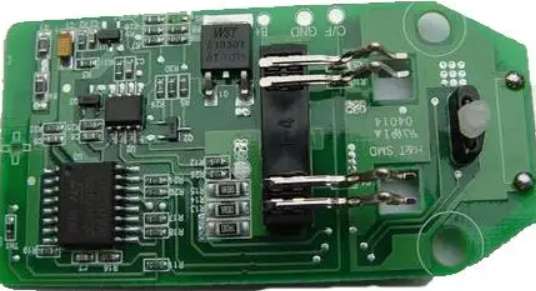
kingford is a professional PCBA processing manufacturer with its own PCB board factory and SMT patch processing factory. We can provide PCB design, PCB board making, component purchasing, SMT patch, DIP plug-in, PCBA testing, finished product assembly and other one-stop PCBA processing services. Next, how to select components and substrates for PCBA processing?
PCBA processing selection of components and substrate standards
1. Selection of components
The selection of components should fully consider the requirements of the actual area of the SMB. Conventional components should be selected as far as possible. Do not blindly pursue small-size components to avoid increasing costs. IC device should pay attention to pin shape and pin spacing; For less than 0.5mm pin spacing QFP should be carefully considered, it is better to directly choose BGA-packaged devices.
In addition, the packaging form of components, PCB weldability, reliability of smt mounting, temperature tolerance and other factors should be taken into account. After selecting components, a component database must be set up, including installation size, pin size and SMT manufacturer.
2. Selection of substrate
Select the substrate based on the SMB service conditions and mechanical and electrical performance requirements. Determine the number of copper-covered foil surfaces (single, double or multilayer) of the substrate according to SMB structure; Determine the thickness of the substrate based on the SMB size and the weight of the component per unit area. When selecting SMB substrates, factors such as electrical performance requirements, Tg value (glass transition temperature), CTE, flatness, and price should be considered.
1. Customers place orders
Customers place orders according to their actual needs of PCBA processing plants, and put forward specific requirements. The processing plant will evaluate its capacity to see if it can fulfill the order. If the manufacturer is sure that they can complete the order within the expected time, then the two parties will negotiate to determine the production details.
2. Production materials provided by customers
After the customer decides to place an order, he shall provide a series of documents and lists to the PCBA processing plant, such as PCB electronic files, coordinate files, BOM list and so on, which must be provided.
3. Purchase raw materials
PCBA processing plant purchases relevant raw materials from designated suppliers according to the documents provided by customers.
4. Incoming material inspection
Before PCBA processing, strict quality inspection is carried out for all raw materials to be used to ensure that they are qualified before being put into production.
5. PCBA production
In the process of PCBA processing, in order to ensure the quality of production, whether it is patch or welding production, the manufacturer needs to strictly control the furnace temperature.
6. PCBA test
The PCBA processing plant conducts rigorous product testing, and the PCB board that passes the test is delivered to the customer.
7. Packaging after sale
After the PCBA processing is completed, the products are packaged and then handed over to the customer to complete the whole PCBA processing.
2. What is the layout of SMT factory?
Shenzhen kingford has its own SMT plant, which can provide SMT SMT processing services of 0201 components with minimum package, support the processing of incoming materials and samples and OEM. Next, how to introduce the layout of SMT factory?
SMT factory layout and location requirements
1. Placing area of fire extinguisher
The fire extinguisher shall be placed next to the column and around the SMT workshop in accordance with the fire regulations.
2. Placing area of the material rack car
The material rack car is used for SMT production line and material replacement during machine type switching. In order to facilitate production and improve the efficiency of material replacement, it is better to place the material rack car near the SMT machine. Moreover, because the material can be replaced on both sides of the front and rear of the SMT machine, at least one material rack car is placed on both sides of the front and rear of the SMT machine.
3. Placing area of the material preparation table
The material preparation table is mainly used for material preparation in the production process and material preparation before machine type switching. Therefore, the material preparation table should be placed near the SMT machine, and it is best to put it together with the material rack car, so that it is convenient to put the material directly on the material rack car after preparing the material.
