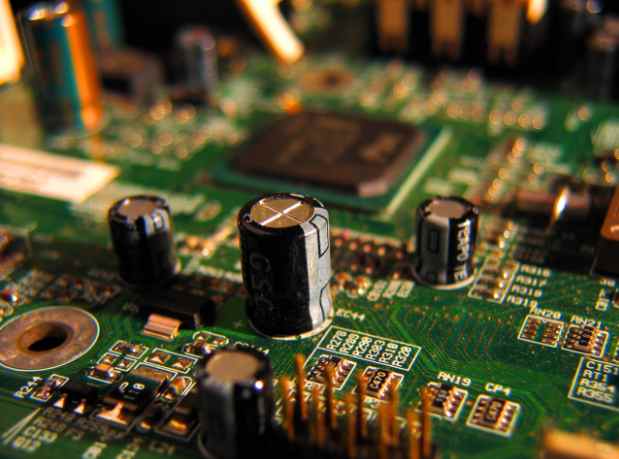
After SMT processing is completed, packaging shall be inspected to ensure that PCBA products delivered to customers are working normally and reliably. Next, Shenzhen PCBA processing manufacturer kingford will introduce the matters for attention in packaging inspection after SMT processing.
Precautions for packaging inspection after SMT processing
1. SMT factory shall assemble and deliver finished products after SMT processing. PCBA manufacturer shall sort out inspection and test data and data, issue qualification certificate, and prepare test plates and packaging materials for testing after passing the inspection. Delivery shall include accepted printed boards, certificates of conformity, necessary (or as stipulated in the contract) test data and attached test plates (for Grade 3 product multilayers shall include at least circuit on-off test data, metallographic microcut photos of plated holes).
2. The attached test board can add the appropriate test graphics to the outside of the frame of the required printed board (near the outside of the edge line) as a part of the board (assembly board), and the required printed board processing at the same time, to the final smt processing shape is separated, to represent the finished circuit board for doing some destructive tests such as voltage resistance, thermal stress, analog rework, micro-cutting. The attached test plate should generally be marked with a lot number; When the board is assembled in SMT form, the attached test board shall be marked with a printed board so that it can be traced from the attached board to the finished board it represents. For Grade 3 product printed boards, attached test boards must be provided. For Grade 1 and grade 2 printed boards, whether attached test boards should be provided shall be decided by the user or in accordance with the contract.
3. Packing, storage and transportation
(1) Packing
SMT plant packaging is to ensure qualified printed board products, can withstand transportation, storage environment, before use without damage and degradation of quality. After cooling to room temperature and packing, the PCB board that has passed the inspection shall be cleaned, dried and dehumidified according to the regulations. Then, the PCB board shall be packed in polyethylene plastic bag or laminated plastic bag composed of polyethylene/polyamide and polyester/polyethylene with vacuum sealing. The multiple layers of multiple packages shall be lined with neutral wrapping paper. It is usually packed in laminated plastic vacuum-absorbing packaging. If the storage environment is harsh and the storage time is long, when the specified storage conditions are exceeded, the plastic aluminum foil laminated bag made of aluminum foil and polyethylene or polyester film can be used for vacuum packaging as agreed by both parties. When long distance transportation is required, the finished multilayer board shall be packed into the packing box, the outer ring of the box shall be sealed, the box shall be lined with moisture-proof paper, and the desiccant shall be put in. Each batch of qualified products shall be accompanied by the product qualification certificate. If the products are packed in boxes (or other packing forms), the packing list shall be attached, including the product name, finished product model, specification, batch, quantity, production date, packaging date, production unit, etc.
(2) In the process of storage and transportation, moisture and long-term sun exposure should be prevented, and contact with strong alkali, strong acid gas and mechanical damage should be prevented. PCB boards should be stored in a clean container or box with a temperature of 10 ~ 35℃ and a relative humidity of no more than 75%. The surrounding environment should not be acidic and alkaline.
2. Classification introduction of PCBA inspection items
What are the categories of PCBA inspection items? According to IPC and Chinese military standards, the inspection items are divided into four categories: material inspection, process inspection, identification inspection and quality consistency inspection.
PCBA processing plant
1. Material inspection
In patch electronics factory, material inspection is an important part of quality control in the production process of PCBA board manufacturer, and also a part of quality assurance for users, which proves that the materials used in PCBA board are qualified after reinspection. When the user needs to check the materials of the finished PCBA board, the material inspection can be used as proof that the quality of the materials conforms to the design document or the order contract. The material inspection shall consist of the original product certificate of the SMT factory and the certificate of conformity based on the identification data obtained by the manufacturer of the PCBA board through counting sampling as stipulated. Key materials applicable to printed board production must be reinspected, including substrates, semi-cured sheets and other process materials. The content of the reinspection should be targeted at the main parameters which have an impact on the product. For process materials, it is usually necessary to check the qualification certificate of materials and conduct necessary process tests to determine the quality of materials. It is not necessary to test or inspect all properties of materials, because it is impossible and unnecessary for any professional SMT manufacturing factory to have test conditions and capabilities for all materials.
