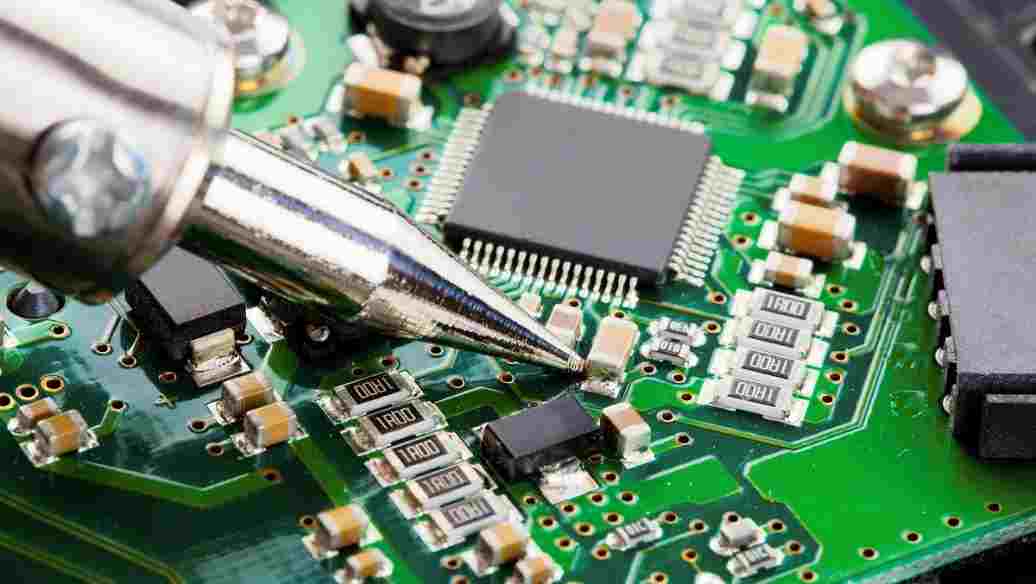
①PCBA welding from peak temperature to freezing point
This area is the liquid phase, and too slow cooling rate is equivalent to increasing the time above the liquid phase, which will not only make the IMC thickening rapidly, but also affect the formation of solder joint microstructure, which has a great impact on solder joint quality. For example, when welding lead-free Sn-Ag-Cu material and PCB solder pad impregnated with Sn or Cu /OSP coating, The slower cooling rate increases the formation of Ag3sn and Cu6Sn5. Sn-Ag-Cu solder with ENIG pad will increase the formation of NiSn4. The faster cooling rate is beneficial to reduce the formation rate of IMC.
Rapid cooling near the freezing point (between 220 and 200℃) is conducive to reducing the plastic time range of the non-eutectic lead-free solder during solidification. For example, the melting point range of Sn-Ag-Cu solder is between 20 and 216℃, and the plastic time range is short. Rapid cooling and solidification is conducive to the formation of fine crystalline particles and the formation of the densified structure. Help to improve SMT solder joint strength. Shortening the time of PCB assembly board at high temperature is also conducive to reducing the damage to thermal components.
One of the studies that did a series of technological experiments on various cooling slopes was this; A particular assembly plate is divided into two groups for reflow welding at two different cooling rates. The heating rate and preheating time of the first two temperature zones in the two groups are exactly the same, but two completely different cooling rates are used in the liquid phase zone. The first group uses a slow cooling rate, the second group uses a fast cooling rate, and then compare.
In the liquid phase, rapid cooling can shorten the liquid phase time, reduce the temperature difference (△T) between the largest and smallest components on the PCB surface, and inhibit the IMC growth rate.
About liquid phase area rapid cooling rate to reduce the PCB surface maximum and minimum element delta ア theory is as follows: With a fast cooling rate, heat energy is dispersed to the furnace, and little remains in the assembly plate, which allows the assembly plate to cool quickly, while no internal heat lines remain in the plate phenomenon occurs. For a slow cooling rate, residual heat energy inside the assembly plate will be released into the environment, rapid cooling rate comparison, Will keep the assembly plate and seemingly cooled components at high temperatures for a period of time. Even though delta T between the two curves is only about 1 ° C. However, it still has some influence on the demanding PCBA lead-free process window.
