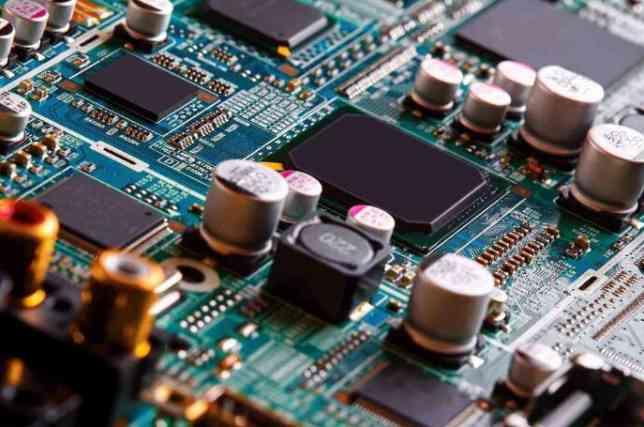
Wave-crest welding flux is the main electronic auxiliary material used in PCBA processing of electronic assembly. Its quality directly determines the reliability of subsequent products. The following is a brief description of the role of flux in wave soldering.
1 Remove the rust film on the surface of the metal to be welded. The rust film on the surface of the metal to be welded is usually insoluble in any solution, but the rust reacts with some materials to form compounds soluble in liquid spray pills, thereby removing the rust film and purifying the metal surface to be welded. The reaction may be a chemical reaction that dissolves the flux and the rust film in the flux or another compound in the flux solvent, or a chemical reaction that reduces the rust film to a pure metal surface. The fluxes belonging to the first chemical reaction are mainly represented by the loose-scented fluxes, and as examples of the second chemical reaction, some are reducing gases. For example, oxygen can reduce oxides on metal surfaces at high temperatures, producing water and restoring pure metal surfaces.
2 Prevent secondary oxidation of metal to be welded during heating. During wave soldering, the reoxidation of metal surface will increase with the increase of temperature. Therefore, the flux must provide protection for the cleaned metal surface, that is, the flux should form a film over the entire metal surface to coat the metal. It is insulated from air to prevent secondary oxidation of the metal to be welded during heating of the solder.
3 Reduce the surface tension of the liquid solder. The flux during welding may affect the energy balance of the surface by promoting solder flow, reducing the surface tension of the liquid solder, and reducing the contact Angle.
4. Heat transfer. Welded joint sections usually have many gaps, and the air in these gaps acts as a separator during the welding process, resulting in poor heat transfer. If these gaps are filled with flux, the heat transfer can be accelerated and the rate of heat achieved.
5 Promote the flow of liquid solder. After the preheated flux is in contact with the crest flux, the activity increases sharply, the viscosity decreases sharply, and the second flow is formed on the surface of the metal to be welded, and quickly dispersed on the surface of the metal to be welded. The flow created by the secondary flow of flux is added to the liquid solder, which delays the flow of the liquid metal,
Drag action of secondary flux flux on liquid solder
The flux coating system automatically and efficiently applies flux to the solder surface of the PCB board, using flux to break the oxide layer and remove loose oxide from the metal surface, thereby bringing the solder into direct contact with the base metal.
2. In PCBA processing, there are several process points in the whole process of rework and reflux
In PCBA processing, there are several process points in the whole process of rework and reflux.
The repair reflow welding curve should be close to the original welding curve. The thermal reflux curve can be divided into four zones: preheating zone, immersion temperature zone, reflux zone and cooling zone. You can set the temperature of each of the four zones, the time parameters, and you can store and call these programs at any time by connecting to your computer.
2 In the reflux process, the heating temperature and time of each area should be correctly selected, and the heating rate should be indicated. Generally, the maximum heating rate does not exceed 6°C/s before 100°C; After 100°C, the maximum heating rate does not exceed 3°C/s; In the cooling zone, the maximum cooling rate does not exceed °C/s. Excessive heating and cooling rates can damage PCBS and reworked components, sometimes making them invisible to the naked eye. Different components, should be for different heating temperature and time to choose different paste. For example, the return temperature of BGA chip should be higher than that of PBGA. 90% Pb and 10% Sn should be higher than 37% Pb and 63% Sn solder paste. For no-wash solder paste, its activity is lower than that of non-wash solder paste, so the welding temperature should not be too high, and the welding time should not be too long to prevent oxidation of solder particles.
3 The bottom of the PCB must be able to heat when hot air returns. Heating has two purposes: one is to avoid warping and deformation due to the heat on one side of the PCB; The second is to avoid heat. Another is to shorten the melting time of the solder paste. Bottom heating is especially important for large circuit board repair BGA. There are usually two ways to heat the underside of the repaired equipment: hot air heating and infrared heating. The advantage of hot air heating is that it heats evenly. In general, it is recommended to use heat during rework. The disadvantage of infrared heating is the uneven heating of PCB.
4 Choose a good hot air return nozzle. The hot air return nozzle is non-contact heating, and the high temperature air flow is used to simultaneously heat the solder of each solder spot on the BGA chip.
Cleaning after rework is usually partial cleaning. There are two methods: solvent cleaning and direct matching of flux. After cleaning, this method may still leave an unclear imprint. The second is to use a cleaning solution. Wash with water, which is usually followed by drying due to the presence of water, but is clean and meets the requirements of the relevant process standards.
Regardless of the type of rework and the type of rework tool used, although printed circuit components can meet quality levels due to the use of equipment and the skill of the operator, there are still many uncontrollable factors in the process. Objectively speaking, the quality of rework in the form of manual welding depends largely on the level of technology and the understanding of the operator. It is impossible to form a very consistent working effect in the short term. As a result, some degree of rework is required in some printed circuit components. Risk.
Although the current repair workstation system has greatly improved in terms of function, the accuracy of, is comparable to the automatic placement of equipment, but it is still manual operation, so operator training is very important. Secondly, in the construction of the welding device, because of its function and function, it is impossible to be compared with the modern seven temperature zone, ten temperature zone automatic reflux welding equipment. The control parameters of the thermal environment in the minimal area are limited, so the welding temperature curve is set as,.
The adjustment of solder joints formed by large packaging devices is very different, especially for components such as BGA and CSP. The shape, glossiness and smoothness of local solder joints are worse than those of reflow furnace.