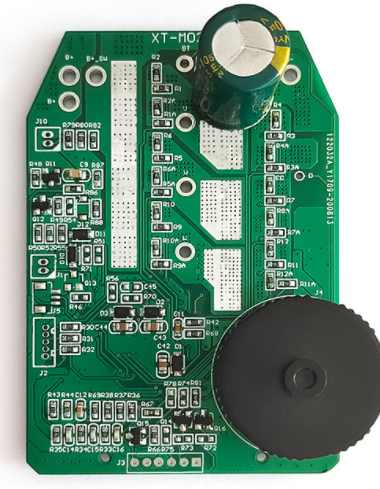
The circuit board of our common electronic products, that is, we often say PCBA, is manufactured by SMT patch processing and DIP plug-in processing. Due to the fine and integrated components of the patch in PCBA processing, especially for SMT patch processing technology is relatively technical content. In order to ensure the patch processing quality intact, we must master the corresponding technical points. Next, Shenzhen patch processing manufacturer -kingford- share SMT patch processing technology points with you, I hope to bring you some help!
I. Main points of solder paste printing technology
1, the Angle of the printing press scraper and steel mesh: the smaller the Angle of the scraper and steel mesh, the greater the pressure of the scraper, easy to squeeze the solder paste to the bottom of the steel mesh, causing tin short circuit. Steel mesh scraper Angle is generally 45~60°
2. Scraper pressure: Scraper pressure refers to the depth of the scraper falling to the steel mesh surface, which is also an important factor affecting the printing quality. When the pressure is too small, the scraper is not close to the steel mesh surface, so it is equivalent to increasing the thickness of solder paste printing. Moreover, a layer of solder paste remains on the surface of the steel mesh, which is easy to cause the pointed defect of the printed solder paste when demoulding.
3, scraper speed: scraper running speed and solder paste viscosity is inversely proportional. When PCBA has a narrow spacing pad, the printing speed should be slow, the speed is too fast, the shorter the time that the scraper passes through the steel mesh opening, the solder paste can not fully penetrate into the steel mesh. Easy to cause solder paste printing is not full or leakage defects.
4. Printing gap: printing gap is the fit degree between steel mesh and PCB, which is related to the storage of printing solder paste on PCBA pad. The fit between the two is too tight, easy to cause deformation of steel mesh. On the contrary, it is easy to cause the printing solder paste to be too thick, and it is easy to form short circuit.
5. Demoulding speed: The instant speed of steel mesh leaving PCBA after solder paste printing is completed is the demoulding speed, which is an important parameter related to the printing quality. Demoulding speed is too fast, the adhesive force of solder paste will be reduced, easy to cause the phenomenon of solder paste wire drawing or point pulling.
Two, SMT SMT machine technical points
SMT machine is one of the key equipment in SMT processing. Because of the high speed, high efficiency, stable performance, to our PCBA processing has brought a huge advantage. SMT SMT SMT SMT SMT SMT SMT SMT machine technology points can be summarized in three words: accurate patch, patch good, patch fast.
(1) Correct installation of components: The type, size, resistance value and polarity of components on each side of the PCBA surface shall meet the requirements of the assembly drawing and BOM list, and shall not be pasted incorrectly. ② Accurate component mounting: Component mounting should be aligned and centered with PCBA screen printing as far as possible. For more precise devices, the actual printed solder paste graphic alignment shall prevail.
2. Good patch: ① do not damage components: the patch machine may damage components when picking up and mounting because of the error of the feeder, components and printed board, leading to the failure of the patch. (2) Suitable patch pressure: the patch pressure should be suitable, the patch pressure is too small, the welding end or pin of the components float on the surface of the solder paste, the solder paste does not stick to the components, and the azimuth movement is easy to occur when transferring and reflow welding; Too much pressure on the patch, too much extrusion of solder paste, simple adhesion of solder paste, easy short circuit during reflow welding, too much pressure will even damage components. ③ Guarantee the mounting rate: because the parameter adjustment of the mounting machine is unreasonable or the reason of the feeder, the components fall in the mounting process, this phenomenon is called "throwing". In practice, it is measured by the mount rate. When the mount rate is below the booking level, the reason must be found.
3. Fast SMT: Usually, there are hundreds to thousands of electronic components on a PCBA board, which are pasted to the PCBA board one by one through the SMT machine. The mounting speed is the basic requirement of SMT patch production capacity. The mounting speed mainly depends on the speed of the mounting machine, but also closely related to the optimization of the mounting process and the use of equipment.
