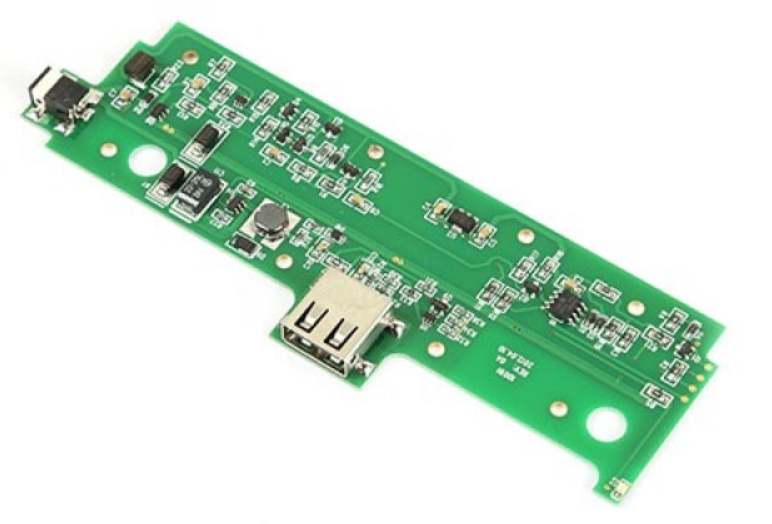
1. Three anti-corrosion paint, also known as PCBA circuit board protective oil, coating oil, moisture-proof paint, three anti-corrosion paint, waterproof glue, insulation paint, anti-corrosion paint, salt spray paint, dust-proof paint, protective paint, and coating, three anti-corrosion glue, etc. The PCBA circuit board using three anti-paint has waterproof, moisture-proof, dustproof, cold and heat shock resistance, aging resistance, radiation resistance, salt spray resistance, ozone corrosion resistance, vibration resistance, good flexibility, strong adhesion and other properties.
Moisture is the most common and destructive major factor in PCBA boards. Excessive moisture will greatly reduce the insulation resistance between conductors, accelerate high-speed decomposition, reduce Q value and corrode conductors. We often see copper rust in the metal parts of PCBA circuit boards.
Hundreds of contaminants found randomly on printed circuit boards are equally destructive. They lead to the same results as moisture corrosion-electron decay, conductor corrosion or even irreparable short circuits. Probably the most common contaminants in electrical systems are chemicals left over from the manufacturing process. Examples of these contaminants include flux, solvent release agents, metal particles, and marking inks. Other major pollutions are caused by human carelessness, such as body oil, fingerprints, cosmetics and food residues. There are also many pollutants in the operating environment, such as salt spray, sand, fuel, acid and other corrosive vapors and mold.
The printed circuit board and components are coated with three anti-corrosion paint, which can reduce or eliminate the deterioration of electronic performance when it may be affected by adverse factors in the operating environment. The purpose of coating is considered to have been achieved if the coating maintains its effect for a satisfactory period of time, if beyond the service life of the product.
Even if the coating is thin, it can withstand mechanical vibration and swing, thermal shock and high temperature operation to a certain extent. Of course, it is a mistake to think that thin films can be used to make individual parts inserted into printed circuit boards mechanically strong or sufficiently insulated. Components must be mechanically inserted securely and must have their own suitable caulk so that there is double insurance against accidents.
In order to meet customer demand for PCBA processing, kingford now adds a complete selective three-anti-paint coating line. We are mainly engaged in SMT patch processing. If you have any needs, please contact us.
2. The importance of X-ray quality detection after SMT patch processing
X-ray: The full name of X-ray nondestructive testing equipment, is the use of low-energy X-ray, the product internal scanning imaging, in order to detect the content of cracks, foreign bodies and other defects detection. This is the principle of X-ray scanning in living hospitals.
With the intellectualization and miniaturization of electronic products, the size of the chip is getting smaller and smaller, but the number of pins is increasing. In particular, some central BGA and IC components are used extensively. Due to the special packaging of chip internal welding condition detection can only be stopped with the aid of equipment. Ordinary artificial intelligence vision system detection can not fundamentally judge the quality of solder joints, and artificial vision inspection in the case of dense solder joints used to be the most inaccurate and repeatable option, the best choice is to X-ray stop batch inspection.
Urgent order, rapid proofing more need equipment to detect. X-ray detection technology is widely used in BGA welding quality inspection after reflow welding, so as to analyze the qualitative and quantitative risk of solder joint suspension, find quality anomalies and adjust them in time. According to the summary analysis of theoretical operation cases, the accuracy of X-ray inspection on the interior of BGA solder joints can exceed 15% of the artificial ICT detection, and the efficiency is more than 50%.
In the scope of application, the device can not only identify the welding defects (such as air welding, virtual welding) in the BGA, but also can stop scanning analysis of the micro-electronic system and sealing components, cables, fixtures, plastic interior, etc.
Therefore, for a processing plant and customers who have the understanding of quality and quality control, they should choose scientific technology and means to enhance and improve the production quality. Rather than just going through all kinds of false propaganda or indifferent attitude towards the end user.