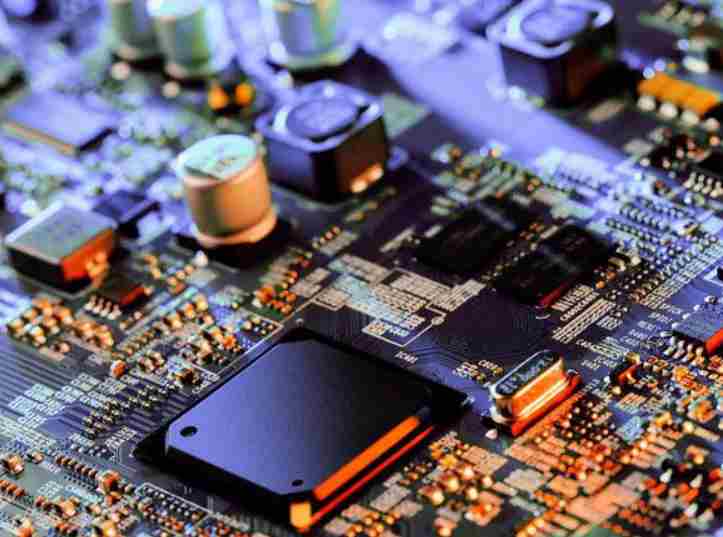
1. Do you think PCBA circuit board welding must use the traditional process of SMT patch processing? Do you think SMT process can solve all component welding requirements? Do you think traditional component packaging can solve all the problems? In recent years, under the environmental requirements such as ultra-high density and lead-free Pich40um, ACA((Anisotropic Conductive Adhesive) ACF (Anisotropic Conductive Film) and solder resin conductive material ESC (Epoxy conductive material) Solder Connection) all belong to ECA (Electrically Conductive Adhesives.) technology. ECA technology is on the rise.
First, ACA, ACF technology
There are two kinds of anisotropic conductive adhesive: paste and film. ACA is paste paste. Acfs are thin films, usually machined into sea strips of varying widths according to the requirements of the application. ACA and ACF materials have conductive spherical particles floating in them. Using this glue or sea film tape, the flip chip is attached to the substrate, and when the conductors are pressed together in reverse, a conductive path appears in the Z-axis direction.
Second, the advantages and applications of anisotropic conductive adhesive (ACA) compared with traditional tin lead solder
① It is suitable for ultra-fine spacing (50um), which is an order of magnitude narrower than the solder interconnection spacing, which is conducive to further miniaturization of packaging.
②ACA has a low curing temperature, so it is particularly suitable for the interconnection of heat-sensitive components and non-weldable surfaces.
(3) The interconnection process of ACA is very simple with few process steps, which is conducive to improving production efficiency and reducing costs.
(4) ACA has higher flexibility and better thermal expansion coefficient matching, which improves the environmental adaptability of interconnect points and reduces the failure.
⑤ Save the process of packaging
ACA belongs to the green electronic packaging material, does not contain lead and other toxic metals.
As a result of the above excellent performance, ACA technology has been widely used in IC packages interconnected by flip chips and in the interconnection between flexible plate cable and hard plate. For example, LCD display, personal digital assistant (PDA), global positioning system (GPS), mobile phones, game consoles, laptops, HDD (hard disk actuator) head, memory module, the IC connection in the photoelectric coupler devices such as internal, mostly by ACA or ACF interconnection.
Iii. Bonding principle and technology of ACF interconnection devices
ACF is a thin film formed by mixing a certain amount (generally 3% ~ 15%, percentage by volume) of conductive particles into a polymer matrix (such as epoxy based glue). The conducting particles are generally spherical resin particles coated with Ni/Au on the surface. Before bonding, the conductive particles in the anisotropic conductive adhesive are generally approximately evenly distributed and do not contact each other. The well is protected by a layer of insulating film, so the ACF film itself is non-conductive. The unused anisotropic conductive film generally has two layers of protective film, which need to be removed before bonding. Generally, the ACF bonding process includes two processes: pre-bonding and bonding. When the ACF membrane is pressurized and heated, it will become softened (in a colloidal state), and the conductive particles can flow and be evenly distributed, so that each line has a certain number of conductive particles, ensuring a stable resistance value. Under the action of bonding pressure, the insulating film of conductive particles is broken, and there are several electrically deformed conductive particles sandwiched between the convex points on the wafer and the ITO circuit on the corresponding glass substrate. By these deformed conductive particles, the electrical interconnection between the upper and lower convex points is realized, and particles in other areas without pressure are not in contact with each other. Therefore, anisotropic interconnection is realized. After curing, the mechanical support and heat dissipation of electronic packaging are realized. The bonding principle of COG devices and the deformation mechanism of conductive particles in the bonding process.
2.ESC technology
With the progress of science and technology, technology is also constantly developing and changing. Take SMT patch processing as an example, in addition to the most common patch processing methods of PCB circuit board and reflow soldering of printed solder paste, we also have many special processes based on product characteristics, such as bonding, DIP plug-in and so on, among which ESC is also a welding process.
ESC (Epoxy coated Solder Connection) technology is epoxy resin sealed welding method, which uses new resin coated solder to heat the connection. ESC technology is a new technology to replace ACF, which simplifies the process and reduces the cost.
1. ESC technology and technology
ESC technology is shown in the figure below. First, the solder paste resin glue is dripped on the pad of the hard plate, and then the electrode of the soft plate is aligned and pasted on the pad of the hard plate. Finally, welding and resin curing are realized simultaneously through heating and pressure.
ESC technology
Two, ESC and ACF technology comparison
ACF technology has some shortcomings in process and connection strength. From the comparison between Figure 2 and Figure 3, ACF is more complex than ESC. ESC has the following advantages compared with ACF:
① The process is simple, saving the space of ACF tape;
② Welding + resin curing, enhance the connection radian, improve the reliability;
③ More application areas.
Three, the application of ESC technology
① New development of Flip Chip assembly technology. ESC technology can realize Flip Chip reflow welding and bottom filling glue curing.
②MM-ESC technology (module and module combination technology).
The new generation of mobile phones without connectors between the substrate technology
Using ESC technology can realize the connectionless connection between the five modules of the new generation mobile phone, saving space, reducing the thickness of the machine, but also improve the connection strength and reliability.