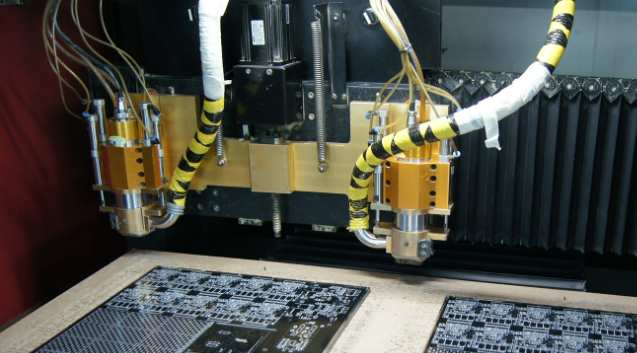
Abstract: This paper reviewed the field experience of milling cutter type circuit board splitter dust removal process for ten years, aiming at the problems of complex factory products (component density and cutting path complexity), high reliability and low cost of circuit board substrate requirements (by adding high hardness quartz, mica, alumina, etc.) caused by dust difficult to be completely removed in the splitter process. At the same time, due to the increasingly strict quality requirements of customers, some factories began to consider adding dust removal process after the board. At the same time, considering the increase of the cost of the plate separator due to the improvement of dust removal efficiency, sometimes the cost of dust removal after the board is lower, higher dust removal efficiency, that is, more cost-effective. There are also some products due to the particularity of the board process window is very narrow, in order to achieve high product quality factories have to use the board after the process to meet the requirements. Dr.Escherich's Taifun-Clean unit is a common modular cleaning system (pictured below), Its working principle is that the ordinary compressed air is ejected at high speed from the air nozzle through a unique structure and rotates at a speed of more than 600 revolutions per minute to generate a pulse of strong air flow to shake out the dust attached to the workpiece and be extracted and discharged by the attached vacuum system. The working principle of other cleaning systems is roughly the same or similar.
Key words: circuit board after dust cleaning system process scheme Automotive electronics
directory
1. Preface 1
Ii. Analysis of dust removal scheme after dividing plate 1
3. Key control point of dust removal in the process after dividing plate
4. Field management measures to improve process dust removal after plate splitting
5. Conclusion 7
I. Introduction
As more and more manufacturers join the automotive electronics industry, the competition is unprecedenedly fierce, so the product design pursuit of high reliability and low price, in the design of product shape, plate style, plate layer and plate and so on complex and diverse, so the difficulty of the board process is unprecedented. In order to improve the competitiveness of manufacturers must improve the quality of products, so the manufacturing process is put forward higher requirements. For products that have special requirements for the splitter process, such as Company B's ESX products with vibration sensors and metal lines in the cutting path, the company's splitter process is defined to use specific low-vibration milling cutters to reduce vibration and control the size of metal dust particles, thus the window for the splitter process is limited. In addition, the conservative design of non-pre-cut panels based on product quality and the XX175F substrate based on cost resulted in very bad dust residue. In order to pursue high quality, B company had to adopt the dust removal process after the panels.
Although the board process itself has the dust removal function, for the dust collecting machine, because the main shaft of the board is cut on the auxiliary surface of the circuit board (that is, contains the most simple, the least number of components), the dust removal system is also on this surface, so the dust on this side is basically no problem. However, the main side of the circuit board (that is, the side containing the most complex or the most number of components) is on the opposite side of the dust removal system, for relatively simple components of the product is OK, for relatively complex components of the product on this side of the dust problem is not ideal. For the next dust separator, although some factories for some products can use special fixture retaining wall to prevent dust flying into the main surface of the circuit board. However, with the pursuit of high integration and high utilization of circuit board components, components are getting closer and closer to the edge of the board, Recently up to about 1mm, taking into account the potential risk of collision (generally to maintain 1.5 to 3mm) and the reliability of the fixture retaining wall (retaining wall needs to ensure at least 1.5mm thickness), in fact, the element from the plate side to 3mm and above to use the fixture retaining wall, and meet the conditions of the product is limited, In particular, automotive electronic products with safety protection (generally based on products) are mostly inconsistent. In addition, the fixture after adding the retaining wall will have the risk of collision when placing the plate in front of the sub-plate and taking the plate after the sub-plate. The cleaning and maintenance of the fixture will also have many inconvenience, and the production cost of the fixture will be high.
At the same time, due to the characteristics of the product itself, the differences in the dust removal performance of the panel equipment itself, the differences in the understanding of the technical personnel of the panel process dust removal and the poor maintenance and management of the panel equipment, the dust residue of the final product is not ideal. Because the sub-board equipment is the main equipment, the investment is relatively high and generally will not have rich configuration (foreign mainstream equipment such as European sub-board machine, semi-automatic to nearly 800 thousand yuan, the price of automatic up to 2 million yuan), the second sub-board dust removal will cause the use of equipment efficiency seriously decreased (affecting about 50% efficiency), And there will be equipment cutting "belt plate" (or called "suction plate") and other quality problems. Especially for automotive electronics, which require high stability of the product, heavy industry is not allowed, so the board after the dust removal process has become a very practical choice