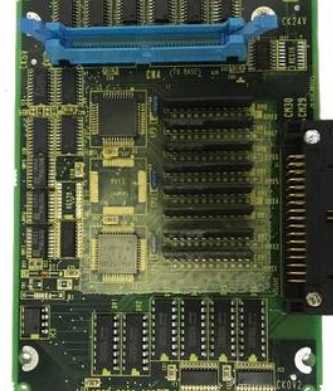
An important measure of profitability of a company or line in SMT patch processing is the "pass through rate." Similarly, for customers requiring PCBA processing, the through-through rate means whether the delivery date can be maximized. The higher the through-through rate, the shorter the delivery date. So what are the factors that affect the pass rate in SMT patch processing?
In the face of through-through rate, we summarized two modules, one is before production, the other is after production. Today we will focus on the analysis of the pre-production, that is, the process design stage.
The process design for pass-through rate is mainly through PCB process refinement design to ensure the manufacture of veneer with zero defects. In general, we hear mostly about design for Manufacturing (DFM), process design for pass-through rate is rarely heard because most factories don't have this knowledge, and if they do, they don't realize the importance and complexity of pass-through design.
First, the process design of pass-through rate needs the support of experienced engineers. Process design for pass-through rate usually needs to be realized through the following stages:
(1) Master a large number of typical cases.
(2) To understand the process characteristics of each kind of packaging - easy to produce what problems.
(3) Understand the mechanism and cause of each adverse phenomenon.
(4) Master effective solutions and measures.
Two, if SMT factory has not gone through these processes, it is difficult to achieve pass-through rate oriented process design! In the production stage, there are five main technological means to improve the straight-through rate, which can be improved:
(1) Optimize the design of steel mesh.
(2) Choose the appropriate solder paste.
(3) Optimize the printing operation.
(4) Optimize the temperature curve.
(5) Adopt tooling and improve the process method.
2. Judge and solve the SMT patch welding method
SMT soldering voiding is the process of iding of the SMT patch with a gap below the solder spot, resulting in an unwelded or incomplete weld. This phenomenon will reduce the reliability of solder joints and connection performance, leading to poor operation and failure of electronic equipment.
The following is the method to judge and solve the SMT patch welding:
Judging virtual welding:
1. Appearance inspection: the surface smoothness of solder joints is insufficient, the color of solder joints is abnormal or the size of solder joints is inconsistent.
2. X-ray inspection: X-ray machine is used to scan the solder joints to check whether there are gaps or bubbles below the solder joints.
3. Gold wire measurement: Before and after welding of the SMT patch, the solder joint shall be measured with gold wire to measure whether there is any gap or air bubble below the solder joint.
Solve virtual welding:
1. Control welding temperature: Reasonable control of welding temperature can avoid the formation of bubbles and voids below the welding spot. If the welding temperature is too high, the material below the solder joint will produce gas, resulting in virtual welding.
2. Change the thickness of PCB board: Increasing the thickness of PCB board can increase the time of heat conduction and reduce the generation of gas below the solder joint, thus reducing the possibility of virtual welding.
3. Change welding materials: Using high quality welding materials can reduce the occurrence of virtual welding. Bubbles below the solder joint can be improved by using appropriate solder alloys and fluxes.
4. PCB board design optimization: Reasonable optimization of PCB board design can reduce the number of welding points, thus reducing the occurrence of virtual welding.
5. Optimization of welding process: Reasonable optimization of welding process can reduce the fluctuation of welding temperature, thus reducing the occurrence of virtual welding. At the same time, reasonable control of welding speed, can make solder better fill solder spot, reduce the bubble below the solder spot.
Shenzhen kingford is a professional PCBA OEM manufacturer, which can provide one-stop services from upstream electronic components procurement to PCB production and processing, SMT patches, DIP plug-ins, PCBA testing, finished product assembly, etc.