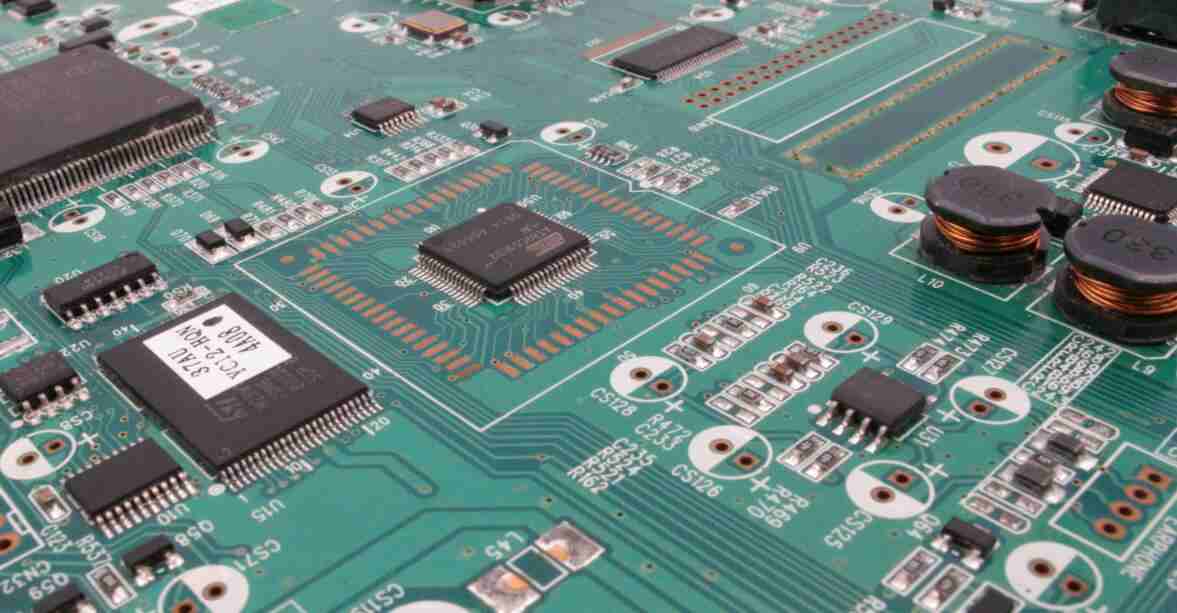
Tri-proof paint is a specially prescribed paint used to protect the circuit board and its associated facilities from environmental denudation. Three anti paint has satisfactory high and low temperature resistance; After curing, it forms a transparent film, which can be used to protect circuits from damage under conditions such as chemical substances (e.g. combustion materials, coolants, etc.), shock, moisture, salt spray, moisture and high temperature. Under these conditions, the circuit board may be corroded, mold growth and short circuit initiation, etc., with excellent insulation, moisture-proof, anti-leakage, dust-proof, anti-corrosion, anti-aging, anti-mildew, anti-loosening parts and insulation resistance to corona.
Three anti paint effect
Moisture is the most widespread and damaging main factor to PCB circuit boards. Excessive moisture will greatly reduce insulation resistance between conductors, accelerate high speed decomposition, reduce Q value, and corrode conductors. We often see PCB circuit board metal local copper rust is not coated with three anti-paint metal copper and water gas, oxygen gas side by side its chemical reaction.
The three anti paint coating on the printed circuit board and components can reduce or eliminate the fading state of electronic operating performance when it is possible to suffer from adverse operating background factors. The coating is considered to have achieved its coating objective if it retains its effectiveness for a good period of time, such as beyond the product's service time limit.
Three anti-paint components
Acrylic products
Acrylic three anti - paint soft and strong toughness can provide all aspects of the best care. Because it is a single component system, with good adhesion, simple operation, not high requirements for facilities and conditions, convenient construction, high openness, high brightness, short operation cycle and other unique places, so they are easy to use and easy to clean. Some acrylic products are satisfied with military standards, they dry quickly and dry, can be composed of a set of organic solvents to clean it up, so this type of circuit board is one of the most widely used and most useful products on the market.
Is three anti paint toxic?