2. Process inspection
SMT patch processing enterprise process inspection is the quality inspection in the production process of PCBA board, it is the basis to ensure the quality of the final product, but also an important part of the quality assurance system. SMT patch OEM shall set up appropriate inspection points according to its own production quality stability, process characteristics and product quality grade requirements. It is most advantageous to implement the inspection method combining self-inspection, mutual inspection and special inspection. It is difficult to achieve the three-level inspection system in mass production, but at least self-inspection and special inspection should be carried out. Inspection points should be set at least in the photographic plate, hole metalization (coating hole integrity), inner and outer layer of conductive pattern etching (check wire width and spacing level graphic defects), before coating solder resistance film (check cleanliness), after drilling and contour machining, circuit opening and closing and product packaging, and there should be inspection records. In the production process should also be equipment, key solution and plating solution for regular or irregular testing, automation equipment should be at any time to detect the running state of the equipment.
3. Identification and inspection
Qualification inspection is used to prove that the PCBA board manufacturer has the ability to produce the products specified in the standard. It is also the user's choice of qualified PCB suppliers, and the certification of their production capacity and the identification of new products. The inspection shall be carried out in the inspection lot of PCBA boards manufactured using the equipment and processes used in normal production, and the qualification inspection shall meet all requirements of the specified product grade. Qualification tests may be conducted using standard test samples, finished plates, trial production samples or past performance data assessed as equivalent by both parties (generally Group B test items with high test costs). The test sample size shall be in accordance with relevant regulations or national standard GB2828 or agreed by both parties.
4. SMT factory quality consistency inspection
Quality conformance inspection is carried out on the finished product PCBA board or quality conformance attached board to ensure the quality of the delivered product. When using the attached board, it shall be made according to the pattern and position on the assembled board as specified in the standard. For each piece of quality consistent attached board and its corresponding finished board, there shall be a traceability mark certificated to be on the same piece of fabricated board. The quality conformance inspection shall include Group A (batch by batch) and Group B (periodic).
(1) SMT patch proofing Group A inspection shall conduct batch by batch inspection, and shall conduct Group A inspection for all products delivered to users; For different levels of products, the items and frequency of inspection are different.
Products that have passed the inspection of Group A shall not be delayed before the completion of the inspection of Group B. Since the inspection of Group B is carried out periodically, it should be delivered as long as the inspection of Group A is qualified.
(2) Group B inspection Group B inspection is conducted in accordance with the specified period, and the items and frequency of inspection for different levels of products are different.
For the above inspection items, if the material or process changes, the SMT electronic patch manufacturer should carry out experiments at any time to determine the influence of the material and process changes on the quality of PCBA board. If group B fails to pass the inspection, for Level 3 product board, the supplier shall notify the user unit that has delivered the products during the inspection period of Group B to stop receiving the products until the supplier of PCBA board takes corrective measures, and conduct the B inspection again until the corrective measures are proved to be effective. If the product fails to pass the repeated inspection, the supplier shall inform the user of the unqualified information and corrective measures to be taken. The frequency and period of inspection shall be stipulated in the relevant standard or contract. The sampling method and test method of inspection shall refer to relevant standards.
There are four reasons for choosing Shenzhen kingford for SMT processing
1. Strength guarantee
▪SMT workshop: We have imported SMT machines and several sets of optical inspection equipment, with a daily output of 4 million. Each process is equipped with QC personnel, who can keep an eye on product quality.
▪DIP production line: We have two wave-soldering machines, among which there are more than 10 old employees who have worked for more than three years. The skilled workers can weld all kinds of plug-in materials.
2. Quality assurance, cost-effective
▪ High-end equipment can stick precision shaped parts, BGA, QFN, 0201 materials. Can also template patch, loose material hand.
▪ Sample and size batch can be produced, proofing from 800 yuan, batch 0.008 yuan/point, no start-up fee.
3. Rich experience in SMT and welding of electronic products, stable delivery
▪ Accumulated SMT SMT processing services for thousands of electronic enterprises, involving many kinds of automotive equipment and industrial control motherboard. The products are often exported to Europe and the United States, and the quality can be affirmed by new and old customers.
▪ On time delivery, normal 3-5 days after complete materials, small batch can also be expedited on the same day shipment.
4. Strong maintenance ability and perfect after-sales service
▪ Experienced maintenance engineers can repair all kinds of patch welding caused by bad products, to ensure the connection rate of each piece of circuit board.
▪ 24-hour customer service staff at any time response, the fastest speed to solve your order problems.