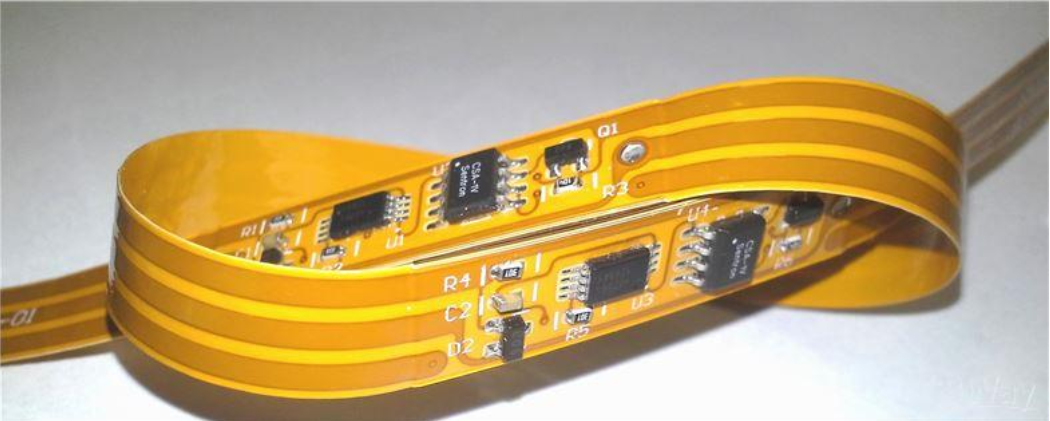
Flexible PCB (also known globally as flex circuit, flexible printed circuit board, flex print, flex circuit) is a member of the electronics and interconnect family. They consist of a thin insulating polymer film to which a conductive circuit pattern is fixed, and is usually provided with a thin polymer coating to protect the conductor circuit. The technology has been used in one form or another to interconnect electronic devices since the 1950s. It is now one of the most important interconnect technologies used to manufacture many of today's most advanced electronic products.
Similarities and Differences between Rigid PCB and Flexible Circuit
When designing a rigid PCB, certain design rules must be followed, including minimum hole size, minimum space and trace width, minimum distance to board edge, copper, and overall design thickness. Additionally, many manufacturing process steps are shared between rigid and flexible PCBs. These process steps include drilling and plating of holes and vias, optical imaging and development, etching of copper traces, pads, contours and planes, and heating (baking) of the circuit board to remove moisture from the PCB. At this point in the manufacturing process, the rigid PCB leads to the solder mask station, while the flex circuit connects to the overlay station.
Standards for IPC and Rigid and Flexible PCBs
The following list of IPC standards applies to rigid PCBs and flex circuits. Note that this list is not exhaustive and other IPC standards may need to be considered.
IPC-2221A, Generic Standard for Printed Circuit Board Design
IPC-2223, Standard for Segmented Design of flexible printed circuit boards
IPC-4101, Specification for Rigid and multilayer printed circuit board Substrates
IPC-4202, Flexible Base Dielectrics for Flexible printed circuits
IPC-4203, Adhesive Coated Dielectric Films for Use as Covers for Flexible Printed Circuits and Flexible Adhesive Bonding Films
IPC-4204, Flexible Metal-Clad Dielectrics for Fabrication of Flexible Printed Circuits
IPC-6013, Qualification and Performance Specification for Flexible Printed Circuits
Benefits of reduced size and weight for flexible circuits
Typically, flex circuits are the preferred solution for manufacturers who need:
· Suitable for wiring solutions that rigid boards cannot.
· Thin and light product, but still durable.
· Miniaturized versions of existing technologies.
· 3D packaging geometry.
· A small number of devices are interconnected.
· Shock and vibration resistance.
These advantages demonstrate that flexible circuit options are ideal solutions for mobile consumer electronics. Enterprising circuit board hobbyists splitting their smart phones or laptops will find an abundance of flexible circuits in any modern device on the market.
In the case of mobile devices, the use of rigid circuits results in devices that are too large, too heavy, and too fragile to be carried around easily. Such was the case with the Osborne I, the first full-power mobile computer, which weighed in at a staggering 24.5 pounds.
However, the size and weight reduction represents only half of the flex circuit story. They are also ideal for high temperature and high density applications.
High temperature and high density applications
In many cases, flex circuits are made of polyimide or similar polymers. This material dissipates heat better than most circuit board materials. For this reason, flex circuits can be placed in inconvenient locations where heat can affect the performance of rigid circuit boards.
flexible PCB can be designed to withstand extreme temperatures - between -200°C and 400°C - which explains why they are ideal for borehole measurements in the oil and gas industry.
In fact, due to these conditions and the need for small, unobtrusive devices in most industrial environments, flex circuits represent the engineering design of choice in most industrial sensor technologies.
High temperature resistance generally has good chemical resistance and excellent radiation and UV resistance. Combined with the ability to control impedance in high-density circuit board designs, flexible circuit designs offer manufacturers many benefits.
Why not make all boards flexible?
flexible PCB are certainly useful, but they will not replace rigid circuit boards for all applications. Cost efficiency is a major barrier to implementing dedicated Flexible circuit board designs in consumer products. Rigid circuit boards are less expensive to manufacture and install in typical automated high-volume manufacturing equipment.
Shenzhen Minghua Avionics SMT patch processing: Usually, the ideal solution for innovative products is to use flexible circuits when necessary, and use rigid, reliable rigid circuit boards to reduce manufacturing and assembly costs as much as possible.
Some manufacturers even explicitly use hybrid rigid-flex printed circuit boards for this purpose. This is common in laptop computers and medical equipment, where rigid circuit boards can be connected to each other using ribbon flex circuits. By focusing on the individual strengths of each board's underlying technology, these boards can be compounded and designed to meet any number of engineering needs.