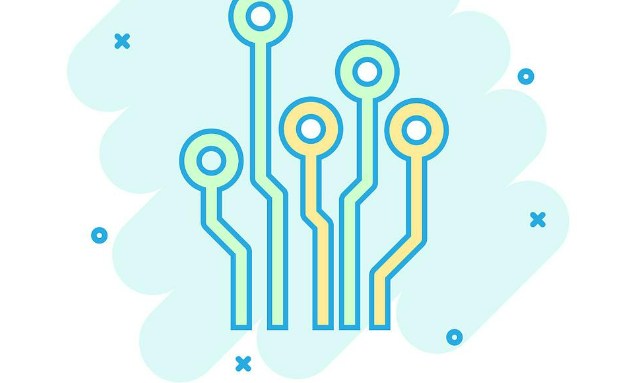
The analysis and design of power supply systems(PDS) are becoming increasingly important in the field of high-speed circuit design, especially in the computer, semiconductor, communication, network and consumer electronics industries. With the inevitable further scaling down of VLSI technology, the supply voltage of IC will continue to decrease. As more manufacturers move from 130nm to 90nm, expect supply voltages to drop to 1.2V or even lower, while the current will increase significantly. From DC IR voltage to AC dynamic voltage fluctuation control, due to the allowed noise range is becoming smaller, this development trend brings great challenges to the design of power supply system.
Usually in AC analysis, the input impedance between power sources is an important measurement used to measure the characteristics of a power supply system. The determination of this observation has evolved into the calculation of IR pressure drop in DC analysis. Whether in DC or AC analysis, the factors affecting the characteristics of the power supply system are: PCB layering, the shape of the power supply board layer plane, the layout of the components, the distribution of holes and pins, and so on.
The concept of input impedance between power sources and ground can be used in the simulation and analysis of the above factors. For example, a very broad application of the ground input impedance of a power supply is to evaluate the placement of decoupling capacitors on a board. With a certain number of decoupling capacitors placed on the board, the characteristic resonance of the board itself can be suppressed, thus reducing the generation of noise, and the edge radiation of the board can be reduced to alleviate EMC problems. In order to improve the reliability of power supply systems and reduce the manufacturing cost of systems, system design engineers must often consider how to cost-effectively select the system layout of decoupling capacitors.
The power supply system in high speed circuit system can be divided into chip, integrated circuit package structure and PCB three physical subsystems. The power grid on the chip is composed of several metal layers placed alternately. Each metal layer is composed of thin metal strips in the X or Y direction to form the power or ground grid. The holes connect the thin metal strips in different layers.
For some high performance chips, both kernel and IO power supply are integrated with a number of decoupling units. Integrated circuit package structure, like a reduced size PCB, has several layers of complex shape power supply or floor plate. On the upper surface of the package structure, a location for mounting the decoupling capacitor is usually reserved. PCBS usually contain a continuous large area power supply and floor plate, as well as a number of large and small discrete decoupling capacitors, and power supply rectifier modules (VRMS). The Bonding line, C4 bump and solder ball connect the chip, package and PCB together. The whole power supply system should ensure that each integrated circuit device provides stable voltage within the normal range. However, switching currents and parasitic high-frequency effects in those power-supply systems always introduce voltage noise.
Analysis of PCB process faults of debris in hole wall and aperture enlargement
PCB process failure: residual chips appear in the hole wall
Reasons:
(1) The cover plate or substrate material is inappropriate
(2) Cover pulling causes drill bit damage
(3) The vacuum pressure at the center of the spring fixing bit is insufficient
(4) The pressure foot gas supply pipeline is blocked
(5) The spiral Angle of the drill is too small
(6) Excessive laminated layers
(7) Drilling process parameters are incorrect
(8) The environment is too dry to produce electrostatic adsorption
(9) The knife retreat rate is too fast
Solution:
(1) Select or replace the appropriate cover plate and substrate material.
(2) Choose suitable hardness of cover plate material. Such as No. 2 rust-proof aluminum or composite cover plate.
(3) Check the vacuum system of the machine (vacuum degree, pipeline, etc.).
(4) Replace or clean the pressure foot.
(5) Check whether the drill complies with the standard technical requirements.
(6) The number of laminated layers shall be reduced according to the technological requirements.
(7) Select the best feed speed and bit speed.
(8) According to the technical requirements to meet the specified humidity requirements should reach the humidity of 45%RH above.
(9) Select the appropriate knife retreat rate.
PCB process failure: aperture enlargement
Reasons:
(1) There is a problem with drill diameter
(2) When the drill is broken in the hole, the aperture becomes larger
(3) caused by the repair of leakage holes
(4) Errors caused by repeated drilling of positioning holes
(5) Caused by repeated drilling
Solution:
(1) Drill bit diameter must be carefully measured before drilling.
(2) The part of the drill broken in the hole shall be pushed out.
(3) Pay attention to the diameter of drill bit when filling holes.
(4) The positioning hole position and dimensional accuracy should be re-selected.
(5) Special attention should be paid to the diameter of the borehole.