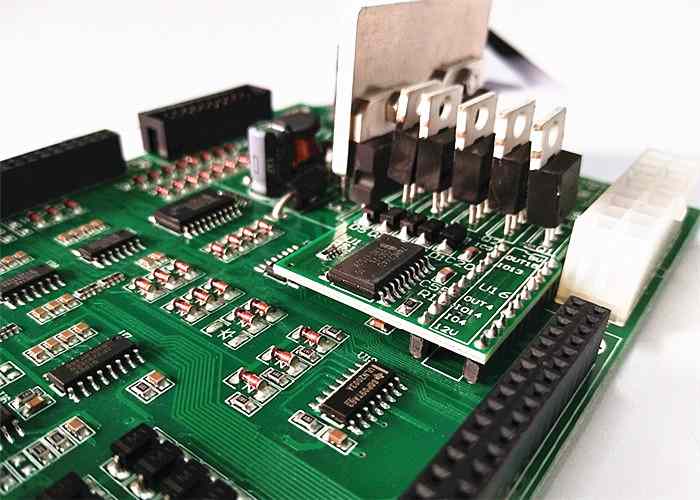
1. Open the material
Objective: According to the requirements of MI (engineering data of PCB circuit board), cut the PCB into small pieces on the large sheet material that meets the requirements to produce board parts. A small sheet in accordance with customer requirements.
Process: large plate → cut plate according to MI requirements → curium plate → beer rounded edge grinding → out plate
2. Drilling
Objective: According to the engineering data of circuit board, drill the desired aperture in the corresponding positions on the plates with the required size.
Process: Stack dowel → upper plate → drilling → lower plate → overhaul
3. Sinking copper
Objective: Copper deposition is the chemical deposition of a thin layer of copper on the wall of an insulating hole.
Process: rough grinding → hanging plate → semi-automatic copper wire → lower plate → Dip 100% dilute H2SO4→ thickening copper
4. Graphic transfer
Objective: Graphic transfer is to produce the image transfer on a printed board.
Process: (blue oil process) : grinding board → printing the first side → baking → printing the second side → baking → explosion → image impact → investigation; (dry film process) : hemp plate → film pressing → static → counterposition → exposure → static → image flushing → investigation
5. Graphic plating
Objective: Pattern plating is the plating of a copper layer of required thickness and a gold-nickel or tin layer of required thickness on the copper skin or hole wall exposed by the pattern of the line.
Process: upper plate → oil removal → water washing twice → micro-etching → water washing → pickling → copper plating → water washing → acid leaching → tin plating → water washing → lower plate
6. Remove the film
Objective: To expose the non-line copper layer by receding the anti-plating covering film with NaOH solution.
Process: water film: jack → alkali leaching → washing → washing → over the machine; Dry film: put plate → pass machine
7. Rot carving
Objective: Corrosion etching is the use of chemical reaction to remove the copper layer of non - line parts.
8. Green oil
Objective: The green oil is to transfer the green oil film graphics to the board, to try to take care of the line and block the tin on the line when burning welding parts.
Process: grinding plate → photosensitive green oil → curium plate → exposure → impact shadow; Grinding plate → printing the first side → drying plate → printing the second side → drying plate
9. Characters
Target: A character is a readily recognizable token provided.
Process: green oil curium finally curium cooling static → screen → printing characters → curium
10. Gold-plated fingers
Objective: To coat the finger of the plug with a layer of nickel gold of required thickness to make it more hard and wear resistant.
Process: upper plate → oil removal → water washing twice → micro-etching → water washing twice → pickling → copper plating → water washing → nickel plating → water washing → gold plating
Tin-spray plate
Objective: The tin spraying of multilayer circuit board is to spray a layer of lead tin on the exposed copper surface that is not covered by solder resistance oil, so as to protect the copper surface from corrosion and oxygenation, so as to ensure satisfactory welding performance.
Process: micro erosion → air drying → preheating → turpentine coating → solder coating → hot air leveling → air cooling → cleaning and air drying
11. Forming
Objective: Through the production of model stamping or digital control gong machine gong to the customer's needs of the pattern molding method organic gong, beer plate, small gong, hand cutting
Explain clearly: printed circuit board value gong machine board and beer board very high accuracy, small gong second, hand cutting board minimum can only do a little simple shape.
12. Testing
Objective: Energized flow through subtest fixture/fly pin test to verify and determine visually unobtainable open circuit, short circuit and other deficiencies affecting functionality.
Process: die → plate → test → conform to standard →FQC eye inspection → not suitable for standard → repair → return test →OK→REJ→ discard
13. Final inspection
Objective: To check the appearance of PCB board parts once again, and repair the minor defects to prevent the outflow of defective and defective board parts.
Specific office process: incoming materials → inspection data → visual inspection → in line with standards →FQA sampling → in line with standards → packaging → not suitable for standards → disposal → investigation.