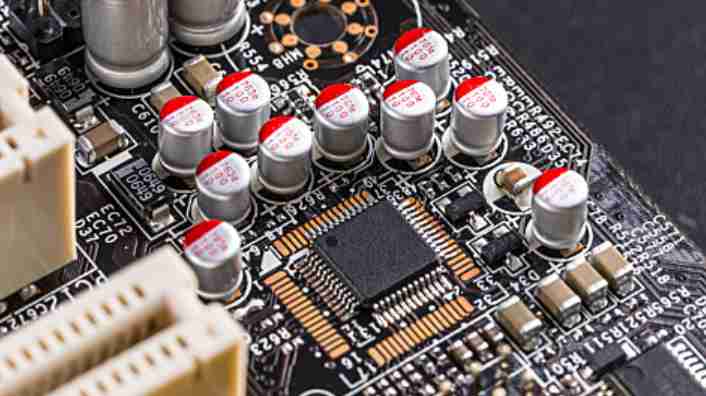
At first glance, PCBS look pretty much the same on the outside, regardless of their internal quality. It is beneath the surface that we see the differences that are critical to the durability and function of PCBS throughout their life.
Whether in the manufacturing and assembly process or in actual use, PCB to have reliable performance, this is very important. In addition to the associated costs, defects during assembly may be covered by the PCB
In the final product, failure may occur in the actual use process, leading to claims. Therefore, from this point of view, it is safe to say that the cost of a good quality PCB is negligible. In all market segments, especially those producing products in critical application areas, the consequences of such failures are dire.
These aspects should be kept in mind when comparing PCB prices. Although reliable, guaranteed and long-life products have higher initial costs, they are worth it in the long run. Let's take a look at Coke
The 14 most important characteristics of a reliable circuit board are:
1, 25 micron hole wall copper thickness
Benefits:
Enhanced reliability, including improved Z-axis expansion resistance.
Risks of not doing so:
Problems with hole blowing or degassing, electrical connectivity during assembly (inner separation, hole wall breakage), or possible failure under load conditions in actual use. IPCClass2 (most
The factory standard) requires 20% less copper plating.
2. No welding repair or line repair
Benefits:
Perfect circuit can ensure reliability and safety, no maintenance, no risk, the risk of not doing so if not properly repaired, it will cause circuit board break. Even if the repair is' properly ', there is a risk of failure under load conditions (vibration, etc.) which may occur in actual use.
3. Exceed the cleanliness requirements of IPC specifications
Benefits:
Improving PCB cleanliness improves reliability.
The risk of not doing so
Residue and solder buildup on the circuit board pose a risk to the solder shield. Ionic residue poses a risk of corrosion and contamination of the weld surface, which may lead to reliability problems (poor solder joints/electrical defects)
Barrier) and ultimately increase the probability of actual failure.
4, strictly control the service life of each kind of surface treatment
benefit
Solderability, reliability, and reduced risk of moisture intrusion
The risk of not doing so
Solderability problems can occur due to metallography changes in the surface treatment of older boards, and moisture intrusion can lead to delamination, inner and actual use during the assembly process and/or actual use
Hole wall separation (open circuit) and other problems.
5. Use internationally known substrates -- no "local" or unknown brands
benefit
Improve reliability and known performance
The risk of not doing so
Poor mechanical properties mean that the board will not perform as expected under assembled conditions. For example, high expansion properties can lead to delamination, circuit breaking and warping problems. A weakening of electrical characteristics can result in impedance
Energy difference.
6. Copper clad plate tolerance meets the requirements of IPC4101ClassB/L
benefit
Strict control of dielectric layer thickness can reduce the deviation of expected value of electrical performance.
The risk of not doing so
Electrical performance may not meet the specified requirements, the same batch of components in the output/performance will be very different.
7. Define solder resistance materials to ensure compliance with IPC-SM-840ClassT requirements
benefit
NCAB Group recognizes "excellent" inks for ink safety, ensuring that the solder resistance layer inks meet UL standards.
The risk of not doing so
Poor quality ink can lead to adhesion, flux resistance and hardness problems. All of these problems can cause the solder shield to detach from the circuit board and eventually lead to corrosion of the copper circuit. Poor insulation characteristics can be attributed to
Unexpected electrical connectivity/arc resulting in .
8. Define tolerances for shapes, holes and other mechanical features
benefit
Strict tolerance control can improve the dimensional quality of the product - improve fit, shape and function
The risk of not doing so
Problems during assembly, such as alignment/fit (pin pressing issues only become apparent when assembly is complete). In addition, loading the base can be problematic due to the increased size deviation.
9. NCAB specifies the solder shield thickness, although IPC does not specify it
benefit
Improved electrical insulation to reduce the risk of flaking or loss of adhesion and to increase resistance to mechanical impact wherever it occurs!
The risk of not doing so
Thin solder resistance layer can lead to adhesion, flux resistance and hardness problems. All of these problems can cause the solder shield to detach from the circuit board and eventually lead to corrosion of the copper circuit. Caused by thin solder resistance layer
Poor insulation characteristics can cause short circuit due to unexpected conduction/arc.
10. Appearance requirements and repair requirements are defined, although IPC does not
benefit
In the manufacturing process of careful care and careful casting safety.
The risk of not doing so
Multiple scrapes, minor injuries, repairs, and repairs - boards work but don't look good. In addition to the visible problems, what are the hidden risks, as well as the impact on assembly, and in
What are the risks in actual use?
11. Requirements for the depth of the plug hole
benefit
High quality plugs will reduce the risk of failure during assembly.
The risk of not doing so
The chemical residue in the gold settling process can be left in the hole where the plug hole is not sufficient, causing problems such as weldability. And the hole may also contain tin beads, in the assembly or actual use, tin beads may
It splashes out and shorts out.
12. PetersSD2955 specifies the brand and model of peelable blue glue
benefit
The designation of peelable blue glue avoids the use of "local" or cheap brands.
The risk of not doing so
Poor quality or cheap peelable glue may bubble, melt, crack, or set like concrete during assembly, making the peelable glue unpeeled/ineffective. 13. NCAB implements specific approval and placing procedures for each purchase order
13. NCAB implements specific approval and placing procedures for each purchase order
benefit
This procedure is performed to ensure that all specifications have been confirmed.
The risk of not doing so
If product specifications are not carefully confirmed, the resulting deviations may not be discovered until assembly or the final product, when it is too late.
14. Sleeve plate with scrap unit is not accepted
benefit
Not using partial assembly can help customers improve efficiency.
The risk of not doing so
Sheeting with defects requires special assembly procedures. If the scrap unit board (x-out) is not clearly marked, or it is not isolated from the sheeting, it is possible to assemble the known defect
Plate, thus wasting parts and time.