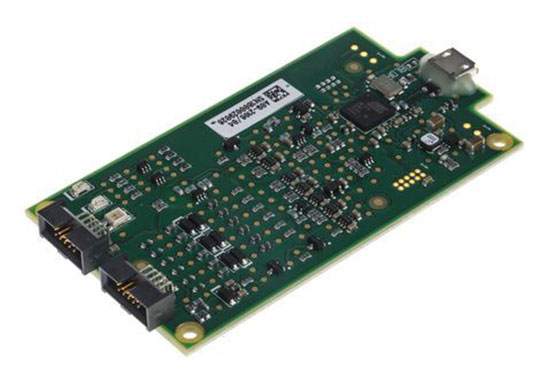
Soft and hard combined board, is Flexible circuit board and hard circuit board, after pressing and other processes, according to the relevant process requirements combined together, formed with FPC characteristics and PCB characteristics of the circuit board. There are many differences between soft board and hard board in PCB design. Next, Shenzhen PCB design company -kingford will introduce the key points of PCB design.
Soft and hard PCB design points
1. Circuit design requirements for flexible area:
1.1 The line should avoid sudden expansion or contraction, and use tear shape between thick and thin lines;
1.2 If electrical requirements are met, the maximum value of the pad should be adopted. The connection between the pad and the conductor should adopt a smooth transition line, avoiding right angles. The independent pad should be equipped with the toe, which can strengthen the supporting effect.
2. Dimensional stability: Add copper design as much as possible, and design as many solid copper foils as possible in the scrap area.
3. Design of covering film window
3.1 Add manual alignment holes to improve alignment accuracy
3.2 Window design Considering the scope of glue flow, usually the window opening is larger than the original design, the specific size of the design standard is provided by ME
3.3 Special mold design can be adopted for small and dense scutches: rotary punching, jump punching, etc
4. Design of rigid torsion transition zone
4.1 Smooth transition of the line. The direction of the line should be perpendicular to the direction of bending.
4.2 The wire shall be evenly distributed throughout the bending area.
4.3 The wire width shall be maximized throughout the bending area.
4.4 PTH design shall not be adopted in the transition area as far as possible.
4.5 Design of Coverlay and NoflqwPP for rigid flexible transition zone
5. Flexible area design required by air-gap
5.1 There should be no through hole in the part to be bent;
5.2 Add protection copper wire to the most sides of the line. If space is insufficient, add protection copper wire to the inner R Angle of the bent part.
5.3 The connecting part of the line shall be designed as an arc.
5.4 The larger the bent area, the better, in the absence of interference with assembly.
6. Others
Do not share the tool holes on the soft board, such as the punch hole, ET hole, and SMT positioning hole.
Notes for PCB design of soft and hard combined board
1, soft and hard combined board large area grid interval distance is too small, in the process of printed circuit board production and manufacturing, the figure transfer process after the shadow, it will be very easy to produce many broken film attached to the board, resulting in broken lines.
2, soft and hard combined plate of the single-side weld disk aperture setting is not perfect, in the process of drilling, there will be problems.
3. The electric formation of the soft and hard combined plate is the problem of welding plate and connection.
4. In the design process of the soft and hard combined plate, the overlap of the pad is a problem, because after the hole overlap, the drill will be broken due to multiple drilling in a place in the drilling process, resulting in hole damage.
2. What are the characteristics of high reliability PCB?
PCB as the core substrate of electronic products, its quality and reliability directly affect the quality and reliability of electronic products, so high reliability PCB has become the basic requirements of many electronic products. Next, Shenzhen PCB Board factory -kingford will introduce the important characteristics of high reliability PCB.
High reliability PCB important characteristics
1, achieve 25μm hole wall copper thickness can enhance reliability, including improved Z-axis expansion resistance;
2, perfect circuit can ensure reliability and safety, high reliability PCB is generally no welding repair or repair repair, so that it can well avoid circuit board break and other risks.
3. Residue and solder accumulation on the circuit board will bring risks to the solderproof layer. Ionic residue will lead to corrosion and pollution risks on the welding surface, which may lead to reliability problems such as bad solder joints/electrical failures, and ultimately increase the probability of actual failures.
4, the surface treatment of the old circuit board will change metallofacies, there may be solder problems, and moisture intrusion may lead to stratification, inner layer and hole wall separation (open circuit) in the assembly process or actual use, so the high reliability of PCB will strictly control the service life of each kind of surface treatment.
5. Poor mechanical properties mean that the circuit board cannot perform the expected performance under the assembled conditions. For example, high expansion performance will lead to delamination, circuit breaking and warping problems. Weakened electrical characteristics can lead to problems such as poor impedance performance. Therefore, high reliability PCB factories will use internationally renowned substrates, such as Shengyi, Kingboard, Liumao and other well-known brands. KINJI PCB factory is using these substrates to ensure high reliability of customers' PCB products.
6. Because the electrical performance may not meet the specified requirements, the output/performance of the same batch of components will be greatly different. The PCB factory with high reliability will strictly control the dielectric layer thickness to reduce the deviation of the expected value of electrical performance.
7, inferior ink can lead to adhesion, flux resistance and hardness problems. All of these problems can cause the solder shield to detach from the circuit board and eventually lead to corrosion of the copper circuit. Poor insulation characteristics can cause short circuits due to unexpected electrical connectivity/arcing. High reliability PCB factories will strictly define solder resistance materials to ensure compliance with IPC-SM-840ClassT requirements.
8, high reliability PCB will strictly define the shape, hole and other mechanical characteristics of tolerance, very good to improve the product size quality - improve the fit, shape and function.
9, thin solder resistance layer can lead to adhesion, flux resistance and hardness problems, high reliability PCB factory NCAB specified solder resistance layer thickness, although IPC has no relevant regulations.
10, high reliability PCB factory defines the appearance requirements and repair requirements, in the manufacturing process of careful care and carefully cast safety, avoid a variety of scratches, small damage, repair and repair.
11, the plug hole depth has a high requirement, the use of high-quality plug holes to reduce the risk of failure in the assembly process.
kingford PCB board making ability
Energy production from 2 layers to 14 layers, 14-22 layers can be proofing production.
Minimum line width/spacing: 3mil/3milBGA Spacing :0.20MM
Minimum aperture: 0.1mm Size :610mmX1200mm
Ink: Tamura, Taiyo, Fudoken;
FR4: Shengyi, Kingboard, Harbour, Hongren, Guoji, Hezheng, Nanya,
(Shengyi S1130/S1141/S1170),Tg130℃/ Tg170℃ T g180℃ and other high TG plates)
High frequency plate: Rogers, Taconic, ARLLON;
Surface process: tin spray, lead-free tin spray, gold plating, full plate gold plating, plug gold plating, full plate thick gold, chemical tin (silver), anti-oxidation (OSP) blue glue, carbon oil
kingford is a Circuit board manufacturer specializing in the manufacture of printed circuit boards. It has been dedicated to the production of single, double-sided and multi-layer circuit boards for 20 years. We can provide PCB proofing and mass production services such as FR4 hard board, FPC soft board, soft and hard combined board, HDI board and metal substrate.