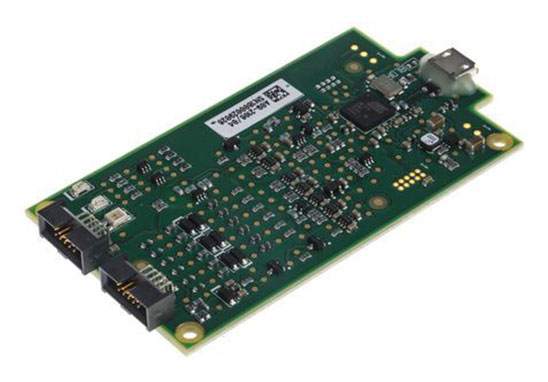
SMT patch machining has an important index for machining quality evaluation, that is straight rate. In patch processing. SMT pass through rate refers to the proportion of one-time qualification from production to the last process. This parameter can directly reflect the processing capacity of SMT processing plant and directly reflect the quality control of SMT processing plant. The higher the pass-through rate, the higher the capacity.
In order to ensure the pass-through rate of SMT patch processing, we hear most about improving manufacturing design (DFM), but the following five process optimization methods are needed to truly improve the pass-through rate of smt patch processing:
1. Improve pcb circuit board steel mesh design;
2. Select the appropriate type of solder paste;
3. Improve the operation method of printing process;
4. Increase the temperature curve of indoor/reflow welding;
5. Select tooling and improve the process method.
For the defects of each process, our company gives the following processing ideas, I hope to help you.
The main reason for the bridge: welding paste
Solution: (1) reduce the amount of solder paste; (2) "large welding plate narrow window" design, guide solder spreading, especially suitable for steel mesh window can not be reduced
The main reason for opening welding: the gap between the bottom of the pin and the pad is large
Solution: (1) Increase the thickness of steel mesh; (2) Expand the size of the pad
The main reason of mechanical fracture of BGA solder joint is operating stress
Solutions: (1) Use tooling to reduce the operational stress of human tooling screws, splice plates and crimping; (2) Reinforce the components (solder joints).
The main reason for the production of tin beads: the solder paste flows to the non-welding surface, mainly around the bottom surface contact, such as chip components, QFN, etc.
Solution: (1) internal steel mesh window, to avoid melting solder flow to the solder joint outside; (2) Cancel the welding resistance around the pad and reserve space for excess solder.
2.PCBA welding requirements for PCB board
In the process of PCBA welding, there are usually many requirements for PCBA plate, which must be met before welding.
Then why welding processing needs to have so many requirements for PCBA board? PCBA will go through a lot of special processes in the processing process, the application of special processes will immediately bring a lot of special process PCB board requirements, if the PCB board problems will increase the difficulty of PCBA welding process may eventually lead to welding defects, unqualified boards, etc.
Therefore, in order to ensure the smooth completion of the special process, but also to facilitate the PCBA welding processing, PCB board size, pad distance and other aspects should meet the manufacturability requirements, then Shenzhen PCBA processing plant - kingford to take you to see the PCBA processing requirements for PCB board.
PCBA processing requirements for PCB board
1.PCB size
PCB width (including board edge) should be greater than equal 500mm, less than 460mm, PCB length (including board edge) should be greater than equal 500mm. The size is too small. It needs to be made into plates.
2.PCB board edge width
Edge width: > 5mm, plate spacing: 8mm, welding pad and plate distance: > 5mm
3.PCB bending degree
Edge width: > 5mm, plate spacing: 8mm, welding pad and plate distance: > 5mm
4.PCB board Mark points
Mark shape: standard circle, square, triangle;
The size of Mark; 0.8~1.5mm;
Mark material: gold plating, tin plating, copper platinum;
Mark surface requirements: smooth surface, smooth, no oxidation, no dirt;
Requirements around Mark: There should be no green or other obstacles in the surrounding 1mm.
Mark position: More than 3mm away from the edge of the plate, and no similar Mark holes or test points can be found in the surrounding 5mm.
5.PCB welding pad
There is no through hole in the pad of the patch assembly. If there is a through hole, the tin paste will flow into the hole, resulting in less tin in the device, or tin flow to the other side, resulting in uneven surface, tin paste can not be printed.
In PCB design and production, it is necessary to understand some knowledge of PCBA welding process to make the product suitable for production. First understand the requirements of PCBA processing plant, can make the subsequent manufacturing process more smooth, avoid unnecessary trouble.
This is the specific requirements of PCBA welding processing for PCB board, not slack in the production of PCB board, the production of high-quality compliance of PCB board can make the board better to accept other special processes, and give PCB board life, inject the soul function.
About kingford
Shenzhen kingford Co., Ltd. specializes in providing integrated PCBA electronic manufacturing services, including upstream electronic components procurement to PCB production and processing, SMT patches, DIP plug-ins, PCBA testing, finished product assembly and other one-stop services.
The company gives full play to its competitive advantages in scale procurement and quality control, and has signed long-term cooperation agreements with many electronic component manufacturers at home and abroad and around the world to ensure the quality and stable supply of raw materials, and transfer the benefits to customers.
We provide PCBA processing services, starting from PCB circuit board production, our own PCB manufacturers (obtained the very strict TS16949 certification of the automotive industry), pay attention to the quality of the circuit board and PCBA quality control system.
With decades of experience in purchasing electronic components, we maintain long-term cooperation with large brands to ensure the original packaging and procurement channels of components. In the process of component packaging, the selection of Qianzhu and Letai solder paste, to ensure the reliability of welding, with automatic printing press, Panasonic high-speed SMT machine, up and down eight temperature zone reflow welding, AOI automatic optical detector, can effectively ensure the reliability and quality of electronic packaging process.
In addition, perfect IPC, IPQC, OQA and other management processes, clear job responsibilities, strict implementation of IPC electronic assembly acceptance standards. For PCBA testing, we have professional engineers to perform 100% batch testing using a variety of test stands, including access, noise, amplitude, signal, temperature, humidity, drop or to perform customer detailed test plans. All efforts are aimed at becoming a refined PCBA processing factory.