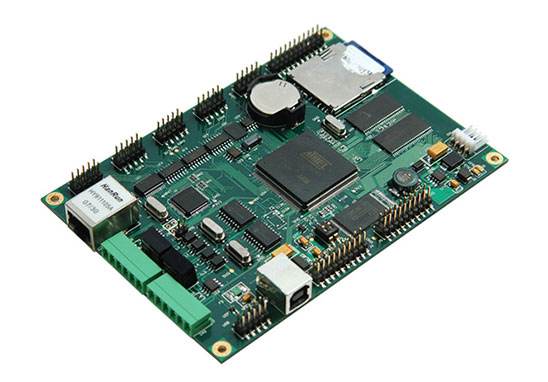
In SMT OEM, there is a bad processing phenomenon called welding pores, which is often called bubbles. Welding pores is a bad processing phenomenon that must be solved in the SMT processing process. Only if there is no bad phenomenon can we provide the best SMT patch processing service to customers. Next, kingford, Shenzhen SMT processing manufacturer, will share with you how to avoid the appearance of pores in patch welding.
Five methods to solve the patch welding hole
1. Bake
Baking of circuit boards and patch components exposed to air for a long time will remove the moisture that may affect the processing.
2. Tin paste
If the solder paste contains moisture, it is easy to produce pores and tin beads in the SMT patch processing. For the solder paste, we need to choose high quality solder paste, and then for the solder paste back temperature, stirring need to be strictly executed in accordance with the requirements of electronic processing production, solder paste exposure to the air time as short as possible, after printing solder paste, need to timely reflow welding.
3. Humidity
Planned to monitor the workshop humidity, control between 40-60%.
4, furnace temperature curve
Twice a day for furnace temperature test, optimize the furnace temperature curve, heating rate can not be too fast. The temperature of the preheating zone should meet the requirements, not too low, so that the flux can be fully volatilized, and the speed of the furnace can not be too fast.
5. Flux
In the wave soldering, the flux spraying amount can not be too much, spraying reasonable.
2. Precautions for SMT proofing and processing IC patches
IC is the English abbreviation of integrated circuit IntegratedCircuit, industry usually according to the form of IC packaging to divide the type of IC, traditional IC has SOP, SOJ, QFP, PLCC, etc., relatively new IC has BGA, CSP, FLIPCHIP, etc. They vary in shape due to the number of pins (part pins) and the spacing between pins.
The packaging form of chip components is one of the packaging forms of semiconductor devices, SMT processing involves a wide variety of parts, a variety of styles, many have become a common standard in the industry, which is mainly some chip capacitance resistance; Many are still changing, especially for IC parts, and the variety of packaging forms is dizzying.
SMT proofing processing IC patch should pay attention to matters
It is difficult to splice IC in SMT manual paste processing and production. After all, IC is usually an IC with a large number of stitches, which requires our SMT patch processing staff to treat it carefully and patiently and operate in strict accordance with processing requirements in order to obtain products with the same quality as machine paste. Chip hand welding has many points worth noting. For example, due to the high internal integration, it is easy to be damaged by overheating. Generally, the temperature of SMT proof machine can not exceed 200℃.
SMT proofing processing IC patch common notes
1. The welding time should be as short as possible, generally no more than 3s.
2. The electric iron used is a constant temperature of 230 degrees.
3. Anti-static treatment should be done on the SMT proof table.
4. Choose a soldering iron head with a narrow tip, which will not touch the adjacent end points when welding.
5. During SMT patch processing, do not take out the pre-set short circuit before CMOS circuit welding.
6. The plug of the electroplating circuit cannot be scraped off with a knife. Just scrub it with alcohol or wipe it clean with a drawing eraser.
kingford provides professional PCBA OEM services, including upstream electronic components procurement to PCB production and processing, SMT patches, DIP plug-ins, PCBA testing, finished product assembly and other one-stop services.
The company gives full play to its competitive advantages in scale procurement and quality control, and has signed long-term cooperation agreements with many electronic component manufacturers at home and abroad and around the world to ensure the quality and stable supply of raw materials, and transfer the benefits to customers.