Three anti-paint toxic depends on the use of three anti-paint thinner and solvent type, if the use of three anti-paint with toluene, xylene as diluent, this chemical is harmful to human health, if it is considered appropriate and the use of fats, alcohols and other less harmful. Xylene has moderate and common toxicity, has a very irritating effect on the eyes and respiratory tract, high liquid concentration, has anesthetic effect on the central system.
Although there are a lot of so-called environmental protection three anti-paint on the market, but in the actual application, we still have to do a good job of preparedness protection treatment, use wear gas shield face things, etc.
Three anti - paint application process has the following four listed
1, brush - there is a wide range of use, can be in the flat and smooth appearance of the initiation of excellent coating effect.
2, spraying - the use of spray can products can be easily applied to maintenance and small production, spray gun is suitable for large-scale production, but the two forms of spraying for the correctness of the operation is higher, and it is possible to initiation of shadow (the lower part of the component is not covered with three anti-paint).
3, semi-automatic dipping - dipping can ensure the absolute coating, and will not lead to the material consumption caused by excessive spraying.
4, selective coating film - coating is correct and does not cost material, suitable for use in a large amount of coating film, but the coating facilities have higher requirements. Most suitable for use in a large amount of film. The use of a woven XY table, detractable coverage. printed board painting, there are many connectors without spraying paint. Adhesive paper is too slow and tear time there is a lot of glue left, can consider the problem according to the plug-in style, volume, position, do a combined cover, positioning with the installation hole. Cover areas that do not need to be painted.
Three anti-paint operation process requirements
1, cleaning and drying board, remove moisture and nutrients. Dust, moisture and oil should be removed from the surface of the object to be painted so that it can exert its best care. Thorough cleaning can ensure that the corrosive residue is absolutely swept away, and make the three anti paint stick beautifully on the circuit board appearance. Drying conditions: 60 degrees, 10-20 minutes, in the oven after extraction while hot coating effect is better;
2, with the brush coating method, brush coating flat surface or object surface size should be larger than the parts of the plane or object surface size, in order to protect all covering parts and pads;
3. When brushing the plate, try to lay flat, there should be no dettol after brushing, the brush should be smooth, and the local area should not be exposed, between 0.1-0.3mm is appropriate.
4. Before brushing and spraying, ensure that the diluted product is fully mixed, and put it in place for 2 hours before brushing or spraying. Use a high quality naturally occurring fiber brush and apply lightly at room temperature. If machinery is used, the viscosity of the paint should be investigated (with viscosity agent or flow cup), and the viscosity can be adjusted with diluent.
5. The circuit board components should be immersed straight into the paint grains. The co-distributor should not be immersed. The fault should not be covered carefully. The circuit board should be immersed for 1 minute until the bubbles disappear, and then not taken out quickly. The outer surface of the circuit board forms an average film layer. Most of the paint residue should be allowed to flow from the circuit board back to the impregnator. TFCF has different coating requirements. The immersion speed of circuit board or component is not too fast, so as not to generate too many bubbles.
6. After dipping and coating, when it is used again, if there is crust on the surface, remove the skin, it can be used.
7. Flat on the support after brushing, ready for curing, need to use heating method is to accelerate the curing of the coating. If the coating appearance is unfair or includes bubbles, in the high temperature furnace curing should be placed at room temperature more time in order to let the solvent flash out.
Keep an eye on things
1. If a thicker coating is desired, it is best to obtain it by applying two thinner coats -- and the first coat must be absolutely dried before the upper coat is allowed.
2. When painting the PCB, coating materials are not allowed in the common joint distributor, software socket, switch, heat dissipation device, heat dissipation area, plug-in area, etc., and it is proposed to use tear solderproof adhesive to cover.
3. Thickness of the film layer: the thickness of the film layer depends on the application method. The amount of diluent is large, the viscosity of the glue is low, and the thickness of the glue is thin. On the contrary, the viscosity of the glue is high and the thickness of the glue is thick.
4. All coating operations shall be carried out under the conditions of not less than 16℃ and less than 75% relative humidity. PCB board as a composite material will absorb moisture. If you do not go to the tide, the three anti paint can not fully take care of the effect. Pre-drying and vacuum drying can remove most moisture.
Method of repairing parts that have been coated
If the parts that have been coated are repaired, the component can be removed by directly contacting the coating with the soldering iron. After installing the new component, the area can be cleaned and cleaned with a brush or solvent, and then dried and covered with new paint.