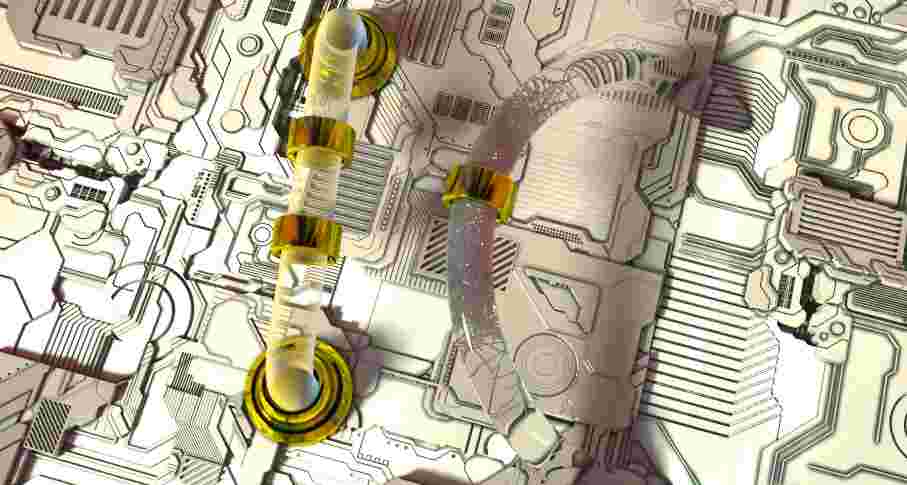
The rapid development of the electronics industry, the increasing demand for PCB (printed circuit board) manufacturing industry, including the rising board layer, the increasing tracking density and the thinning inner layer, all of which are leading to the increasing importance of lamination and lamination technology.
In order to prevent quality problems such as misalignment during layering, it is often required to fuse PCB manufacturing processes before layering in multilayer processes. Compared with the traditional fusion technology, the modern fusion technology has the advantages of high efficiency, easy operation and low cost, which makes it easy to manufacture multi-layer PCB. Based on the basic technology of fusion PCB manufacturing, this paper discusses the parameter factors that affect fusion effect and the application level of fusion technology, so as to provide a reliable reference for obtaining the best fusion parameters.
Principle fusion technique
As a traditional technology, rivet technology has been widely used in PCB board manufacturing. However, rivet technology also has some disadvantages, such as high cost of rivet, dislocation caused by PCB board deformation, easy damage of template, rivet shape indentation on the circuit board, etc., PCB board cost is high. Therefore, fusion technology has been used to replace rivet technology.
Introduction to PCB rivet technology
Depending on the melting characteristics of the epoxy prepreg, the melting technique allows the prepreg to melt at a certain temperature, thus converting the B-phase epoxy into C-phase epoxy, with the inner layer connected by a binder. Fusion is one of the most important processes in laminating process, and its performance directly determines the behavior of laminating. Key elements of convergence technologies include:
• Accuracy of positioning system
The type of positioning system is directly related to the alignment accuracy between the inner layers, which further affects the percentage of pass rate. A good positioning system should be stable, reliable and repeatable.
• Fusion point design
Fusion points are an essential problem because fusion techniques involve many shapes, such as squares, circles, and ovals. Fusion points should be consistent in terms of area, because fusion points with too small an area tend to cause fusion welds to be less strong, while fusion points with too large a area tend to cause image penetration, which can lead to loose connections between white points, inner layers or
• Flatness of equipment
Equipment flatness will affect PCB board Angle, force distribution and time balance during fusion. Non-uniformity will cause the board to deform, which will further cause misalignment between layers.
• Temperature and time control
During the implementation of fusion technology, temperature and time should be carefully controlled to avoid burning, white spots, de-soldering and aging. In addition, the laminated PCB board also plays an important role in determining the fusion effect.
Factors affecting Fusion PCB fusion performance
• Fuse and weld the joint
The different fuses and fuses are summarized in the table below for different types of fuses welded joints.
The shape of the fusion welded joint is between L1/2 and PP, between L3/4 and PP, and between L5/6 and PP
Circle6.194.515.995.62
5.814.826.07
6.065.385.77
Rectangle9.777.899.468.71
9.906.789.58
8.756.949.32
Based on the above table, because the area of the rectangular fusion welded joint is three times larger than that of the circular fusion welded joint, the bonding caused by the rectangular fusion welded joint is significantly larger than that caused by the circular fusion welded joint. However, the resin flow from rectangular fusion welded joints is much greater than that from circular fusion welded joints. When the resin flow is too large, part of the plate side may be higher than the plate, which may cause the plate side pressure. For small-size PCB products, the welding effect is insufficient due to the limited melting points that can be designed and the small area of the circular fusion welding joint. Therefore, rectangular fusion welding joints should be selected, and the fusion position should be carefully designed. As the plate moves inward, the defect of resin flow can be eliminated.
• Melting temperature
When the melting temperature reaches 300°C, the fusion extension area is large, and the polymerization effect is seriously affected. When the melting temperature reaches 270℃, the fusion expansion area is not uniform, and the risk of cracks is large, resulting in fusion effect. When the melting temperature reaches 285℃, the fusion expansion is uniform and there is no crack risk, resulting in the best fusion effect. Therefore, it can be concluded that 285°C is the optimal melting temperature for multilayer PCB manufacturing at the same melting time and layering.
• melting time
At equivalent melting temperature and cascade, different fusion times will affect the fusion expansion zone and fusion effect. When the melting time is 12 s, the fusion expansion area is not uniform, which has the risk of crack and bad fusion effect. When the fusion time is 18 seconds, the fusion expansion area is large and the fusion effect is poor. When the fusion time is 15 s, the fusion expansion is uniform with no crack risk and optimal fusion effect. Therefore, 15 seconds is the optimal fusion time for multilayer PCB fabrication at equivalent melting temperature and equivalent layer stacking. Too long or too short fusion time will bring bad fusion effect.
• Cascade
Equivalent fusion temperature and fusion time, different cascades determine the fusion region and fusion effect. At equivalent melting times and temperatures, when prepreg 2116 is applied, there is not even a crack in the fusion expansion zone, resulting in optimal fusion results. At equivalent melting time and temperature, when prepreg 7628 is applied, the fusion expansion zone even has cracks. This indicates that under the same melting time and melting temperature, the thinner the prepreg, the better the fusion effect will be produced. Therefore, it can be concluded that 2116 prepregs or lower layers are suitable for the realization of melting technology in the manufacturing process of multi-layer PCB.
According to the discussion in this paper, many factors affect the fusion effect: the shape of the fusion welded joint, melting temperature, fusion time and layering. The rectangular fusion welded joint has better welding effect than the circular fusion welded joint. When equivalent layers are superimposed and fused, the higher the fusion temperature, the larger the fusion expansion area. Too low melting temperature will lead to uneven fusion expansion area, there is a risk of cracks. The longer the fusion time, the larger the fusion expansion area. When the fusion time exceeds 15 s, the fusion expansion area will expand, resulting in undesirable fusion effect. The thinner the prepreg billet structure, the more uniform the melting expansion. Therefore, a prepreg of 2116 or lower is best for fusion.