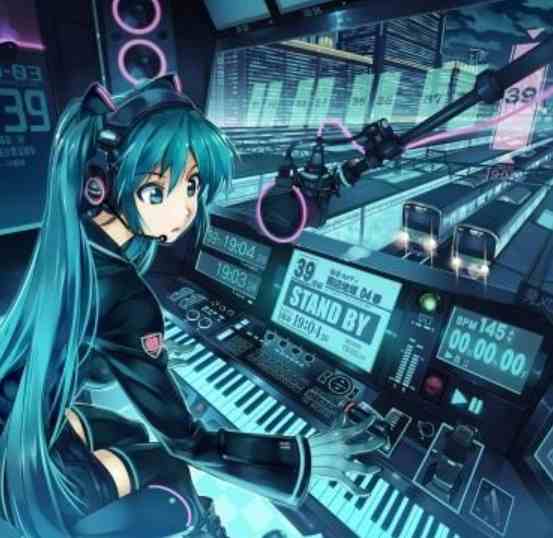
With the improvement of product performance, PCB is constantly updated and developed, the lines are more and more dense, more and more components need to be placed, but the size of PCB will not grow, but become smaller and smaller, so at this time to drill holes in the plate, it needs considerable technology.
Introduction to common PCB microporous technology
There are many kinds of PCB drilling technology, the traditional method, the production of inner blind holes, successive pressing multilayer board, first with two double panels with holes as the outer layer, and no holes in the inner plate pressed together, you can appear filled with glue blind holes, and the blind holes on the outer board surface to mechanical drilling holes. But in the production of machine-drilled blind holes, the drill depth is not easy to set, and the taper hole bottom affects the effect of copper plating, plus the production process of inner blind holes is too long, waste too much cost, the traditional method is more and more unsuitable.
Introduction to common PCB microporous technology
In addition to the carbon dioxide drilling and laser drilling we introduced before, there are also mechanical drilling, photosensitive drilling, laser drilling, electroplasma etching and chemical etching.
Mechanical drilling is made by high-speed machining, among which the most important is the drill bit. The drill bit is generally made of tungsten cobalt alloy, which is sintered by high temperature and high pressure with tungsten carbide powder as the matrix and cobalt as the binder. It has high hardness and high wear resistance, and can drill the required holes smoothly.
Introduction to common PCB microporous technology
Laser hole, is the use of carbon dioxide, ultraviolet laser cutting. The gas or light forms a beam, which has a powerful heat energy and can burn through the copper foil to make the required holes. The principle is the same as cutting, mainly controlling the beam.
Plasma, or plasma, is composed of widely spaced particles that are constantly colliding in random ways, and its thermal motion is similar to that of ordinary gases. Electroplasmic etching holes are mainly used for PCB of resin copper layer. Oxygen containing gas is used as electroplasma. After contacting with copper, oxidation reaction will be generated, and then the resin material will be removed to form holes.
As previously introduced, the objects remaining on PCB can not be cleaned off by general methods. Chemical cleaning method can be used to remove the chemical agents by reacting with the residues. Drilling is the same, the use of chemical agents, drop in the need to drill the place, you can corrosion copper foil, resin, and so on, and finally form holes.
The risk of not doing so
The chemical residue in the gold settling process can be left in the hole where the plug hole is not sufficient, causing problems such as weldability. Moreover, tin beads may be hidden in the hole, which may splash out during assembly or actual use, causing a short circuit.
9. NCAB specifies the solder shield thickness, although IPC does not specify it
Benefits: Improved electrical insulation, reduced risk of flaking or loss of adhesion, enhanced resistance to mechanical impact wherever it occurs!
The risk of not doing so
Thin solder resistance layer can lead to adhesion, flux resistance and hardness problems. All of these problems can cause the solder shield to detach from the circuit board and eventually lead to corrosion of the copper circuit. Poor insulation due to thin solder resistance layer can cause short circuit due to unexpected conduction/arc.
10. Appearance requirements and repair requirements are defined, although IPC does not
Benefits: In the manufacturing process of careful care and careful casting safety.
The risk of not doing so
Multiple scrapes, minor injuries, repairs, and repairs - boards work but don't look good. In addition to the visible problems, what are the hidden risks, the impact on assembly, and the risks in actual use?
11. Requirements for the depth of the plug hole
Benefits: High quality plugs will reduce the risk of failure during assembly.
12. PetersSD2955 specifies the brand and model of peelable blue glue
Benefits: The designation of peelable blue glue avoids the use of "local" or cheap brands.
The risk of not doing so
Poor quality or cheap peelable glue may bubble, melt, crack, or set like concrete during assembly, making the peelable glue unpeeled/ineffective.
13. NCAB implements specific approval and placing procedures for each purchase order
Benefit: This procedure is performed to ensure that all specifications have been confirmed.
The risk of not doing so
If product specifications are not carefully confirmed, the resulting deviations may not be discovered until assembly or the final product, when it is too late.
14. Sleeve plate with scrap unit is not accepted
Benefits: Not using partial assembly helps customers improve efficiency.
The risk of not doing so
Defective sheeting requires special assembly procedures. If the end-of-life unit board (x-out) is not clearly marked, or it is not isolated from the sheeting, the known defective board may be assembled, wasting parts and time.