In addition, it should be noted that rapid cooling will increase the internal stress of solder joints, which may cause solder joints cracks and component cracking of SMT patches. Because in the welding process, especially in the welding spot solidification process, the thermal expansion coefficient (CTE) or thermal performance of various materials (different solder, PCB material, Cu, Ni, Fe-Ni alloy) is very different, such as the CTE of Sn-Ag-Cu is 15.5 ~ 17.1x10 of the minus sixth power /℃, The CTE of Sn-Pb is 21ppm/℃, the CTE of ceramics is 5ppm/℃, the CTE of PCB FR-4 is 11 ~ 15*10 minus sixth power /℃ in horizontal direction, 60 ~ 80ppm/℃ in vertical direction, and the CTE of epoxy resin is also 60 ~ 80ppm/℃. Therefore, welding defects such as cracking of related materials and breakage of coating in PCB metallization hole during solder joint solidification are found. The cooling rate of Sn-Ag-Cu alloy from the peak temperature to the freezing point (245 ~ 217℃) is generally controlled at -2 ~ -6℃/s.
② From the solder alloy solid line (freezing point) below near to 100℃.
Too long time from the solid phase line of solder alloy (the freezing point of Sn-Ag-Cu alloy is 216℃) to 100℃, on the one hand, will increase the thickness of IMC, on the other hand, for some interfaces with low melting point metal elements (such as lead-free components with Bi coating on the welding end), segregation phenomenon may occur due to the formation of dendritic crystals. Easy to cause solder joint stripping defects. In order to avoid the formation of dendritic crystals, cooling should be accelerated, and the cooling rate from 216 ~ 100℃ is generally controlled at -2 ~ -4℃/s.
③100℃ to the outlet of the reflow welding furnace.
To protect operators, the temperature at the outlet should be lower than 60 ° C. Different furnace outlet temperature is not the same, cooling rate is high and cooling zone long equipment, outlet temperature is lower. In addition, theoretical studies believe that the thickness of IMC will increase during the aging process of lead-free solder joints. Therefore, from 100℃ to the outlet of the reflow welding furnace, too long time will increase the thickness of IMC.
In a word, the cooling rate has a great influence on the welding quality of PCBA, because the microstructure inside the solder joint and the defects inside the solder joint, components and printed board cannot be detected from the appearance detection. This will affect the long-term reliability of electronic products. So. It is important to have a controlled cooling process. Especially for amorphous lead-free filler metal, the cooling speed should be strictly controlled.
2. Overview of electrical reliability of PCBA manufacturing
Usually, the same PCB circuit board is processed by SMT reflow welding, wave soldering, and repair processes, which may result in different residues. Under a humid environment and a certain voltage, electrochemical reactions may occur between the PCB circuit board and the conductor, resulting in the decrease of the surface insulation resistance (SIR). If electromigration and dendritic crystal growth occur, a short circuit between wires will occur, resulting in the risk of electromigration (commonly known as "leakage").
An overview of the electrical reliability of PCBA manufacturing
In order to ensure electrical reliability, it is necessary to evaluate the performance of different no-clean flux. The same flux should be used for the same PCB as far as possible, or be cleaned after welding.
According to the reliability analysis of seven aspects of solder joint mechanical strength, tin whisker, cavity, crack, intermetallic compound cellular, mechanical vibration failure, thermal cycle failure, electrical reliability, any kind of failure is more likely to occur in the solder joint with the following defects: after welding, there is the problem of too thin and too thick intermetallic compound: There are holes and tiny cracks inside the solder joint or at the interface; Small wetting area of solder joint (small lap size of component welding end and pad) : microstructure of solder joint is not dense, large crystalline particles and large internal stress. Some defects can be detected by visual, AOI, X-ray, such as small solder joint size, pores on the surface of the solder joint, obvious cracks, etc. However, the microscopic structure, internal stress, internal cavity and crack of solder joints, especially the thickness of intermetallic compounds, these hidden defects are invisible to the naked eye and cannot be detected by manual or automatic inspection of SMT processing, so it is necessary to adopt various reliability tests and analysis for detection. Such as temperature cycle, vibration test, drop test, high temperature storage test, humid heat test, electromigration (ECM) test, high accelerated life test and high accelerated stress screening; Then the electrical properties, mechanical properties (such as solder joint shear strength, tensile strength) test; Finally, we can make a judgment by examination, X-ray fluoroscopy, metallographic section, scanning electron microscope and other tests and analysis.
It can also be seen from the above analysis that hidden defects add an uncertain factor to the long-term reliability of lead-free products. As a result, high-reliability products are currently exempt; Both visible and hidden defects are due to lead-free high tin, high temperature, small process window, poor wettability, material compatibility problems, and design, process, management and other factors.
Therefore, we must start from the design of PCBA lead-free products to consider the compatibility between lead-free materials, lead-free and design, lead-free and process compatibility; Give full consideration to heat dissipation; Carefully select PCB board, pad surface layer, components, solder paste and flux, etc. SMT process optimization and process control more carefully than with lead welding; More strict and meticulous material management.