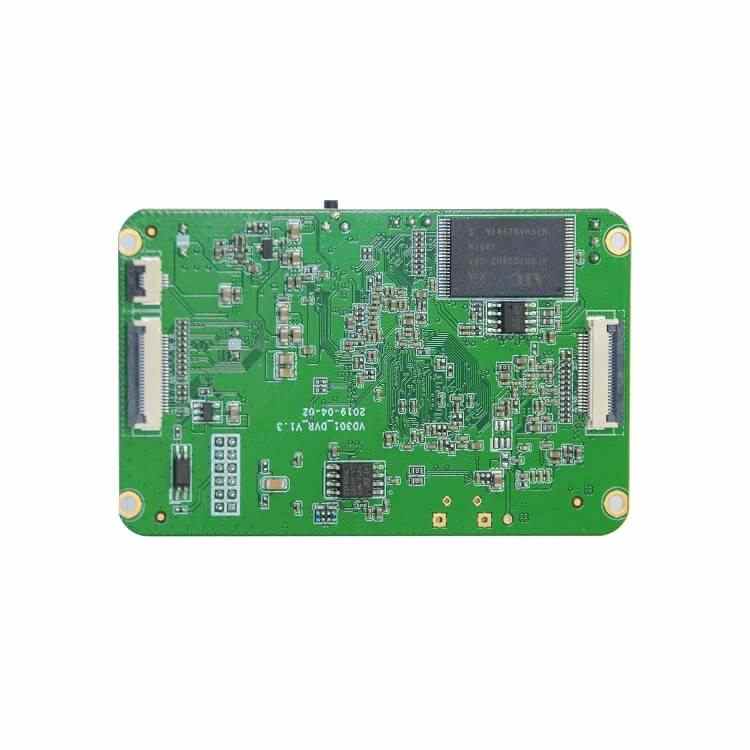
What are the characteristics of AOI introduced by SMT processing plant?
(1) High-speed detection system has nothing to do with PCB mounting density.
(2) Fast and convenient programming system.
(3) Rich special multifunctional detection algorithms and binary or gray level optical imaging processing technology are used for detection.
(4) The detection window can be automatically corrected according to the instantaneous change of the location of the components to be detected, so as to achieve high-precision detection.
(5) Check the detection points by ink marking directly on the PCB or by graphical error representation on the operating display.
AOI can be placed after printing, before welding and after welding.
(1) AOI is placed after printing. The printing quality of welding paste can be checked. It can detect whether the amount of solder paste is appropriate, whether the position of the solder paste figure is offset, and whether there is adhesion between the solder paste figure.
(2) AOI is placed after the patch and before welding. The quality of the patch can be tested. It can detect component misplacement, component shift, component reverse placement (such as resistance flip), component side standing, component loss, polarity error and patch pressure caused by adhesion between solder paste graphics, etc.
(3) AOI is placed after reflow welding. Welding quality inspection can be done. It can detect the welding defects such as misplacement of components, displacement of components, misplacement of components (such as resistance turning over), loss of components, polarity errors, solder joint moisture, too much solder, too little solder, leakage welding, virtual welding, bridge connection, welding ball (welding ball between pins), component cocking (tablet) and so on.
2. Principle and application field of X-RAY detection equipment
Every industry will have some capable equipment helpers, today we talk about the rapid development of the electronic industry in the capable "x-ray detection equipment", I believe that in this industry work friends have a certain understanding. This article summarizes the x-ray detection equipment principle and application field, so that you can quickly master after reading.
I. Principle of x-ray detection equipment
1. First of all, X-RAY equipment mainly uses the penetration effect of X-ray rays. X-ray rays have a very short wavelength and a very large energy.
2. What x-ray equipment can detect is the relationship between the penetration force of X-ray rays and the density of substances. Substances with different densities can be distinguished by the use of differential absorption. Therefore, if the detected item is broken, has different thickness, and changes shape, the absorption of X-ray rays is different, and the images produced are different, so the black and white images can be produced.
3, can be used for IGBT semiconductor detection, BGA chip detection, LED light strip detection, PCB bare board detection, lithium battery detection, aluminum castings non-destructive detection.
4. In simple terms, this is done by using a non-destructive micro-focus x-ray device to output high quality fluoroscopic images and then convert the signals received by the flat-panel detector. All the functions of the operation software only need a mouse to complete, very easy to use. Standard high-performance x-ray tubes can detect defects up to 5 microns, and some X-ray devices can detect defects up to 2.5 microns. The system magnifies up to 1,000 times, and objects can move and tilt. The x-ray device can perform manual or automatic detection and automatically generate detection data reports.
2. Application fields of X-RAY detection equipment
1. Industrial X-RAY testing equipment is widely used, commonly used in lithium battery testing and other battery industry, circuit board industry, semiconductor packaging, automotive industry, circuit board assembly (PCBA) industry, to observe and measure the position and shape of the internal objects after packaging, find problems, confirm whether the product is qualified, and observe the internal condition.
2, specific application scope: mainly used for SMT, LED, BGA, CSP flip chip detection, semiconductor, packaging components, lithium industry, electronic components, auto parts, photovoltaic industry, aluminum die casting, molded plastics, ceramic products and other special industries detection.