4. Small table placement area of printing station
Printing station table is used for placing auxiliary tools of printing press in production, such as wiping paper, solder paste, alcohol, etc., which should be placed near the printing press for easy access and use to improve production efficiency.
5. Tin paste placement area
The tin paste placing area includes the refrigerator for storing the tin paste, the tin paste mixer, the tin paste return temperature cabinet, etc., which can be placed next to the column or in a fixed area around the workshop according to the requirements of the workshop, but it should be easy to access the tin paste in the production line.
6. Visual inspection area and maintenance area behind the furnace
In order to facilitate the visual inspection and maintenance of semi-finished products after the furnace, a small table is generally placed behind the furnace, which is specially used for the visual inspection and maintenance after the furnace, so that the products produced can be carried out in the next link of operation in time.
7, the grid placement area
The screen board placing area includes the screen board placing cabinet, screen board cleaning machine, screen board inspection tools, etc., used for screen board storage, cleaning and screen tension inspection, but to facilitate the use of the screen board in the production line.
8. Garbage placement area
The waste in production mainly comes from two parts, one is the dust-free paper used in the printing operation, the other is the waste tray and waste strip produced by the material replacement. The waste generated by these two parts should be placed separately for recycling, especially the waste used by the printing press. Therefore, garbage areas can be placed next to the printing press and the laminator or garbage areas can be placed next to the column and placed separately.
9. Kanban placement area
SMT Kanban includes production Kanban and quality management Kanban, etc., which can be centrally placed next to the entrance to the workshop or set up production Kanban at each production line and centrally placed quality Kanban, so as to facilitate the viewing of producers and managers and timely understanding of the current production and quality status of the SMT workshop.
10. Product placement area
The products produced include finished products and semi-finished products. These two parts should be divided and strictly distinguished to avoid confusion.
11. SMT spare parts placement area
Nozzle SMT spare parts include nozzle, motor, belt, cylinder and so on. Nozzle should be put in a special area so that nozzle is convenient for people to have, especially expensive spare parts, and nozzle should be set safely.
12. Temperature and humidity position area
In order to better understand the temperature and humidity of SMT workshop, several temperature and humidity measuring areas are appropriately set up according to the size of the workshop area, which are generally placed on the column or wall beside the production line.
13. Office area of SMT workshop
Let engineers and managers work in the SMT workshop, so as to timely solve the technical and management problems encountered in production and ensure the smooth production of the SMT production line.
14. Area for anti-static measures
Personnel entering the SMT workshop must have an area to take anti-static measures. This area can be designated at the door of the workshop, including changing electrostatic clothes, shoes, hats and locker for each employee. In addition, a special area for electrostatic ring testing should be set up at the entrance of the SMT workshop, so that each employee can do electrostatic ring testing and record the test results before going to work.
Why kingford?
1. Strength guarantee
▪SMT workshop: We have imported SMT machines and several sets of optical inspection equipment, with a daily output of 4 million. Each process is equipped with QC personnel, who can keep an eye on product quality.
▪DIP production line: We have two wave-soldering machines, among which there are more than 10 old employees who have worked for more than three years. The skilled workers can weld all kinds of plug-in materials.
2. Quality assurance, cost-effective
▪ High-end equipment can stick precision shaped parts, BGA, QFN, 0201 materials. Can also template patch, loose material hand.
▪ Sample and size batch can be produced, proofing from 800 yuan, batch 0.008 yuan/point, no start-up fee.
3. Rich experience in SMT and welding of electronic products, stable delivery
▪ Accumulated SMT SMT processing services for thousands of electronic enterprises, involving many kinds of automotive equipment and industrial control motherboard. The products are often exported to Europe and the United States, and the quality can be affirmed by new and old customers.
▪ On time delivery, normal 3-5 days after complete materials, small batch can also be expedited on the same day shipment.
4. Strong maintenance ability and perfect after-sales service
▪ Experienced maintenance engineers can repair all kinds of patch welding caused by bad products, to ensure the connection rate of each piece of circuit board.
▪ 24-hour customer service staff at any time response, the fastest speed to solve your order problems.