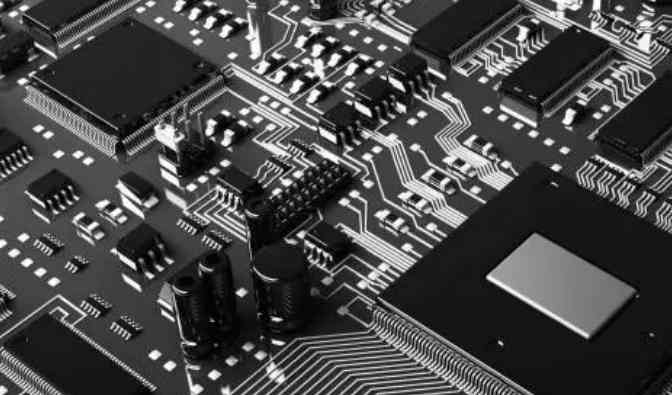
1. Spacing between patches
The spacing between patch components is a problem that engineers must pay attention to in layout. If the spacing is too small, it is very difficult to print solder paste and avoid soldering tin.
Distance suggestions are as follows
Device distance requirements between patches:
Same device: ≥0.3mm
Dissimilar devices: ≥0.13*h+0.3mm (h is the maximum height difference of nearby components)
The distance between components that can only be manually placed is required to be ≥1.5mm.
The above suggestions are for reference only, according to the PCB design process specification
2. Distance between in-line device and patch
A sufficient distance should be kept between the in-line resistance device and the patch. It is recommended that the distance should be between 1-3mm. Due to the trouble of processing, there are few cases of using the in-line plug-in.
3, for the IC decoupling capacitor placement
The decoupling capacitor must be placed near the power port of each IC as close as possible to the IC power port. If a chip has multiple power ports, the decoupling capacitor must be placed at each port.
4. Attention should be paid to the direction and distance of components placed on the edge of PCB board
Since PCBS are generally made with a patchwork board, the device near the edge needs to meet two conditions.
The first is to be parallel to the cutting direction (so that the mechanical stress of the device is even. For example, if the device is placed in the way on the left of the figure above, when the plate is to be split, the different stress directions of the two welding pads may lead to the fall off of the element and the pad)
The second is that the device cannot be arranged within a certain distance (to prevent damage to the components when the board is cut).
5. Attention should be paid to the fact that adjacent pads need to be connected
If the adjacent pad needs to be connected, first confirm the connection on the outside to prevent the bridge caused by a ball, and pay attention to the width of the copper wire at this time.
6, if the pad falls in the ordinary area need to consider heat dissipation
If the pad falls in the paving area, the right way should be adopted to connect the pad to the paving, and determine whether to connect 1 wire or 4 wires according to the size of the current.
If the left way is adopted, it is more difficult to weld or repair and disassemble components, because the temperature is fully dispersed through the copper paving, resulting in the welding of the fish.
7. If the lead is smaller than the plug-in pad, you need to add tears
If the wire is smaller than the pad of the in-line device, you need to add a tear drop in the way shown on the right.
Adding teardrops has the following benefits:
(1) Avoid reflection caused by sudden reduction of signal wire width, which can make the connection between the wire and the component pad smooth transition.
(2) It solves the problem that the connection between the pad and the wire is easy to break under the impact force.
(3) The setting of tear drops can also make the PCB board appear more beautiful.
8. The lead width on both sides of the component pad should be consistent
9. Keep the pad without pins and ground it
For example, two pins of a chip in the figure above should not be used, but physical pins of the chip exist. If the two pins are in a state of suspension as shown on the right of the figure above, it is easy to cause interference. Interference can be avoided by adding a pad and grounding the pad.
10. It is best not to hit the welding pad through the hole
Note that it is best not to hit through the hole on the pad, easy to cause tin leakage welding.
11. Pay attention to the distance between wires or components and the edge of the plate
Note that the lead or components can not be too close to the edge of the plate, especially the single panel, the general single panel is mostly paper board, easy to break after the force, if in the edge line or put components will be affected.
12, must consider the environmental temperature of the electrolytic capacitor away from the heat source
Firstly, whether the ambient temperature of the electrolytic capacitor meets the requirements should be considered. Secondly, the capacitor should be kept away from the heating area as far as possible to prevent the liquid electrolyte inside the electrolytic capacitor from being dried.
Coatings are widely used in diesel and gasoline cars, but do hybrid or electric cars also need coatings?
With the rapid adoption of electric vehicles and ADAS and autonomous driving technologies, as well as the increase of infotainment facilities in cars, the automotive industry's demand for electronic products has increased dramatically. At the same time, the demand for three-proof paint is also growing.
To make electric cars last longer on each charge, one of the solutions is to make them as light as possible. Electronics design engineers need finer spacing on circuit boards to minimize the size of the electronics. In ADAS and other applications, the very low fault tolerance means that a high level of protection must be applied to the circuit board against environmental factors such as humidity, condensation, temperature changes, corrosive gases, and other contaminants.
Protecting electronics from the environment is important, but so is insulating the components on the circuit board. It is essential to use high dielectric strength materials that can resist higher voltages before breakdown.
Three-proof paint can meet such challenges. Three anti paint can not only provide a strong protective barrier against the external environment, but also can provide fine component spacing required insulation resistance. All of these factors provide a high level of protection in a lightweight solution. Hybrid and electric vehicles have a huge demand for triple-proof paint, but these two types of applications have very strict requirements, which means more pressure to solve the problem.
What common applications will the automotive industry use coatings in?
The potential applications of three anti - paint can be said to be unlimited. As long as the PCB needs light quality protection, then the triple anti paint is the ideal solution.
Automotive coating applications include sensors in ADAS and other support applications. Examples include ADAS control unit PCBS, or powertrain applications such as battery management system PCBS, charger PCBS, alternators, DCS, DC converters and transfer switches.
In addition, coatings are also needed to protect electronics in automotive infotainment systems, interior and exterior lighting, air conditioning systems and other electronic control systems. There are many electronic products in the car need to use three anti paint, too numerous to list.
We move from the cars themselves to the charging infrastructure, which is exposed to a variety of weather conditions: heat, cold, humidity and corrosion, especially near coastlines. It is necessary to arrange a safe and reliable charging station network for the convenience of the driver to charge the car, so the charging point should also be included in the potential application of the three anti-paint.
Bio-based coatings, especially those that use more sustainable raw materials in their raw materials, have well demonstrated that triple-proof paints perform well in electric vehicles and other automotive applications.
The lighter quality of the three-proof paint not only meets the manufacturer's requirements for product sustainability, but also shows better anticoagulability, thermal stability, flexibility and adhesion in the end-use environment compared to many petrochemical derived polymers.