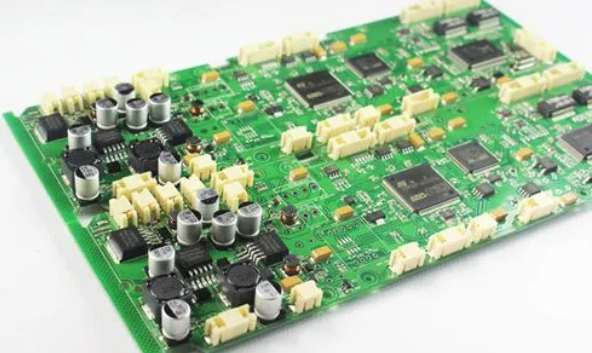
Often see a lot of industrial control board or radio frequency board in the PCB board around will play a circle of holes and copper belt, even some radio frequency board will be around the edge of the board metallized edge, what is the routine to do this?
The edge radiation of multilayer PCB is a common source of electromagnetic radiation
Nowadays, with the increase of system speed, not only the timing and signal integrity problems of high-speed digital signals are prominent, but also EMC problems caused by electromagnetic interference and power supply integrity caused by high-speed digital signals in the system are also prominent. The electromagnetic interference generated by high-speed digital signals will not only cause serious interference inside the system and reduce the anti-interference ability of the system, but also produce strong electromagnetic radiation into the outer space, causing the electromagnetic radiation emission of the system to seriously exceed the EMC standard, so that the product cannot pass the EMC standard certification. The edge radiation of multilayer PCB is a common source of electromagnetic radiation.
Edge radiation occurs when an unexpected current reaches the edge of the ground layer and the power layer. These unexpected currents may come from:
- Ground and power noise caused by insufficient power bypass.
- A cylindrical radiating magnetic field generated by the inductive hole, which radiates between the layers of the board and eventually meets at the edge of the board.
- The reflux current of the strip carrying the high frequency signal is too close to the edge of the circuit board.
Source of power supply noise
The source of power supply noise mainly lies in two aspects: first, the transient alternating current is too large in the high-speed switching state of the device; The second is the inductance existing in the current circuit. From the form of expression, it can be divided into three categories:
- Synchronous switching noise (SSN), sometimes referred to as ΔI noise, can also be attributed to the phenomenon of Ground bounce;
- Influence of non-ideal power supply impedance;
- Resonance and edge effect.
In high-speed digital circuit, when the digital integrated circuit is powered on, its internal gate output will be from high to low or from low to high state transition, that is, the conversion between "0" and "1". In the process of change, the transistor in the gate circuit will keep on and off, then there will be a current from the power supply into the gate circuit, or from the gate circuit into the ground plane, so that the power plane or ground plane current imbalance, resulting in a momentary change of current △I. This current creates an AC voltage drop as it flows through the inductors present on the return path, causing noise. This voltage drop is large enough to cause power integrity problems if there are a large number of output buffers simultaneously performing state transitions, and this Noise is known as Simultaneous Switch Noise (SSN).
The AC noise of the power supply will be transmitted between the power supply layer and the ground. The resonant cavity mode of the two planes will be used to conduct AC noise. When transmitted to the edge of the plane, the AC noise will radiate into the free space, which will lead to the EMI certification of the product.
As for the noise generated by passing holes, we know that the interconnected signal lines on PCB include the microstrip line on the outer layer of pcb and the strip line between two planes in the inner layer, as well as the electroplating through holes (through holes are subdivided into through holes, blind holes and buried holes) that are connected by signal layer-changing. The microstrip line in the surface layer and the strip line between the two planes can control the radiation well through good reference plane overlapping structure design.
The through-hole runs through multiple layers vertically. When the high-frequency signal transmission line passes through the through-hole to change layers, not only the impedance of the transmission line changes, but also the reference plane of the signal return path changes. When the signal frequency is relatively low, the influence of the through-hole on signal transmission can be ignored. As the change of the reference plane of the pass hole causes the change of the current return path, the TEM wave generated by the pass hole will propagate laterally between the resonant cavity formed on the two planes and eventually radiate outward into the free space through the edge of the pcb, resulting in the excessive EMI index.
