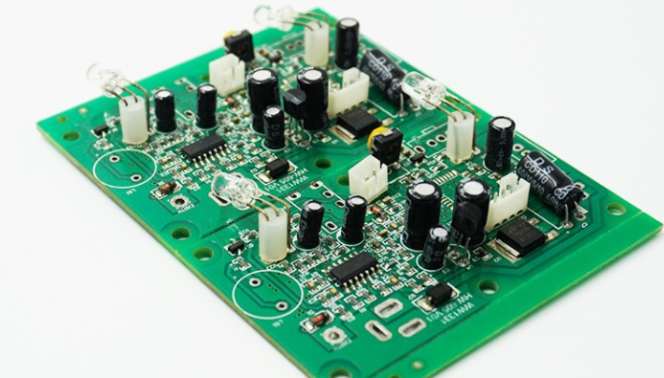
For the repair of Chip components, you can use ordinary anti-static electric soldering iron, or you can use a special clamp type soldering iron to heat both ends at the same time. Chip components are easiest to repair in SMT. Chip components are generally small, so when heating it, the temperature should be controlled properly, otherwise too high temperature will cause the components to be damaged by heat. The following is the SMT processing manufacturer's relevant knowledge about SMT processing component rerepair and OEM OEM service preparation.
1. What are SMT machining components to be repaired
Chip resistors, capacitors and inductors are commonly referred to as CHIP components in SMT. For the repair of Chip components, you can use ordinary anti-static electric soldering iron, or you can use a special clamp type soldering iron to heat both ends at the same time. Chip components are easiest to repair in SMT. Chip components are generally small, so when heating it, the temperature should be controlled properly, otherwise too high temperature will cause the components to be damaged by heat. Generally, the duration of the soldering iron on the pad shall not exceed 3 s when heating. The core of its technological process is: the diswelding and disassembling of chip components, the cleaning of pad and the assembly and welding of components.
1. Dewelding and disassembling of chip components
(1) If there is coating layer on the component, the coating layer should be removed first, and then the residue on the working surface should be removed. (2) Install the hot clip iron head with appropriate shape and size in the hot clip tool. (3) the temperature of the iron head is set at about 300 dragons, which can be changed appropriately according to needs. (4) The two solder joints of the chip element are coated with flux. (5) Remove oxides and residues on the tip of the iron with a wet sponge. (6) Place the soldering iron head above the chip element, and clamp both ends of the element and contact the solder joint. (7) Lift the element when the solder joints at both ends are completely melted. (8) Place the removed element in a heat-resistant container.
2. Clean pad
(1) The selection of chisel-shaped iron head, the temperature is set at about 300 dragons, can be made according to the need for appropriate changes. (2) Brush flux on the welding pad of the circuit board. (3) Remove oxides and residues on the tip of the soldering iron with a wet sponge. (4) Place the soft tin-absorbing braided tape with good solderability on the pad. (5) Gently press the soldering iron head on the tin absorbing braid belt. When the solder on the pad is melted, slowly move the soldering iron head and braid belt to remove the residual solder on the pad.
3. Assembly and welding of chip components
(1) Choose the right shape and size of the iron head. (2) The temperature of the soldering iron head is set at about 280 Y, which can be changed as required. (3) Brush the flux on the two pads of the circuit board. (4) Remove oxides and residues on the tip of the iron with a wet sponge. (5) Apply an appropriate amount of solder to a pad with an electric soldering iron. (6) Clamp the chip element with the insert, and connect one end of the element with the solder plate that has been tinned with an electric iron to fix the element. (7) Weld the other end of the component with the pad with the electric iron and the soldering wire. (8) Weld both ends of the components with the pad respectively. The above is shared by Shenzhen Baoan SMT processing factory kingford Electronics for SMT processing common components repair content, I hope to help you, learn more about SMT processing knowledge, welcome to visit kingford
2. What preparations should be made for OEM processing services
OEM service for electronic products is now a common production and processing method. In a nutshell, well-known brand operators do not immediately carry out the production and manufacturing of products, but only carry out the design scheme and product research and development with their own grasp of technology. Then I will look for an electronic processing plant, namely PCBA factory or SMT patch factory, to carry out the production, manufacturing and assembly of products. The manufacturer who orders such production and processing orders is an OEM manufacturer, and such products are OEM products. What must be prepared in advance for OEM production and processing of electronic devices? There are still a lot of differences, very simple is PCBA OEM production OEM, only have to show the production and processing documents, the rest of the thing is by PCBA OEM production OEM processing plant to deal with, then is waiting for the goods.
①BOM document has accurate BOM table and silk screen printing ink engineering drawings, can be printed, but it is better to show EXCEL and PDF documents. In this way, the actual operation staff of SMT patch production and processing can immediately guide the BOM into the mobile phone software when the program is written, which can save time and effort and improve the accuracy of the program process.
② Raw materials must be checked successively according to BOM and the total demand of raw materials. It is stipulated that raw materials for SMT operation should be mounted on plates. It is better to give 5% of the loss of resistance and volume, so that the end can be cleared more quickly and orders can be placed.
③ Steel mesh has 0.4PIH on the dense foot IC and goods with BGA, must open the laser steel mesh, its processing technology is excellent, SMT stage can reduce many poor elements. Other boards are capable of etching process steel mesh. For automatic printing equipment, the most basic steel mesh specifications are (340*470-550*650). It is better to send Gerber files or detailed PCB to open steel mesh one day before release and manufacture.
④ Determine the delivery date and production process: when the material work is handed over to the patch factory, negotiate the delivery date and the processing process with lead or without heavy metal. It is better to indicate it in the BOM.
⑤ Special processing needs SMT patch production and processing is a complex and delicate field, processing technology must be careful, careful, once a mistake is very easy to show large quantities.