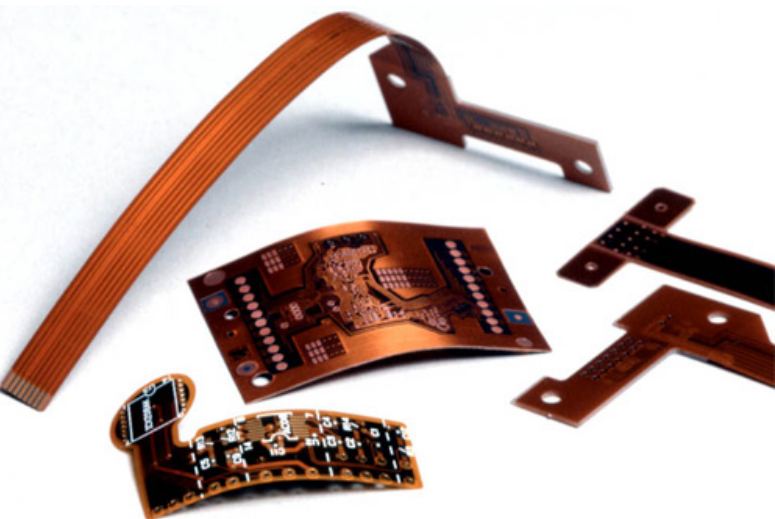
One. Pretreatment of FPC
The FPC board is soft and not vacuum packed when leaving the factory. It is easy to absorb moisture in the air during transportation and storage. It needs to be pre-baked before SMT line casting to slowly force out the moisture. Otherwise, under the high temperature impact of reflow welding, the water absorbed by FPC will be quickly vaporized into steam to highlight FPC, which is easy to cause bad FPC delamination and foaming.
Pre-baking conditions are generally 80-100℃ for 4-8 hours. In special cases, the temperature can be adjusted to more than 125℃, but the baking time should be shortened accordingly. Before baking, always do a sample test to determine if the FPC can withstand the set baking temperature, you can also consult the FPC manufacturer for suitable baking conditions. When baking, the FPC stack should not be too much, 10-20PNL is suitable, some FPC manufacturers will put a piece of paper in between each PNL for isolation, need to confirm whether the isolation paper can withstand the set baking temperature, if not, need to remove the isolation paper, then bake. After baking, the FPC should have no obvious discoloration, deformation, warping and other bad, which should be inspected by IPQC before casting.
Two .Manufacture of special carrier board
According to the CAD file of the circuit board, the hole positioning data of the FPC is read to manufacture the high-precision FPC positioning template and special carrier plate, so that the diameter of the positioning pin on the positioning template and the aperture of the positioning hole on the carrier plate match. Many FPC are not the same thickness because they want to protect part of the line or for design reasons, some places are thick and some places are thin, and some have to strengthen the metal plate, so the joint of the carrier plate and FPC needs to be processed and polished according to the actual situation, the role is to ensure that the FPC is smooth when printing and mounting. The material of the carrier plate is required to be thin, high strength, less heat absorption, fast heat dissipation, and small warpage deformation after multiple thermal shocks. Commonly used load plate materials are synthetic stone, aluminum plate, silicone plate, special high temperature resistant magnetized steel plate, etc.
Three. The production process.
Here, we take ordinary carrier board as an example to detail the SMT points of FPC. When using silicone plate or magnetic fixture, the fixation of FPC is much more convenient, without using tape, and the process points of printing, patch, welding and other processes are the same.
1. Fixation of FPC:
Before SMT, the FPC needs to be precisely secured to the carrier plate. In particular, the shorter the storage time between the FPC being fixed to the carrier plate and printing, mounting and welding, the better. There are two kinds of carrier plates with and without dowel pins. A carrier plate without positioning pins must be used together with a positioning template with positioning pins. Put the carrier plate on the positioning pins of the template so that the positioning pins are exposed through the positioning holes on the carrier plate. Put the FPC on the exposed positioning pins one piece at a time, and then secure the carrier plate with adhesive tape. A number of spring positioning pins of about 1.5mm in length are fixed on the load plate with positioning pins. One piece of FPC can be directly set on the spring positioning pins of the load plate, and then fixed with adhesive tape. In the printing process, the spring positioning pin can be completely pressed into the load plate by the steel mesh, without affecting the printing effect.
Method 1 (single-side adhesive tape) : Use thin high-temperature resistant single-side adhesive tape to fix four sides of the FPC on the carrier plate to prevent deviation and warping of the FPC. The viscosity of the adhesive tape should be moderate, it must be easy to peel off after reflow welding, and there is no adhesive residue on the FPC. If the automatic tape machine is used, it can quickly cut the tape of the same length, which can significantly improve efficiency, save costs and avoid waste.
Method 2 (fixed with double-sided tape) : First, use high-temperature resistant double-sided tape to stick to the carrier plate, the effect is the same as that of the silicone plate, and then paste FPC to the carrier plate. Pay special attention to the viscosity of the tape should not be too high, otherwise it is easy to cause FPC tear when stripping after reflow welding. After repeated furnace, the viscosity of double-sided tape will gradually decrease. When the viscosity is too low to reliably fix FPC, it must be replaced immediately. This station is the key station to prevent FPC from fouling, so it is necessary to wear finger sleeves. Before the carrier board is reused, it is necessary to clean it properly. You can scrub it with non-woven cloth dipped in cleaning agent or use an anti-static dust drum to remove surface dust, tin beads and other foreign bodies. Do not use too much force when taking and putting FPC, FPC is fragile, easy to produce crease and fracture.
