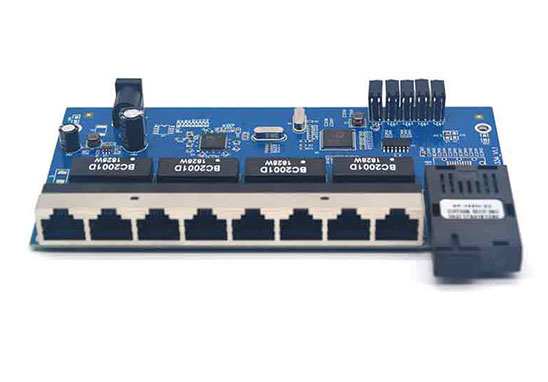
PCBA board repair is a very important link in the processing of PCBA. Once it is not handled properly, it will lead to the scrap of PCBA board and affect the yield. So, what are the PCBA board repair requirements? Next, Shenzhen PCBA processing manufacturer -kingford for you to introduce.
PCBA board repair requirements
1. Baking requirements of PCBA and moisture sensitive components
1. All new components to be installed must be baked and dehumidified according to the humidity sensitivity level and storage conditions of the components, and in accordance with the relevant requirements in the Specifications for the Use of Moisture Sensitive Components.
2. If the repair process needs to be heated to more than 110℃, or there are other moisture-sensitive components within 5mm around the repair area, it must be baked and dehumidified according to the humidity sensitive grade and storage conditions of the components, and in accordance with the relevant requirements in the Specifications for the Use of moisture-Sensitive Components.
3. For the moisture sensitive components that need to be reused after repair, if hot air reflux, infrared and other repair processes are used to heat the solder joints through the package body of the components, they must be baked and dehumidified according to the humidity sensitive grade and storage conditions of the components, and in accordance with the relevant requirements in the Specifications for Use of Moisture Sensitive Components. For the repair process of manual chromite heating solder joint, under the premise that the heating process is controlled, pre-baking can be dispensed with.
2. Storage environment requirements for PCBA and components after baking
If the storage conditions of baked moisture sensitive components, PCbas, and unpacked new components to be replaced exceed the expiration date, bake them again.
3. Requirements for heating times of PCBA repair
The component is allowed to repair heating accumulative not more than 4 times; The allowable number of rerepair heating for new components shall not exceed 5 times; The reheating times of the reusing components removed from the top shall not exceed 3 times.
2. Analysis of common adverse phenomena in PCBA processing
In the process of processing and production of PCBA, there may be some errors in operation, leading to the adverse phenomenon of the patch. So, what adverse phenomena will occur in PCBA processing?
PCBA processing common adverse phenomenon
1. Tilt up
Causes: the size of both sides of the copper platinum produced uneven tension; The preheating rate is too fast; Machine mounting offset; Uneven solder paste printing thickness; Uneven temperature distribution in the back welding furnace; Solder paste printing offset; Machine track splint is not tight resulting in mounting deviation.
2. Short circuit
Causes: the spacing between steel mesh and PCB board is too large, resulting in thick solder paste printing, resulting in short circuit; Too low component mounting height will squeeze the solder paste resulting in short circuit; High temperature of backwelding furnace leads to short circuit; Component mounting offset resulting in short circuit; The opening of steel mesh is not good (too thick, too long pin opening, too large opening), resulting in short circuit, etc.
3. Offset
Cause: the positioning reference point on the circuit board is not clear; The positioning datum point on the circuit board and the datum point of the grid board are not aligned; Circuit board in the printing press fixed clamping loose, positioning thimble is not in place.
4. Missing parts
Causes: vacuum pump carbon sheet poor vacuum is not enough to cause the lack of parts; Plug or bad suction nozzle; Improper component thickness detection or bad detector; Mounting height is set improperly, etc.
5, air welding
Causes: the activity of tin paste is weak; Steel mesh opening is not good; Copper platinum spacing is too large or large copper paste small components; Scraper pressure is too large; Element foot flatness is not good (foot warping, deformation) back welding furnace preheating area too fast.
Why choose Shenzhen Honglijie to do PCBA processing?
1. Strength guarantee
▪SMT workshop: We have imported SMT machines and several sets of optical inspection equipment, with a daily output of 4 million. Each process is equipped with QC personnel, who can keep an eye on product quality.
▪DIP production line: We have two wave-soldering machines, among which there are more than 10 old employees who have worked for more than three years. The skilled workers can weld all kinds of plug-in materials.
2. Quality assurance, cost-effective
▪ High-end equipment can stick precision shaped parts, BGA, QFN, 0201 materials. Can also template patch, loose material hand.
▪ Sample and size batch can be produced, proofing from 800 yuan, batch 0.008 yuan/point, no start-up fee.
3. Rich experience in SMT and welding of electronic products, stable delivery
▪ Accumulated SMT SMT processing services for thousands of electronic enterprises, involving many kinds of automotive equipment and industrial control motherboard. The products are often exported to Europe and the United States, and the quality can be affirmed by new and old customers.
▪ On time delivery, normal 3-5 days after complete materials, small batch can also be expedited on the same day shipment.
4. Strong maintenance ability and perfect after-sales service
▪ Experienced maintenance engineers can repair all kinds of patch welding caused by bad products, to ensure the connection rate of each piece of circuit board.
▪ 24-hour customer service staff at any time response, the fastest speed to solve your order problems.