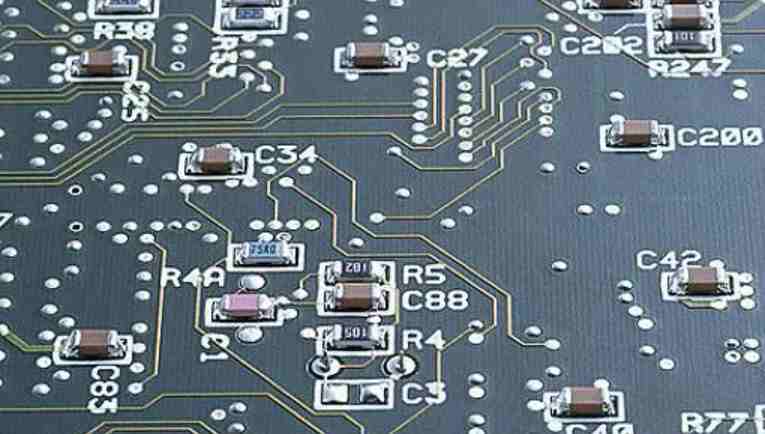
Green oil refers to the PCB coated in copper foil above the ink, this layer of ink can cover in addition to the welding plate and other accidental conductors, can avoid welding short circuit in the process of use, prolong the service life of PCB and other functions; Generally called welding resistance or welding resistance;
Colors come in green, black, red, blue, yellow, white, matte colors, etc. Most PCBS use green solder resistance ink, also known as green oil.
Characteristics and differences of PCB board green oil and blue oil:
I. Price: At present, the price of domestic blue oil per square meter of PCB is about 20 yuan higher than that of green oil, and the imported blue oil (daily production) is about 100 yuan higher than that of green oil. According to our current DVD player, the cost of domestic oil per DVD increases by about 5 cents to 15 cents. P-DVD and RW-DVD stand-alone costs about 1 -3 cents per unit.
Two, manufacturer procurement (supply) two kinds of ink procurement is no problem, you can switch at any time. Can meet the environmental requirements.
Three, characteristics:
1. Blue oil color is novel, appears high-grade;
2. Lack of blue oil hardness, easy to wipe flowers, PCB manufacturers will increase the defective products.
3. Blue oil fluidity, easy to accumulate oil, uneven oil. In production, PCB should be placed horizontally rather than vertically, which takes up more space.
4. Blue oil is difficult to plug holes, easy to flow out after plugging holes.
5. Blue oil baking board for a long time, easy to dirty, easy to stick film after packaging.
6. Easy to discolor after SMT, and flux influence
7. Color difference in mass production (different batch colors vary greatly)
8. The above are domestic blue oil and green oil comparison, daily blue oil will be much better, but the price increases more.
9. Single panel material is poor, the problem is more obvious, if the single panel does not switch will cause a machine with blue and green.
2,Compression study
Pressing is very important to deformation, and the stress can be effectively reduced by reasonable parameter setting, press selection and laminating mode. For the general symmetrical structure of the plate, it is generally necessary to pay attention to the symmetric laminated plate when pressing, and symmetrical placement of tool plates, buffer materials and other auxiliary tools. At the same time, the combination of cold and hot press is also significantly helpful to reduce the thermal stress. The reason is that the cold and hot separate press transfers the sheet parts to the cold press at high temperature (GT temperature above), and the loss of pressure and rapid cooling of the material above the Tg point will lead to rapid release of thermal stress and deformation, while the cold and hot integrated press can realize the cooling at the end of hot pressing and avoid the loss of pressure of the sheet parts at high temperature.
At the same time, for the special needs of customers, it is inevitable that there will be some plates with asymmetric materials or structures. At this time, the deformation caused by different Ctes analyzed above will be very obvious. To solve this problem, we can try to use asymmetric laminated plates. Thus, the growth and shrinkage of different CTE core cypress trees in the heating and cooling stages are affected to solve the problem of inconsistent deformation. Table 4 shows the test results on a structurally asymmetric plate.
Through asymmetric stacking, plus a post-cure process after pressing, and leveling before shipping, the board finally met the customer's 2.0mm requirement.
3,Other production processes
In PCB production process, in addition to pressing, there are several high temperature treatment processes, such as welding resistance, characterization and hot air smoothing. Among them, the maximum temperature of the drying board after welding resistance and character is 150℃. As mentioned above, this temperature is above the Tg point of ordinary Tg material, which is in a high elastic state and easy to be deformed under external force. At the same time, when drying the plate, ensure that the direction of the plate is parallel to the direction of blowing. During hot air leveling, ensure that the plate is cooled in the tin discharging furnace for more than 30 seconds to avoid sudden cooling deformation caused by cold water washing after treatment at high temperature.
In addition to the production process, the storage of PCB board parts at each station also has a certain impact on the deformation. In some manufacturers, due to more production waiting and narrow site, multiple boards will be stacked together for storage, which will also lead to external deformation of the board parts. Since PCB board also has a certain plasticity, these deformation will not be 100% recovered in the later flattening process.
4,Flatten before shipping
Most PCB manufacturers will have a leveling process before shipment. This is because the deformation of the plate caused by heat or mechanical force is inevitable in the processing process, which can be effectively improved by mechanical leveling or hot drying leveling before shipment. Affected by the heat resistance of blocked welding and surface coating layer, the temperature of the drying plate is generally below 140℃~150℃, which is just above the Tg temperature of ordinary materials, which has great benefits for the leveling of ordinary plates, while the leveling effect of high Tg materials is not so obvious. Therefore, the temperature of the drying plate can be appropriately increased on some high Tg plates with serious warping. But to the main ink and coating quality. At the same time, pressing weight and increasing cooling time during the drying of the plate also have a certain improvement effect on the deformation. Table 5 shows the test results of the flattening effects of different pressing weight and furnace cooling time on the plate, from which it can be seen that increasing pressing weight and extending the furnace cooling time have obvious effects on the flattening of the deformation.