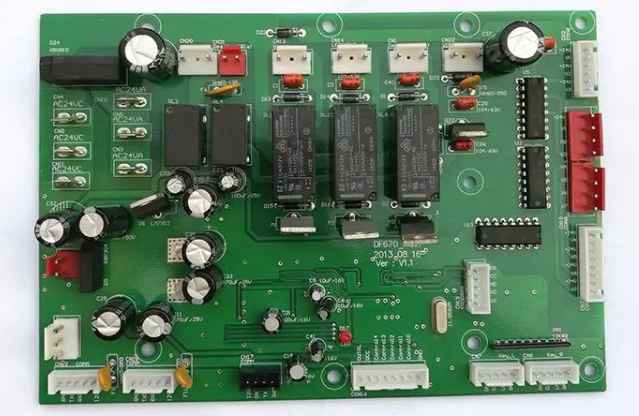
Solder joint as a direct result of welding, its quality and reliability determine the quality of electronic products. That is to say, the quality of assembly during the production process. The final performance is the quality of welding. So SMT patch processing how to reflect the solder joint quality? It is an important means to ensure product quality and production efficiency to ensure that equipment is always in good condition. The following patch processing manufacturers say how to reflect the quality of the patch processing and how to improve the product quality of the relevant knowledge.
1. How does PCBA improve product quality
(1) Strengthen the daily maintenance of the machine
SMT machine is a very complex, high technology, high precision machine, requires a constant temperature, humidity and very clean environment. Perform daily, weekly, monthly, semi-annual, and yearly maintenance according to the equipment requirements.
(2) Requirements for equipment operators
① Operators should receive certain SMT professional knowledge and technical training. ② Operate in strict accordance with the operation rules of the machine. Do not carry faulty devices. If the fault is found, stop the machine in time, and report to the technical responsible personnel or equipment maintenance personnel. (3) The operator should concentrate on eye, ear and hand work during the operation. One is to observe whether there are abnormal phenomena during the operation of the machine, such as no action of the tape winder, broken tape of the mold material, incorrect installation, etc. Listen to the abnormal sound during the operation of the machine, such as the abnormal sound of mounting head, throwing material, transmitter, scissors, etc. One by one, find abnormal phenomena and solve them promptly. Minor faults can solve their own mechanical and circuit problems, please maintenance personnel overhaul.
(3) Formulate measures to reduce or avoid errors. When SMT patches are installed, it is easy to paste wrong components and mount them in wrong positions. Therefore, the following measures are formulated to prevent them.
(1) After the programming of the feeder, there must be a special person to check whether the component value on each numbered position of the material station is consistent with the component value of the corresponding feeder number in the programming table. If not, it has to be positive. (2) Ribbon feeder, after pasting each plate and then filling. There must be a special person to check the correct value of the new plate. ③ The patch must be edited once after programming. Check the component number, rotation Angle and mounting position for each mounting step. ④ Each batch of products affixed after the first piece, there must be a special inspection. The problem should be corrected by modifying the procedure in time. ⑤ In the mounting process, often check the mounting position, throwing material and so on. SMT line technician found problems should be checked in time and eliminated. ⑥ Set up welding detection station (manual or through AOI) In a word, SMT SMT SMT machine mounting speed and mounting accuracy is certain, how to play the role of PCBA processing equipment, the human factor is very important. To formulate effective rules and regulations and management measures to ensure the normal operation of the machine, ensure the mounting quality and efficiency.
2. How to reflect the quality of patch processing
1, good wetting;
2. Complete, smooth and bright surface;
3, the appropriate amount of solder and solder completely cover the welding parts of the pad and lead (or welding end), the height of the component is moderate. In principle, these criteria are applicable to all types of solder joints produced by all welding methods in SMT patch processing. In addition, the edge of the welding point should be thinner. If the welding surface is large enough, the wetting Angle of the solder and the pad surface should be less than 300. No more than 600.
2. Failure form of solder joint within the life cycle Considering the relationship between failure and time, failure form is divided into three different periods:
1. In the early failure stage, a large number of welding joints with poor quality fail, and some welding joints are damaged due to improper process operation and loading and unloading. The process can be optimized to reduce the early failure rate.
2, stable failure rate stage, the quality of most of the solder joints in this stage is good, the failure rate (failure rate) is very low, and relatively stable.
3, the end of life, failure is mainly caused by the accumulation of broken factors, including chemical, metallurgical, thermal mechanical characteristics and other factors, such as the occurrence of metal reaction between solder and welded metal, or thermal mechanical stress caused by solder joint failure. The failure is mainly determined by the characteristics of the material, the specific structure of the solder joint and the load.
3. How to check short circuit of the patch
In the manual welding of SMT patches, short circuit is a common bad processing. If you want to achieve the same effect of manual SMT patches and machine stickers, short circuit is a problem that must be solved. Short-circuit PCBA can not be used, there are many ways to solve the short circuit in SMT patch processing, the following SMT patch processing to give you a brief introduction.
1, manual welding operation to form a good habit, with a multimeter to check whether the key circuit short circuit, each time after the manual SMT patch an IC need to use a multimeter to measure whether the power supply and ground short circuit.
2. Light the short-circuit network on the PCB drawing, look for the most tolerant place of short-circuiting on the circuit board, and pay attention to the IC internal short circuit.
3. If the same short circuit occurs in batches during SMT patch processing, you can take a board for sectioning operation, and then energize each part respectively to check the short circuit part
4. Use short-circuit positioning analyzer for inspection.
5, if there is a BGA chip, because all the solder joints are covered by the chip can not be seen, and it is a multilayer board (more than 4 layers), so in the design of the power supply of each chip is divided, with magnetic beads or 0 ohl resistance connection, so that when the power supply and ground short circuit, disconnect magnetic bead detection, it is easy to locate a chip.
6, small size SMT patch processing surface paste capacitor welding must be careful, especially power filter capacitor (103 or 104), the number is large, it is easy to cause short circuit between the power supply and the ground.
2. How to solve the porosity in reflow welding
Surface mounted packages are known to absorb moisture when exposed to humid environmental conditions during reel storage during plant or service. When a surface-mount component is installed on a PCB, the entire PCB board and component are exposed to rapid changes in ambient temperature (210°C to 250°C) in a typical solder reflux operation. Any absorbed water will quickly turn into superheated steam. This sudden change in steam pressure will cause the package to expand. If the pressure applied exceeds the flexural strength of the plastic molding compound, the packaging may break. Interface delamination can occur even if the packaging is not cracked. The most famous MSD failure mode is the violent cracking of the packaging, sometimes accompanied by an audible "popping" during reflux, which explains the commonly used name "popcorn". Despite a shared awareness of the condition, it is actually difficult to see and recognize this deficiency.
Cracks and characteristic bubbles in plastics are very small, difficult to see without proper lighting and magnification, they lie below the package and are obviously undetectable after reflow. These defects are usually not detected during normal assembly and testing and can lead to early life failure of finished electronics. The only effective way to detect such internal defects during assembly is with a tool called a scanning acoustic microscope. This is the reason IC vendors use to authenticate each new component they offer. How to avoid popcorn effect thermal damage or by strictly preventing moisture absorption during SMT can eliminate SMT component failures currently experienced by system manufacturers. By treating dry SMT magnetic components with a humidity control program, significantly higher yields can be achieved, reducing costly rework and providing a higher level of quality. Bake moisture sensitive equipment prior to assembly.