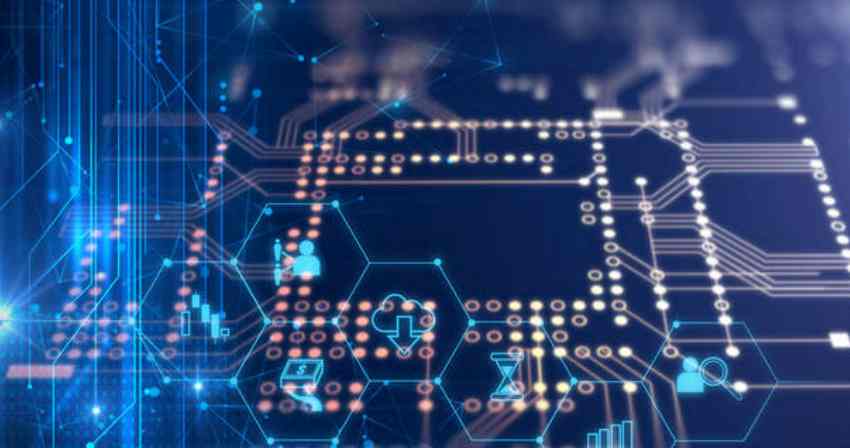
Many factors affect the quality of PCBA quality, including human, machine, material factors, technological factors, environmental factors, etc. The quality of pcba process is mainly affected by the following conditions.
1. Affected by human factors, including: lack of skills, work fatigue, lack of personnel allocation, lack of training, emotional work, unqualified vision, lack of spirit, lack of responsibility.
2. Factors affected by the machine include: irregular maintenance, insufficient air pressure, machine failure, mounting accuracy, poor level adjustment, component wear, insufficient gas supply, camera lighting, setting errors, etc.
3. Affected by material factors are: BOM correctness, component process quality, PCB process quality, warehousing and distribution management.
4. Affected by process factors are: steel mesh design problems, printing parameters problems, reflow/wave soldering and other welding problems, SMT/THT problems.
5. Affected by field factors include: operation standardization, process control, ESD management, temperature and humidity control, SS, etc.
Current location: Home page > Press center Industry News > Acceptance criteria for PCBA processed products
Acceptance criteria for PCBA processed products
With the development of society, more and more things are becoming more and more intelligent. The premise is to have more circuit chip to control these devices, and PCBA processing is one of the most important part. The quality of PCBA processing determines the life and quality of this product. The following describes how to accept PCBA processed products.
I. Test environment:
1, test environment: temperature: 25 + / - 3 ° C, humidity: 40-70% RH
2. Check the product within 1 meter of 40W fluorescent lamp (or equivalent light source), and the inspector should be 30 cm away from the inspector.
2. Quality assurance sampling standard: GB/T2828.1-2003 secondary inspection and sampling plan shall be implemented
AQL value: CR: 0 MAJ: 0.25 MIN: 0.65
Iii. Testing equipment:
BOM list, magnifying glass, probe, and patch location diagram
Iv. Acceptance standards
1. Damaged parts:
Any edge peeling less than 25% of the width or thickness of the element; At most 50% loss of metal coating at the top of the end (acceptable)
Any cracks or exposure to click gap; Cracks, nicks, or any damage to the body of a glass element. A groove in any resistance material. Any cracks or dents. (rejected)
2, patch components -- rectangular or square weldable end components of the side bias:
Side offset ≤ 50% of weldable end width of component or 50% of PAD width (acceptable)
Side bias greater than 50% of the weldable end width of the component or 50% of the PAD width (rejected)
3. Virtual welding:
The overlap between the weldable end of the element and the PAD is clearly visible. (acceptable)
Insufficient overlap between component end and PAD (rejected)
4, tin too much:
The maximum height of the solder joint may extend beyond the PAD or to the top of the weldable end cap metal coating, but not to the body (acceptable)
Solder has been extended to the top of the body. (rejected)
5. Foaming and layering
The area of foaming and delamination shall not exceed 25% of the plating through hole or inner line spacing (acceptable).
The bubbling delamination area exceeds 25% of the plating through hole or inner conductor spacing. The bubbling delamination area reduces the separation of the shell to the minimum electrical gap. (refused)
6. The white:
Chip components with exposed electrical materials shall be installed in such a way that the material is facing away from the printed surface; Only one component inverse white ≤0402 is allowed per Pcs board. (acceptable)
If there is exposed and accumulated electrical material, the patch element is attached to the mount material face towards the printed surface. (rejected)
7. Air welding
The solder joint between the component lead and PAD is moist and full, and the component lead is not warped. (acceptable)
Component leads are not coplanar, which prevents acceptable welding. (refused)
8. Cold welding
During reflow solder paste was fully stretched, the tin solder joints was fully wetting, smooth surface. (acceptable)
The solder paste on the tin ball is not fully reflow, the appearance of the tin is black and irregular, and the solder paste has not fully melted tin dust. (rejected)
9. Few parts: parts are not affixed to a certain patch position in BOM list that needs to be affixed. (Rejected) Multiple pieces: The BOM list requires a patch number that does not need to be affixed but has been affixed with components; The excess is in places where it shouldn't be. (rejected)