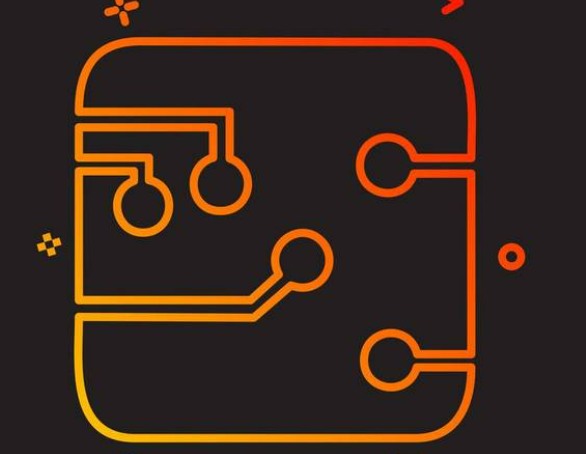
In PCB industry, POFV is a circuit board design, the process is as follows:
1. Opening and drilling
According to the requirements of engineering data MI, the large sheets that meet the requirements are cut into small pieces for production. In line with customer requirements of a small piece of board, according to the engineering data, in line with the required size of the board, the corresponding position to drill out the desired aperture.
2. Sinking copper
Copper deposition is a chemical method to deposit a thin layer of copper on the wall of the insulating hole.
3, graphic transfer, electroplating, film retreat
Graphic transfer is the transfer of the image on the production film to the plate, plating a layer of copper and gold nickel or tin of required thickness on the exposed copper or hole wall of the line graphic. NaOH solution is used to recede the anti-plating covering film to expose the non-line copper layer.
4, green oil, tin plate, test
PCB proofing production circuit board some special technology
1. Impedance control
When the digital signal is transmitted on the board, the characteristic impedance value of the PCB must match the electronic impedance of the head and tail components. Once mismatch occurs, the transmitted signal energy will be reflected, scattered, attenuated or delayed. In this case, impedance control must be performed to match the PCB's characteristic impedance values to the components.
2. HDI blind hole burial
A blind hole is only visible at the top or one of the bottom layers; The buried hole is the inner layer through the hole, the upper and lower sides of the hole are in the inner layer of the board. The application of blind burials greatly reduces the size and quality of HDI (high density interconnect) PCB, reduces the number of layers, improves electromagnetic compatibility, reduces costs, and makes the design work more convenient and fast.
3, thick copper plate
A layer of copper foil is bonded to the outer layer of FR-4. When the finished copper thickness is ≥2oz, it is defined as thick copper plate. Thick copper plate has excellent extensibility, high temperature and low temperature resistance, corrosion resistance, so that electronic products have a longer service life, and the product volume simplification is of great help.
4. Multi-layer special laminated structure
Laminated structure is an important factor affecting EMC performance of PCB board and an important means to suppress electromagnetic interference. The more the number of signal networks, the higher the density of devices, the higher the PIN density and the higher the frequency of signals, the more special multilayer structure should be adopted in the design.
5, electroplating nickel gold/gold finger
Electroplating nickel gold refers to the way through electroplating, so that gold particles attached to the PCB board, because of the strong adhesion, known as hard gold; The process can greatly increase the hardness and wear resistance of PCB, effectively prevent the diffusion of copper and other metals, and meet the requirements of hot pressing welding and brazing. Coating uniform fine, low porosity, low stress, good ductility.
6. Nickel palladium
Nickel palladium is a non-selective surface processing process in PCB proofing, which uses a chemical method to deposit a layer of nickel, palladium and gold on the surface of the printed line copper layer. It makes PCB board achieve good electrical conductivity, corrosion resistance and friction resistance through 10 nm thick gold coating and 50 nm thick palladium coating.
7. Countersunk hole
Countersunk hole is generally used to drill holes on the board with a flat head drilling needle or gong knife, but can not drill through (that is, half through hole). The transition part of the hole wall at the outer/maximum aperture and the hole wall at the most small hole is parallel to the pcb surface, and the part connecting the big hole is a plane, not an inclined plane.
Fanyi PCB design Company to military quality PCB design requirements
PCB design can not be arbitrary, there are certain rules. Fanyi circuit military quality PCB design has the following requirements:
The PCB layout design shall follow the following principles:
1. Arrange the location of components reasonably and increase the density of components layout as far as possible, so as to reduce the length of wire, control crosstalk and reduce the size of printed board surface;
2. Logic devices with signals in and out of the printed board should be placed near the connector as far as possible, and arranged in the order of circuit connection as far as possible;
3, partition layout. According to the logic level, signal conversion time, noise tolerance and logic interconnection of components used, measures such as relative partition or strict separation of circuits are adopted to control the crosstalk noise of power, ground and signal.
4, uniform layout. The whole panel shall be arranged neatly and orderly. The distribution of heating components and wiring density should be uniform;
5, meet the heat dissipation requirements. When air cooling or heat sink is needed, air duct or sufficient heat dissipation space should be set aside; The liquid cooling mode should meet the corresponding requirements;
6, high-power components should not be arranged around the heat-sensitive components, and maintain sufficient distance from other components;
7. When large weight components need to be installed, they should be arranged near the support point of the printed board as far as possible;
8. The installation, maintenance and testing requirements of components shall be met;
9. Many factors such as design and manufacturing costs should be taken into account.
01. Wiring area. The following factors should be considered in determining the wiring area:
1.1 Types and quantities of components to be installed and wiring channels for interconnection of these components;
1.2 Conductive graphics (including power layer and ground layer) should be no less than 1.25mm away from the frame of the printed board without touching the wiring area of the printed wire during contour processing;
1.3 The distance between the conductive figure of the surface layer and the guide rail groove shall be no less than 2.54mm. If the guide groove is used for grounding, the ground wire should be used as the frame.
02. Wiring rules. PCB wiring should generally follow the following rules:
2.1 The number of wiring layers of printed conductors shall be determined as required. Wiring occupied channel ratio should generally be more than 50%;
2.2 According to the process conditions and wiring density, wire width and wire spacing should be reasonably selected to ensure uniform wiring within each layer and similar wiring density of each layer. If necessary, auxiliary non-functional connecting plates or printed wires should be added to the missing area;
2.3 The adjacent two layers of wires should be arranged into vertical oblique or curved lines to reduce the parasitic capacitance;
2.4 Printed wire wiring should be as short as possible, especially high-frequency signal and highly sensitive signal lines; For important signal lines such as clocks, equal delay wiring should be considered when necessary;
2.5 When multiple power sources (layers) or ground (layers) are deployed on the same floor, the separation spacing shall not be less than 1mm;
2.6 Windows should be partially opened for large area conductive graphics larger than 5×5mm².
2.7 The thermal isolation design should be carried out between the large-area graphics of the power layer and the ground and their connecting plates, as shown in Figure 10, so as not to affect the welding quality;
2.8 Special requirements of other circuits shall comply with relevant regulations.
03. Wiring sequence. In order to achieve the optimal wiring of printed boards, the wiring sequence should be determined according to the sensitivity of signal lines to crosstalk and the requirements of wire transmission delay. Priority wiring of signal lines should be as short as possible its interconnect. Generally, wiring should be done in the following order:
3.1 Analog small signal line;
3.2 Signal lines and small signal lines that are particularly sensitive to crosstalk;
3.3 System Clock Signal Cable;
3.4 Signal cables with high transmission delay requirements;
3.5 General signal cables;
3.6 Static potential line or other auxiliary line.