2. Solder paste printing of FPC:
FPC has no special requirements on the composition of the solder paste, the size of the tin ball particles and metal content to FPC there is no fine spacing IC prevail, but FPC on the printing performance of the solder paste is higher, the solder paste should have excellent thixotropy, solder paste should be easy to print and release and can firmly adhere to the surface of the FPC, There will be no bad demoulding blocking steel mesh holes or collapse after printing.
Because the carrier board is loaded with FPC, FPC is equipped with high temperature resistant tape for positioning, so that its plane is inconsistent, so the printing surface of FPC can not be flat like PCB board and the thickness of the same hardness, so it is not suitable to use metal scraper, but should use the hardness of 80-90 degrees of polyamine ester scraper. It is better for solder paste press to have optical positioning system, otherwise it will have a great impact on the printing quality. Although FPC is fixed on the carrier board, there will always be some small gap between FPC and the carrier board, which is the biggest difference with PCB hard board, so the setting of equipment parameters will also have a great impact on the printing effect.
Printing station is also the key station to prevent FPC dirt, need to wear finger cover operation, at the same time to keep the station clean, often wipe the steel mesh, to prevent solder paste pollution of the gold finger and gold buttons of FPC.
3. FPC patch:
According to the characteristics of the product, the number of components and the efficiency of the patch, the use of medium and high speed patch machine can be mounted. Since each FPC has an optical MARK for positioning, SMD mounting on an FPC is not very different from mounting on a PCB board. It should be noted that although the FPC is fixed on the carrier plate, its surface can not be as flat as PCB hard board. There must be local gaps between the FPC and the carrier plate. Therefore, the lowering height and blowing pressure of the suction nozzle need to be precisely set, and the moving speed of the suction nozzle needs to be reduced. At the same time, the majority of FPCS are connected plates, and the finished product rate of FPCS is relatively low, so it is normal for the whole PNL to contain some defective PCS, which requires the BAD MARK recognition function of the SMT machine, otherwise, the production efficiency will be greatly reduced when the production of this kind of non-integrated PNL is good.
4. Reflow welding of FPC:
Mandatory hot air convection infrared reflow furnace should be used, so that the temperature on the FPC can be more uniform change, reduce the occurrence of poor welding. If single-sided tape is used, it can only fix the four sides of the FPC, and the middle part is deformed in the hot air condition, so that the welding plate is prone to tilt, and the molten tin (liquid tin at high temperature) will flow and produce air welding, continuous welding and tin beads, so that the process defect rate is high.
(1) Test method of temperature curve:
Due to the different heat absorption properties of the carrier plate and the different types of components on the FPC, their temperature rises at different rates after being heated in the reflow welding process, and the heat absorbed is also different. Therefore, carefully setting the temperature curve of reflow furnace has a great influence on the welding quality. A more secure method is to place two load plates equipped with FPC on the front and back of the test plate according to the actual load plate spacing during birth. At the same time, attach mounting components to the FPC of the test plate, weld the test temperature probe to the test point with high temperature solder wire, and fix the probe wire on the load plate with high temperature resistant tape. Note that the heat resistant tape will not cover the test site. The test points should be selected near the solder joints and QFP pins on each side of the carrier plate, so that the test results can better reflect the real situation.
(2) Setting of temperature curve:
In the furnace temperature debugging, because the FPC temperature uniformity is not good, so it is best to use the temperature curve of temperature rise/heat preservation/reflux, so that the parameters of each temperature area is easy to control some, in addition, FPC and components are less affected by heat shock. According to experience, it is best to adjust the furnace temperature to the lower limit of the technical requirements of the solder paste. The wind speed of the backwelding furnace generally adopts the lowest wind speed that the furnace can adopt. The chain stability of the backwelding furnace is better and there can be no shaking.
5. Inspection, testing and sub-board of FPC:
Because the carrier plate absorbs heat in the furnace, especially the aluminum carrier plate, the temperature is higher when it comes out of the oven, so it is best to add a forced cooling fan at the mouth of the oven to help rapid cooling. At the same time, operators need to wear heat insulation gloves to avoid being burned by the high temperature load plate. When taking the FPC finished welding from the carrier plate, the force should be even, do not use brute force, so as to avoid tearing or creasing the FPC.
The removed FPC was placed under a magnifying glass at least 5 times for visual inspection, focusing on surface residual glue, discoloration, golden finger tin, tin beads, IC pin empty welding, continuous welding and other problems. Since the surface of FPC cannot be very smooth, resulting in a high misjudgment rate of AOI, the FPC is generally not suitable for AOI inspection, but with the help of special test fixtures, the FPC can complete the ICT and FCT testing.
Since most FPCS are connected boards, it may be necessary to make sub-boards before conducting ICT and FCT tests. Although sub-boards can be completed by using blades, scissors and other tools, the working efficiency and quality are low, and the scrap rate is high. If it is the mass production of special-shaped FPC, it is recommended to make special FPC stamping die, stamping division, can greatly improve the efficiency of the operation, at the same time, the FPC edge of the punching is neat and beautiful, the internal stress generated when the stamping plate is very low, can effectively avoid solder joint crack.
In the assembly and welding process of PCBA flexible electronics, the precise positioning and fixing of FPC are the key points, and the key of fixing is to make suitable carrier plate. This is followed by pre-baking, printing, patching and reflow soldering of FPCS. Obviously, SMT process of FPC is much more difficult than PCB hard board, so it is necessary to set process parameters accurately. Meanwhile, strict production process management is equally important. It is necessary to ensure that operators strictly implement every provision of SOP, line tracking engineers and IPQC should strengthen inspection, timely discover abnormal conditions of production line, analyze the causes and take necessary measures. In order to control the defect rate of FPC SMT production line within dozens of PPM.