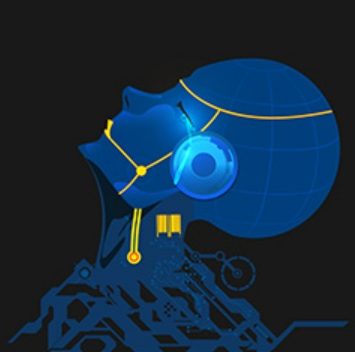
This is also a common phenomenon in the process of debugging, frequency reduction is mainly caused by two aspects. The input voltage and load voltage ratio is small, the system interference is large. For the former, be careful not to set the load voltage too high, although the load voltage is high, the efficiency will be high. For the latter, try the following:
1. Set the small current lower;
2. Clean wiring, especially the critical path of sense;
3. Select a small inductance or the inductance of a closed magnetic circuit;
4. Add RC low-pass filtering. The effect is a little bad. The consistency of C is not good and the deviation is a little large, but it should be enough for lighting.
There is no upside to downscaling anyway, only downside, so be sure to fix it.
Choice of inductor or transformer
With the same drive circuit, the inductance produced by a has no problem, and the inductance current produced by b becomes smaller. In this case, look at the inductive current waveform. Some do not notice this phenomenon, directly adjust the sense resistance or working frequency to reach the required current, which may seriously affect the service life of LED.
Therefore, before the design, reasonable calculation is perfect, if the theoretical calculation parameters and debugging parameters are a little far away, to consider whether the frequency reduction and transformer saturation. When the transformer is saturated, L will become smaller, resulting in a sharp rise in the peak current increment caused by transmission delay, so the peak current of LED will also increase. If the average current stays the same, you can only watch the light fade.
LED current size
We all know that if the LED ripple is too large, the LED life will be affected, how much impact, have not seen which said. I have asked the LED factory about this data before, and they said it is acceptable within 30%, but it has not been verified later. I suggest keeping it as small as possible. If the heat dissipation is not solved well, the LED must be derated. I also hope to have a specific index, otherwise it will affect the promotion of LED.
Etching quality and advanced problem analysis of PCB processing
The basic requirement for etching quality is to be able to remove all layers of copper except below the resist layer, and that is it. Strictly speaking, if it is to be defined, then the etching quality ** includes the consistency of wire width and the degree of side erosion. Due to the inherent characteristics of the present corrosion fluid, not only downward but also to the left and right direction of the etching action, so the side erosion is almost inevitable.
The problem of lateral erosion is one of the etch parameters which is often discussed. It is defined as the ratio of lateral erosion width to etching depth, which is called etching factor. In the printed circuit industry, it varies widely, from 1:1 to 1:5. Obviously, small side etch or low etching factor is desirable.
The structure of the etching equipment and the different composition of the etching solution can affect or control the etching factor or the degree of lateral erosion. The side erosion can be reduced by some additives. The chemical composition of these additives is generally a trade secret, and the respective developers are not disclosed to the outside world. As for the structure of the etching equipment, it will be discussed later.
In many ways, etching quality exists long before the printed circuit board enters the etching machine. Because there is a very close internal relationship between each process or process of printed circuit processing, there is no one is not affected by other processes and does not affect other processes. Many of the problems identified as etching quality actually exist in membrane removal and even in previous processes. The etching process of the outer layer graphics, because it reflects the "pour stream" is better than most of the printed circuit board process, so many problems are reflected in it. At the same time, this is also because etching is a self-laminating, sensitive beginning of a long series of processes in the last link, after which the outer pattern transfer is successful. The more links there are, the more likely there will be problems. This can be regarded as an important aspect of the printed circuit production process.
Theoretically speaking, the printed circuit into the etching stage, in the graphic electroplating process of printed circuit, the ideal state should be: the sum of the thickness of copper and tin after electroplating or copper and lead tin should not be the thickness of the electroplating film, so that the electroplating graphic film on both sides of the "wall" block and embedded in it. However, in reality, the printed circuit board in the world after electroplating, coating pattern is much thicker than the sensitive pattern. The problem arises in the process of plating copper and lead tin, which tends to accumulate laterally because the plating is too high for the sensitive film. A tin or lead tin resist covering the top of the line extends to both sides, forming a "rim" that covers a small portion of the sensitive film underneath the "rim".
The "edge" formed by tin or lead tin makes it impossible to remove the sensitive film when removing the film, leaving a small part of the "residual glue" under the "edge". The "residual glue" or "residual film" left behind the resist "along" will cause no etching. The lines form "copper roots" on both sides after etching, and the copper roots narrow the line spacing, resulting in printed circuit boards that do not meet the requirements of Party A, and may even be rejected. Because the rejection will make the production cost of PCB greatly increased.
In addition, in many cases, due to the reaction and dissolution, in the printed circuit industry, residual film and copper may also form accumulation in the corrosion fluid and blocked in the nozzle of the corrosion machine and acid pump, have to stop processing and cleaning, and affect the efficiency of the work.