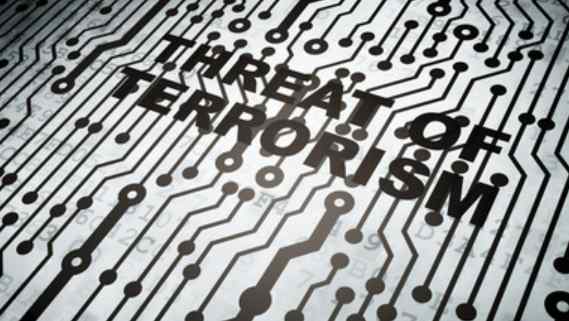
(1) The printed circuit is not allowed to have a cross circuit, for the possible cross lines, you can use "drill", "wind" two ways to solve. That is, let a lead from other resistance, capacitance, the gap at the foot of the audion "drill" in the past, or from the possible cross of a lead end "wound" in the past, in special cases how to circuit is very complex, in order to simplify the design also allows the use of wire straddle, to solve the problem of cross circuit.
(2) Resistance, diode, tubular capacitor and other components have "vertical", "horizontal" two ways of installation. Vertical refers to the component body perpendicular to the circuit board installation, welding, its advantage is to save space, horizontal refers to the component body parallel and close to the circuit board installation, welding, its advantage is that the mechanical strength of the component installation is better. These two different mounting components, the component hole spacing on the printed circuit board is not the same.
(3) The ground point of the same level circuit should be as close as possible, and the power filter capacitor of this level circuit should also be connected to the ground point of the level. In particular, the base of the transistor, the emitter of the ground point can not be too far away, otherwise because the copper foil between the two ground points is too long will cause interference and self-excitation, the use of such a "point grounding method" circuit, the work is more stable, not easy to self-excitation.
(4) the total ground wire must be strictly in accordance with the high frequency - medium frequency - low frequency one level according to the order of weak current to strong current principle, must not randomly turn over and over, between the level would rather wiring long point, also want to comply with this provision. In particular, frequency conversion head, regeneration head, frequency modulation head grounding wire arrangement requirements are more strict, if there is improper will produce self-excitation so that it can not work.
In order to ensure a good shielding effect, a large area enclosed ground wire is often used in the high frequency circuit of FM.
(5) The strong current lead (public ground wire, power amplifier power lead, etc.) should be as wide as possible to reduce the wiring resistance and voltage drop, can reduce the self-excitation caused by parasitic coupling.
(6) The high impedance of the line as short as possible, low impedance of the line can be longer, because the high impedance of the line is easy to whistle and absorb signals, causing circuit instability. The power line, ground wire, base wiring and emitter lead of non-feedback components are all low-impedance wiring. The ground wire of the base wiring of emitter follower and the ground wire of the two sound channels of the radio and recording machine must be separated into one road and then combined until the end of the effect. If the two ground wires are connected, crosstalk is easily generated and the separation degree is reduced.
(7) Where the multi-pin components (such as SOIC, QFP, etc.), the short joint between the pin pad is not allowed to go through, should be from the pad and lead to the interconnect after the short connection (if the solder mask can be excluded) in order to avoid displacement or be mistaken for bridge after welding. In addition, should also try to avoid crossing the interconnect between the pad (especially the fine spacing of the pin device); Where the interconnect between adjacent pads is crossed, it must be shielded by solder resistance film.
(8) For the multi-pin components, especially those with a spacing of 0.65mm or less, the bare copper reference mark should be added on or near the solder pad graph (for example, two symmetrical optical positioning marks of bare copper should be added on the diagonal of the solder pad graph) for precise placement and used for optical calibration.
(9) When the wave crest welding process is used, the through hole on the pin pad should generally be 0.05 ~ 0.3mm larger than the pin diameter, and the diameter of the pad should not be greater than 3 times the aperture. In addition, for the IC, QFP device pad graphics, when necessary, can be added to the fusion welding material drag effect of technology assistant pad, in order to avoid or reduce the occurrence of bridge phenomenon.
(10) The pad used for welding surface mounted components (i.e., the welding point) shall not be used as a test point; Special test pad must be designed to avoid damage to components. To ensure the welding test and production debugging of normal.
(11) All pads used for testing shall, whenever possible, be arranged on the same side of the PCB. This is not only easy to detect, more importantly, greatly reduce the cost of detection (automatic detection is even more so). In addition, the test pad shall not only be coated with tin-lead alloy, but also its size, spacing and layout shall match the relevant requirements of the test equipment used.
(12) If the size given by the components is the maximum and minimum value, the average size can be used as the reference of pad design.
(13) In the design of computer, in order to ensure that the designed graphics can reach the required accuracy, the size of the grid unit must be matched; For the convenience of drawing, all the figures should fall on the grid points as far as possible. For multi-pin and fine-spaced components (such as QFP), when drawing the center spacing of its pad, not only must its mesh unit size be 0.0254mm (that is, 1mil), but also the origin of its drawn coordinates should always be set at its first pin. In short, for multi-pin fine-spaced components, the overall cumulative error must be controlled within ±0.0127mm (0.5mil) during pad design.
(14) All kinds of pads designed shall be used in production together with their carrier PCB after passing test welding and testing. This is especially true for mass production.