OK, now we know that for high frequency and high speed PCB, edge radiation will be generated on PCB board edge. Then how to protect?
Protective measures of multilayer PCB board edge radiation
EMC problems are caused by the three elements: electromagnetic interference source, coupling path, and sensitive equipment
Sensitive equipment we can not control, cut off the coupling path such as adding a metal shield equipment shell, etc., here is not to say, the remaining how to kill the source of interference.
First of all, the wiring of key signals on PCB should be optimized to avoid EMI problems, which are more than the through holes of layer change. We can lay ground through holes around the through holes of key signals to provide additional return path for the through holes of key signals.
Well, for the reduction of PCB edge radiation, I have heard of a 20H rule, which was first proposed by W.Michael King in 1980 and elaborated by Mark.I. Meltrose in his book, and is valued by the business and is often listed as an important EMI design rule. H refers to the thickness of the board, that is, the distance between the power plane and the ground plane is reduced by 20H.
In order to reduce the edge radiation effect, the power plane should be smaller than the adjacent plane, and the effect is not obvious when the power plane is smaller for about 10H. When the power plane is shrunk for 20H, 70% marginal Flux Boundary is absorbed. When the power plane is shrunk for 100H, 98% of the marginal flux boundary can be absorbed. Therefore, the internal power layer can effectively suppress the radiation caused by marginal effect.
The 20H rule is not suitable for the current high frequency and high speed PCB design. The former printed circuit board has a large area, and the resonance frequency of the plane antenna caused by shrinkage is not obvious. Nowadays, due to the small PCB board surface, the radiation intensity of the design of the inner power layer changes significantly with the resonant points of different inner power layer sizes, resulting in higher radiation energy at high frequency.
The reduction of radiation cannot be completely solved by using 20H contraction. Although the frequency below 430MHz is improved, and the frequency below 590MHz is improved by 40H, the resonance frequency becomes higher due to the area reduction, which is not helpful for radiation suppression in the frequency band with higher resonance frequency.
In the future design of EMI, because the internal power layer 20H will not be helpful, and the smaller the board, the more high frequency radiation will be more serious due to the change of plane antenna effect, so the theory of 20H is not in line with the current practical needs.
Since the 20H rule has become invalid for the current high frequency and high speed PCB design, it is necessary to use a shielding structure to deal with the edge of pcb board edge radiation as a source of interference, so as to reflect the noise back into the inner space, which will increase the voltage noise on these layers, but reduce the edge radiation.
Low cost method of radiation protection for multilayer PCB board edge
The low-cost implementation method is to make a circle of grounding holes around the PCB at 1/20 wavelength hole spacing to form a grounding hole shield to prevent TME wave radiation.
For the microwave circuit board, its wavelength becomes smaller, and due to the PCB production process, the spacing between holes and holes can not be made very small, at this time has 1/20 wavelength spacing around the PCB to play a shielded hole around the microwave board effect is not obvious, then it is necessary to use the PCB version of metallized edge wrapping process, the whole board edge surrounded by metal, Thus, microwave signals cannot radiate out from PCB board edge. Of course, the use of board edge metallization edge wrapping process will also lead to a lot of increase in PCB manufacturing costs.
For RF microwave plate, some sensitive circuits, as well as circuits with strong radiation sources can be designed to weld a shielding cavity on the PCB, PCB in the design to add the "hole shielding wall", that is, on the PCB and the shielding cavity wall close to the part of the ground hole. This creates a relatively isolated area.
The design requirements of the perforated shield wall are as follows:
- More than two rows of holes;
- Two rows of holes stagger each other;
- The hole spacing in the same row should be less than λ/20;
- Solder resistance is prohibited at the part where grounded PCB copper foil is crimped with shielding cavity wall.
kingford is a professional PCB design company engaged in electronic products layout layout design, mainly undertake multi-layer, high density PCB design and circuit board design proofing business. Proficient in the use of market mainstream PCB designsoftware, professional and efficient communication to ensure the progress of PCB design, to help you seize the market opportunity one step earlier!