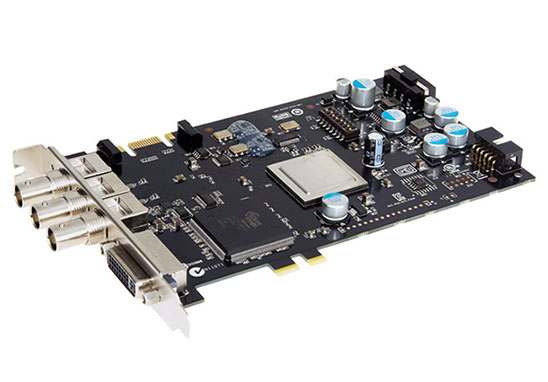
PCBA welding processing, usually PCB board has a lot of requirements, the board must meet the welding requirements. So, why does the welding process need to have so many requirements on the circuit board? It has been proved that in the process of PCBA welding, there will be a lot of special technology, the application of special technology will bring requirements to PCB board.
If PCB board problems, will increase the difficulty of PCBA welding process, ultimately may lead to welding defects, unqualified board, etc. Therefore, in order to ensure the smooth completion of the special process and facilitate the PCBA welding process, PCB board must meet the manufacturability requirements in dimensions, pad distance and other aspects.
Next, Shenzhen PCBA processing manufacturer -kingford will introduce the requirements of PCBA welding processing on PCB board.
1. PCB size
The width of the PCB (including board edges) must be greater than 50mm and less than 460mm, and the length of the PCB (including board edges) must be greater than 50mm. If the size is too small, it needs to be assembled.
2. PCB board edge width
Edge width > 5mm, plate spacing < 8mm, distance between plate and edge > 5mm.
3. PCB bending degree
Upward curvature: < 1.2mm, downward bending: < 0.5mm, PCB deformation: maximum deformation height ÷ diagonal length < 0.25.
4. PCB board Mark points
Mark shape: standard circle, square, triangle;
Mark size: 0.8~1.5mm;
Mark materials: gold plating, tin plating, copper and platinum;
Mark's surface requirements: smooth surface, no oxidation, no dirt;
Requirements around Mark: within 1mm of the surrounding area, there shall be no obstacles such as green oil with a color obviously different from that of the mark;
Mark position: More than 3mm away from the edge of the plate, and no marks such as holes and test points shall be found within 5mm.
5. PCB welding pad
There is no through hole in the pad of the SMD element. If there is a through-hole, the solder paste will flow into the hole, resulting in less tin in the device, or the tin flow to the other side, resulting in uneven surface, unable to print solder paste.
When designing and manufacturing PCB, it is necessary to know some knowledge of PCB welding process in order to make the product suitable for production. Understanding the requirements of the processing plant first can make the subsequent manufacturing process more smooth and avoid unnecessary trouble.
Above is the PCBA welding processing of PCB board requirements. In the production of PCB board, we should not slack off, only the production of high quality PCB board, PCB board can better accept other special technology, give PCB board life, inject the soul of function.
2. Advantages of hybrid packaging technology in PCBA processing
The reason we promote hybrid assembly services in PCBA processing today is because it started with Surface Mount Technology (SMT), a major phase trend following through-hole insertion (THT) in OEM processes. In addition to SMT and electroplating through-hole technology, we use many other operations such as implementing heat sinks, cabling and press fitting connectors, supporting PTH I/0 communication, etc. These are mixed advantages.
Layout stage plays an important role in hybrid assembly layout. In the layout phase, we gradually apply design for manufacturability (DFM) to hybrid model assembly. Our core considerations are as follows to obtain an accurate hybrid assembly location:
1. Reduce the total number of components in the product:
Reducing product components requires less processing time, development time, equipment, smt processing difficulty, service inspection, testing, etc.
2. Modular layout:
Modular layouts increase product versatility, simplify the redesign process, and help minimize product changes.
3. We use multifunctional layout parts:
In addition to their primary function, some layout components have self-alignment capabilities, which help to efficiently lay out modules for mixed part placement.
4. Easy to manufacture layout:
To facilitate the PCB hybrid assembly process, the best combination of layout and materials is selected. With ease of manufacture, the problem of excessive tolerance and surface finish requirements will be minimized. This is the main advantage of the whole mixing process.
To this end, kingford uses a variety of DFM review processes. In addition to component procurement and destructive testing services, we provide advanced PCB board manufacturing services, high and low volume smt proofing, hybrid assembly processes and more to our global customers.
kingford PCBA processing advantage
1. Highly professional: The company focuses on processing samples and small and medium-sized batches, and promises to deliver the materials within 3-5 working days after confirmation.
2. Professional equipment: The company's equipment is tailored for sample and small and medium-sized batch production of advanced equipment, can stick 0201, BGA spacing 0.3MM, QFN, CSP, CON and other components.
3. Professional technology: 100% of technical backbone workers have more than 5 years of work experience, 85% of front-line operators have more than 3 years of work experience.
4. The company implements the 5S and 6σ concepts in daily operation, so as to ensure that the shipment is checked at least 7 times. If the quantity reaches 100PCS, our company promises to pass AOI optical inspection.
5. The company promises that the straight through rate of welding is more than 99%. If customers find welding defects, the company promises to repair them free of charge.