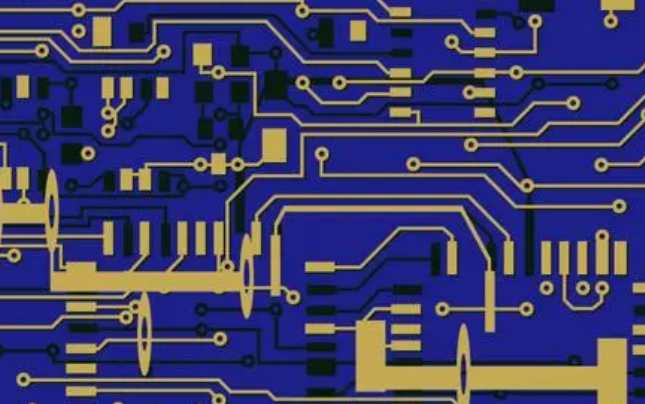
Sophisticated electronics and (assistive) systems serve us in aircraft, trains, trucks, and passenger vehicles, as well as in critical applications such as construction infrastructure, manufacturing equipment, and medical systems. High reliability (the ability of a product to meet all the requirements of a customer's environment over its desired life cycle) is becoming increasingly important. Big data and artificial intelligence are making humans more dependent on electronic systems, and will make reliability deficiencies even more deadly. At DesignCon 2020 recently, I had the opportunity to learn how ANSYS enables engineers to design highly reliable products.
Founded in 1970 near Pittsburgh, Pennsylvania, ANSYS now employs about 4,000 experts in the fields of finite element analysis, computational fluid dynamics, electronics, semiconductors, embedded software and design optimization. ANSYS is known for partnering with very demanding customers in space and aircraft applications. ANSYS then grew rapidly by acquiring other EDA suppliers. They acquired Ansoft Corp. in 2008 and Apache Design Solutions in 2011. This was followed in 2019 by ANSYS's acquisition of DfR Solutions, the developer of Sherlock, the industry's only automated design reliability analysis software.
ANSYS's comprehensive multi-physical field solution, combined with Sherlock's precise reliability analysis, will provide a complete designer-level suite that helps customers quickly and easily analyze electronic failures early in the design cycle, saving users time and money during development. The acquisition of DfR electronic reliability solutions reinforces their expertise in semiconductor packaging, PCBA simulation, and ability to characterize and generate libraries as well as analyze and test various electronic components.
Analyzing the reliability of prototype and/or preproduction units using test fault repair methods is expensive and time consuming, and results are not provided until late in the product lifecycle. ANSYS Sherlock finite element analysis (FEA) enables engineers to easily assess the reliability of hardware designs at the beginning of the design cycle. This also enables designers to weigh different architectures, geometrics and materials early on and across a wide range of conditions for optimal results.
In a packed conference room, Kelly Morgan, chief application engineer at ANSYS, presented three examples of failure mechanisms in which Sherlock could bring great value. Sherlock and ANSYS use physical failure principles to predict hardware reliability :1) low-K (Low dielectric constant) silicon wafers, 2) solder joint fatigue, and 3) micropore separation. There is much more to this information than is provided below.
Dielectric materials with low dielectric constant (k) reduce parasitic capacitance, improve circuit performance and reduce power consumption. However, its lower mechanical strength can sometimes lead to cracks in the dielectric during reflux or thermal cycling due to thermal-mechanical forces caused by differences in coefficient of thermal expansion (CTE). Acoustic examination can reveal these cracks. If the low-K material is found to be cracked in the final phase of product rollout, the cycle is redesigned. Sherlock and ANSYS, by contrast, allow IC designers to predict such failures at the beginning of a project and take immediate corrective action to prevent them from occurring.
Many integrated circuits traditionally use lead-free solder bumps as connections to other tube cores, packages, and even printed circuit boards (PCBS). Different thermal expansion coefficients and temperatures in adjacent layers will cause different expansion and contraction of the material. These thermal mechanical forces, vibration, mechanical impact, etc., will strain solder joints and may cause cracks on solder joints and interconnect surfaces. Recently, copper columns have become popular because of their smaller solder joint spacing. However, these interconnections are more rigid and, depending on the strain applied, may fail more quickly. The multi-physical capabilities of Sherlock and ANSYS Mechanical allow users to easily and accurately predict the reliability of such interconnections, as well as drive changes early in the design cycle if needed.
As the spacing in electronic devices becomes smaller and smaller, the use of microporous technology in PCBS is growing explosively. Stacking microholes up to three or four stories high has become common. However, if these designs do not use the right materials and geometry, the micropores may experience unexpected cracking and delamination.
Thermo-mechanical stresses, moisture, vibration, and other stresses can lead to separation of micropores and layering with copper trace lines at the top or bottom of the electroplated through-hole (PTH). Sherlock analyzes these problem areas, taking into account overstress conditions during reflux and/or operation, and can predict when fatigue will cause interconnection failures between through-or through-holes, through-holes, routing layers, and UBM contacts.