Three, reflow technical points
1. Reasonable reflow welding temperature curve should be set and real-time test of temperature curve should be done regularly. 2, according to the design of PCBA welding direction transmission welding. 3. Prevent the vibration of the conveyor belt during reflow welding. 4. The welding effect of the first printed board must be tested for the mechanical strength of the solder joint. 5. Check whether the welding is sufficient, whether the surface of the solder joint is smooth, whether the shape of the solder joint is in half moon shape, the condition of the tin ball and residue, and the condition of continuous welding and virtual welding.
2.SMT Patch factory
kingfordSMT technical experts and more than years of technical team, to create a rapid response service system and stable and reliable technical support, in the field of PCBA welding to establish lean, reliable, convenient product delivery services; It is a reliable SMT patch factory that provides comprehensive solutions of OEM and ODM technology to reduce the cost and increase the efficiency of electronic hardware and help products move steadily towards the market.
Our service cases are mainly in industrial control, medical, communications, security, Automotive electronics, instrument and instrument industries, the service content covers the whole PCBA welding processing and manufacturing process. Including PCB Layout, component collection, SMT patch processing, DIP plug-in processing, test assembly, failure analysis. Through our professional services, can make the product get real production and supply of stable and reliable double guarantee. Over the years of PCBA manufacturing services, we have worked with customers in a variety of industries to complete more than 6000 product introductions and process improvements. kingford is a company integrating PCBA welding processing and PCBA technical services. Through years of precipitation of PCBA manufacturing services, kingford has formed a standard specification of PCBA manufacturing technology, and made full use of our expertise to help customers solve many problems in production and supply.
I. Process capability of SMT patch processing plant
1. SMT 7 production lines, 15 million points/day; Minimum mountable 0201Chip-0.3mm Pitch BGA; Mounting accuracy is 0.03mm; Mounted PCBA size 50* 50mm-510 *460mm; 2, components from quality customers for many years selection of supply channels, full BOM collection of authentic original guarantee. Strict and standard 100%IQC incoming material inspection and sample bearing management of 12000+ stock SKUs; 3. Two DIP production lines, 300,000 points/day; Wave soldering PCBA plate size width 50-450mm; Post welding wire 4, post welding capacity of 10,000 sets/day; 4, 12 test workbench, can accommodate 24 test stations, test capacity of 3000 sets/day; 5 meters assembly line, can accommodate 30 assembly stations, assembly capacity of 3000 sets/day; 5. SMT patch proofing will be delivered in 8 hours; Real PCBA - station service (PCB board making + component collection +PCBA welding processing + assembly, testing and fitting + sporadic technology);
Ii. Quality control of SMT patch factory
1, from quality customers for many years selection of supply channels, unified collection of authentic original guarantee. 2, strict and standard 100%IQC incoming material inspection and sample bearing management, resist receiving bad materials. 3, the international first-line quality accessories, high reliability, high stability of the model, sample bearing, testing, full ROHS environmental requirements. 4. BOM inspection tool is embedded in the special inspection software to optimize material description, model, dosage, bit number, package, brand and other parameters. 5. According to PCBA product model and process characteristics, optimize the whole process SOP and process parameters, and form a standardized process parameter file. 6. SMT quick sample making and delivery in 8 hours; Real PCBA welding processing - station delivery (PCB board manufacturing + component collection + patch processing + assembly, test and assembly);
Three, the advantages of SMT processing plant
1, PCBA welding processing products do not pick batch, only pick quality; 2. High mixing degree, standardized batch production of the whole process; 3, high difficulty, 01005/0201/BGA/CSP; 4, superior quality, ISO9001:2015/13485:2016 / IPC/zero defect system; 5, fast delivery, SMT patch proofing 8 hours delivery; PCB+ components (PCBA)+ assembly, testing, truly PCBA welding processing one-stop service; 6. Complete BOM component set, effectively reduce cost, and realize zero inventory of materials in one step;
Four, choose SMT patch factory -kingford
Choose kingford = choose a professional SMT processing plant; Select kingford = Select a component repository; Select kingford= select a reliable SMT patch factory. A team of senior engineers in the electronics industry, many years of industrial grade PCBA welding production and manufacturing experience, completed product introduction and process improvement more than 6000 times, to provide customers with accurate PCBA welding process solutions. From product progress deduction, order instruction, data review and refinement, SOP guidance and manufacturing, production management can be controlled throughout the whole process. 100%AOI inspection of solder joints, the highest qualified rate of products is as high as 99.7%. For you to achieve material "0" inventory, product "0" defect. Is your trusted SMT factory.