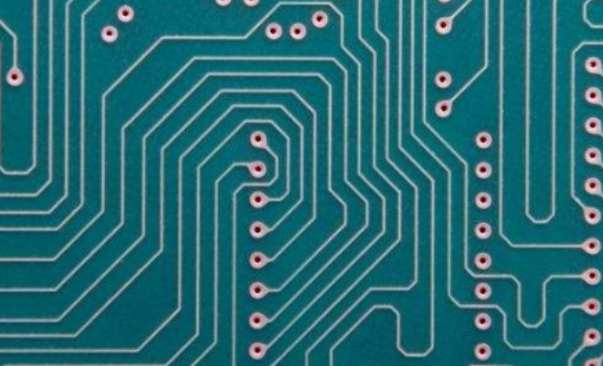
"Princetron Circuit" small edition will introduce the small knowledge about PCB for you. For example, whether different colors of PCB have an impact on its performance, and whether there is a difference between gold plating and silver plating on PCB, the following will explain one by one.
Colorful who noble PCB color revealed
Many DIY players will find a bewildering array of PCB colours available in the market for a wide variety of board products. More common PCB colors are black, green, blue, yellow, purple, red, and brown. Some manufacturers have also developed different colors of white, pink PCB.
In the traditional impression, black PCB seems to be positioned at the high end, and red, yellow and so on are low-end dedicated, that is not the case?
PCB copper coating without solder resistance paint is easily oxidized when exposed to air
We know that both sides of PCB are copper layer. In the production of PCB, no matter the copper layer is manufactured by addition method or subtraction method, it will finally get a smooth and unprotected surface. Although the chemical properties of copper are not as active as aluminum, iron, magnesium, etc., but in the condition of water, pure copper and oxygen contact is easy to be oxidized; Because of the presence of oxygen and water vapor in the air, the surface of pure copper will oxidize quickly upon contact with the air. Due to the thin thickness of the copper layer in PCB, the oxidized copper will become a bad conductor of electricity, which will greatly damage the electrical performance of the entire PCB.
To prevent copper oxidation, to separate the welded and unwelded parts of the PCB during welding, and to protect the PCB's surface, engineers invented a special coating. The coating can be easily applied to the PCB surface, forming a protective layer with a certain thickness and blocking the contact between copper and air. This coating is called a solder resistance layer, and the material used is solder resistance paint.
If it's called lacquer, there must be different colors. Yes, the original solder resistance paint can be made colorless and transparent, but PCBS often need small text printed on the board for easy maintenance and manufacturing. Transparent solder resistance paint can only reveal the PCB background color, so whether manufacturing, maintenance or sales, the appearance is not good enough. So engineers add a variety of colors to the solder resistance paint, resulting in black or red or blue PCBS.
It is difficult to see the wiring of black PCB, which brings difficulties for maintenance
From this point of view, the color of the PCB has nothing to do with the quality of the PCB. The difference between black PCB and blue PCB, yellow PCB and other colors of PCB is the final brush on the solder resistance paint color. If the PCB design and manufacturing process is exactly the same, the color will not have any effect on performance, nor will it have any effect on heat dissipation.
As for the black PCB, its surface line is almost completely covered, which causes great difficulties for the later maintenance, so it is not very convenient to manufacture and use a color. Therefore, in recent years, people gradually reform, give up the use of black welding resistance paint, and turn to use dark green, dark brown, dark blue welding resistance paint, the purpose is to facilitate manufacturing and maintenance.
At this point, we have basically understood the problem of PCB color. The reason for the emergence of "color represents high or low", that is because manufacturers like to use black PCB to make high-end products, red, blue, green, yellow and other low-end products resulted. To sum it up: the product gives the color meaning, not the color gives the product meaning.
What are the advantages of gold, silver and other precious metals used on PCB?
Now that the color is clear, let's talk about the precious metal on PCB! Some manufacturers in the promotion of their products, will specifically mention their products with gold plating, silver plating and other special processes. So what exactly is the use of this process?
PCB surface needs to be welded components, requires a part of the copper layer exposed for welding. These exposed layers of copper are called pads, which are usually rectangular or round and have a small area. In the above article, we know that the copper used in PCB is easily oxidized, so after the solder resistance paint is applied, the only thing exposed to air is the copper on the solder pad.
If the copper on the pad is oxidized, it is not only difficult to weld, but also increases the resistivity, seriously affecting the performance of the final product. So engineers came up with all sorts of ways to protect the pad. Such as plating the inert metal gold, or coating the surface with a layer of silver through a chemical process, or coating the copper layer with a special chemical film to prevent contact between the pad and the air.
Exposed pad on PCB, copper layer directly exposed. This part needs to be protected to prevent it from being oxidized
From this point of view, whether gold or silver, the purpose of the process itself is to prevent oxidation, protect the pad, so that it in the following welding process to ensure yield.
However, the use of different metals will require the storage time and storage conditions of PCB used in the production factory. Therefore, PCB manufacturers generally use vacuum plastic sealing machines to pack PCBS before they are manufactured and delivered to customers to ensure that no oxidative damage occurs to the maximum extent.
And before the final components on the machine welding, the board manufacturers also need to detect the oxidation degree of PCB, eliminate oxidized PCB, to ensure the yield. The board card that the final consumer gets has been tested. Even if the oxidation after a long time of use will almost only occur in the insertion and removal of the connection part, and there is no impact on the welding pad and the welded components.
Since silver and gold have lower resistance, will the use of special metals such as silver and gold reduce the calorific value of the PCB?
We know that the biggest factor affecting the amount of heat produced is resistance. Resistance is also related to the material of the conductor itself, the cross-sectional area and length of the conductor. The thickness of metal material on the surface of the pad is even far less than 0.01mm. If the pad is treated with OST(organic protective film), there will be no excess thickness at all. The resistance of such a small thickness is almost zero, which is incalculable, and of course does not affect the calorific value.