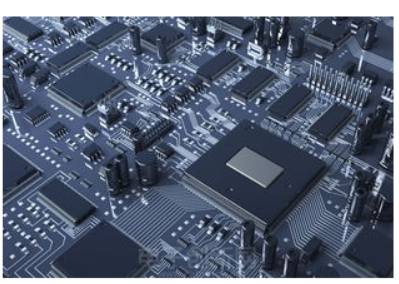
In the production process of PCBA processed aluminum substrate, tin wire is usually manually welded after the process in order to ensure its better application effect. So, PCBA processing aluminum substrate manual soldering wire should pay attention to what problems? Next, Shenzhen PCBA processing manufacturer -kingford for you to introduce.
PCBA processing aluminum substrate manual soldering wire precautions
First, pay attention to the welding temperature
Due to the particularity of aluminum substrate material, in order to ensure the welding effect, it is necessary to ensure the operation of the temperature level during welding, keep the welding temperature constant as far as possible, pay attention to the accuracy of welding, only in this way can ensure the very good application effect.
Two, choose the right raw materials
In the process of welding, it is particularly important to select suitable raw materials. Try to select some ultra-low temperature electrode, and its relative welding fluid, so that the welding effect will be better.
Three, it is harmful to apply force on spot welding with soldering iron head
The iron head transfers the heat to spot welding, the key is to improve the total contact area, with the electric iron on spot welding for heating is no effect, in many cases can lead to the damage of the welded parts. For example, the welding points of resistors, power switches and connectors are generally fixed on plastic prefabricated components, and the result of additional force is easy to lead to invalid components.
Although manual welding has been rarely used in the production and manufacturing of mass electronic equipment, manual welding is still unavoidable for the maintenance and adjustment of electronic equipment. At the same time, manual welding as a strong theoretical professional skills, welding quality will also damage the maintenance effect.
2. What problems should we pay attention to when selecting components for lead-free SMT processing?
Due to the influence of environmental protection factors, SMT patch processing is basically using lead-free process at present. What problems should we pay attention to when selecting components for SMT lead-free process?
SMT lead-free process selection components to consider factors
1. The heat resistance of components must be considered
Due to the high melting point of lead-free solder, one of the characteristics of the SMT lead-free welding process is the high welding temperature, which brings the heat resistance problem of components. Therefore, when evaluating component suppliers in PCBA lead-free process, it is not only necessary to evaluate whether toxic and harmful substances are used, but also to evaluate the heat resistance of components. Different components, their heat resistance mode is not the same, some impact resistance and high temperature resistance, some high temperature resistance and impact resistance; The temperature resistance curve of components is not equal to the welding temperature curve, a little uneven, may damage a component.
2, must consider the compatibility of solder and components surface coating material
In lead-free welding, the types of welding end coating materials of components are the most complex. Lead-free components welding end surface coating types of pure Sn, Ni-Au, Ni-Pd-Au, Sn-Ag-Cu, Sn-Cu, Sn-Bi alloy layer of different solder alloys; Their interface reaction speed is not the same, the resulting seam structure is not the same, the reliability is not the same. Due to the large variety of electronic components, the coating of component welding end is very complex, so there may be a mismatch between the welding end of some components and the solder, resulting in reliability problems.
kingford PCBA processingadvantage
1. Highly professional: The company focuses on processing samples and small and medium-sized batches, and promises to deliver the materials within 3-5 working days after confirmation.
2. Professional equipment: The company's equipment is tailored for sample and small and medium-sized batch production of advanced equipment, can stick 0201, BGA spacing 0.3MM, QFN, CSP, CON and other components.
3. Professional technology: 100% of technical backbone workers have more than 5 years of work experience, 85% of front-line operators have more than 3 years of work experience.
4. The company implements the 5S and 6σ concepts in daily operation, so as to ensure that the shipment is checked at least 7 times. If the quantity reaches 100PCS, our company promises to pass AOI optical inspection.
5. The company promises that the straight through rate of welding is more than 99%. If customers find welding defects, the company promises to repair them free of charge.