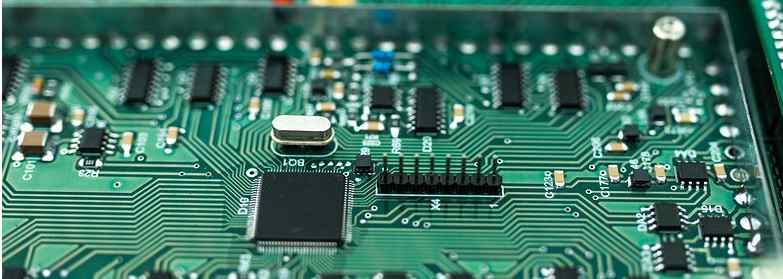
1.SMT patch refers to the short term of the process process on the basis of PCB. PCB(printed circuit board) means printed circuit board. SMT is a series of processes that are processed on the basis of PCB. PCB(PrintedCircuitBoard) SMT is Surface Mounted Technology (Surface Mounted Technology). It is the most popular technology and process in the electronic assembly industry at present. Surface Mount Technology (SMT) of electronic circuits is called surface mount or surface mount technology. It is a kind of pin-free or short-lead surface assembly components (SMC/SMD, Chinese known as chip components) installed on the Printed Circuit Board (PCB) surface or other substrate surface, through reflow welding or immersion welding and other methods to be welded and assembled circuit installation technology.
Under normal circumstances, the electronic products we use are designed by pcb plus various capacitors, resistors and other electronic components according to the designed circuit diagram, so all kinds of electrical appliances need a variety of smt SMT processing technology to process. SMT basic process elements: solder paste printing -> Parts mounting --> Reflow welding --> AOI Optical Detection --> Maintenance --> The board is divided. Due to the complex technological process of SMT patch processing, there are many factories for smt patch processing, and the quality of SMT patch is constantly improving. In the process of SMT patch, every link is very important, and there should be no mistakes. Today, I would like to learn the introduction and key processes of reflow welding machine in SMT patch processing. Reflow welding equipment is the key equipment in SMT assembly process. The solder joint quality of PCBA welding completely depends on the performance of reflow welding equipment and the setting of temperature curve. Reflow welding technology has experienced different forms of plate radiation heating, quartz infrared tube heating, infrared hot air heating, forced hot air heating, forced hot air heating with nitrogen protection and so on.
The increased requirements of the cooling process of reflow welding also promote the development of the cooling zone of reflow welding equipment. The cooling zone changes from natural cooling at room temperature and air cooling to water cooling system designed to adapt to lead-free welding. Reflux welding equipment due to the production process of temperature control accuracy, temperature uniformity in the temperature zone, transmission speed and other requirements. From the three temperature zone developed five temperature zone, six temperature zone, seven temperature zone, eight temperature zone, ten temperature zone and other different welding systems.
Key parameters of reflow welding equipment: 1. Number, length and width of temperature zone; 2. Symmetry of upper and lower heaters; 3. Uniformity of temperature distribution in the warm zone; 4. Independence of transmission speed control in temperature interval; 5, inert gas protection welding function; 6. Gradient control of temperature drop in cooling zone; 7. Maximum temperature of reflow welding heater; 8. Temperature control precision of reflow welding heater;
1. Welding temperature curve: The actual welding temperature at the solder joint is tested to set the temperature curve according to the PCB outline size, the number and thickness of multilayer plates, the volume and density of welded components, the area and thickness of copper layer on PCB board and other factors.
2. Control the preheating time, reflux time and cooling time: according to the length of the heater, the trajectory of the reflux curve is controlled by controlling the speed of the conveyor belt. The rolling gradient of the cooling zone is controlled by the cooling time and the cooling zone air volume.
3. The reflux temperature curve should overlap with the reference temperature curve provided by the solder paste supplier.
4. When SMT reflow welding is processed on both sides, it is generally necessary to weld one side of the low-quality component first. If there are large-quality components on both sides or the large-quality component surface must be mounted first in the process, during the second reflow welding, the large-quality components already welded at the bottom shall be protected to prevent the loss of large-quality components caused by the secondary reflow.
5, in the through hole reflow welding, attention should be paid to the device and transmission system jitter caused by component displacement.