in real time, the real-time monitoring of chain speed, and the temperature of the air point inside the reflux furnace in question can be directly queried during production.
100% continuous real-time monitoring and recording of the furnace temperature curve of each PCB board product passing through the reflux furnace, and automatically judge whether the PCB board meets the process requirements.
With only one busbar Profile, regular verification curve testing can be eliminated, reducing labor requirements, saving verification time, and improving production efficiency.
Record each piece of PCB furnace temperature curve through the reflux furnace, warning file classification statistics, History historical data management: according to the product process defect classification to query the corresponding information, and can generate automatic report export.
Automatic alarm during production ------ including furnace temperature alarm, chain speed alarm, process alarm, bar code loss alarm, CPK alarm. (Automatic analysis of alarm time, event type, event location).
furnace after AOI: AOI automatic optical inspection: will be programmed to make good inspection parameters and inspection in advance components images taken by the camera according to check the logic for processing. If the inspection result is within the standard range specified in the inspection parameters, it is judged to be qualified; if it is outside the standard range, it is judged to be unqualified. Procedure source Bom and patch coordinates, all objects outside the patch coordinates are not within the detection range.
AOI test process
When the light is irradiated from the top to the normal welding spot, the reflection light of the reverse mirror cannot enter the lens, which is dark.
When the solder joint is pseudo-welded, the similar plane of the solder joint as shown on the left of the figure above will enter the lens and show bright colors. Therefore, this feature can be used to test the welding condition of the solder joint. This is the principle of testing the solder joint
RGBW lighting principle Refraction and reflection detection principle
But AOI can not detect circuit problems, at the same time can not detect invisible solder joints.
X - RAY: X-ray, X-ray inspection equipment, using high pressure accelerated electrons to release the X RAY, RAY through the PCB board and leave the image. Due to the increasing precision of electronic products and the increasing number of bottom pad packaging devices, special X-ray related equipment is needed for detection.
Technicians observe the gray scale of PCB board solder joint through the brightness of the image, and can detect the following defects: PCB circuit disconnection, IC welding, BGA short circuit less tin welding, THT through hole tin deficiency, etc.
In summary, combined with the SMT process production characteristics, the R&D personnel need to consider whether there is enough process edge reserved in the design layout, the general requirement is 3-5mm, how many parts should be used in the design of the plate, different from the layout of mobile phone is that it is not suitable to adopt the Yin and Yin plate layout, the selection of individual components considering the weight of the device, the second side of the reflux will have the risk of device falling. Device selection needs to consider whether it can be mass-produced, need to burn the device whether there is a suitable package, such as the incoming material is coil packaging after burning is impossible to package back;