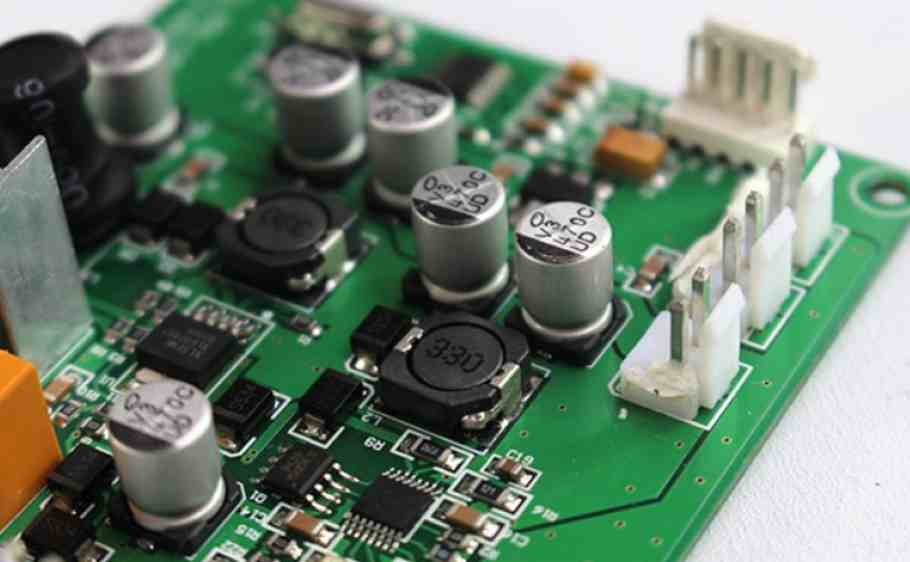
Printed circuit boards cannot be functionalized until electronic components are assembled on their surfaces. Failure analysis shows that the failure of printed circuit board is mainly attributed to the assembly process of electronic components. Therefore, the component assembly technology of printed circuit board plays an important role.
The assembly technology of printed circuit board includes the selection of assembly materials, assembly process design, assembly technology and assembly equipment. Any link seriously affects the final reliability of the printed circuit board. With the increasing interconnection density of PCB, the size of pad and the distance between sizes become smaller and smaller, which brings great challenges to the PCB Assembly technology. Although many new connection technologies have appeared in printed circuit boards in recent years, the assembly of electronic components is still dominated by high temperature connection of solder.
1 Assemble the solder
Solder is a key "bridge" material for the interconnection and assembly of printed circuit boards and components. For good reliability during the welding process, the solder is usually fusible metal. With the progress of technology, solder has been greatly developed, especially in the field of brazing micro-components, has become an indispensable assembly material.
After welding, the solder can not only form alloy on the surface of the welding plate metal, the connection spot welding together, and the melting point is lower than the base metal, easy to form alloy fusion with the base metal. The welding process of the printed circuit board requires not only enough mechanical connection, but also good electrical connection.
PCB assembly generally uses soft brazing, melting point below 450 degrees Celsius solder becomes "soft solder". This kind of solder is mainly composed of tin. In order to meet the requirements of brazing, adding different alloy components, such as lead, copper, silver, gold, zinc, cadmium, magnesium, boron, silicon and other elements, used to reduce or increase the melting point of solder. Among them, tin - lead solder is the most common welding material in PCB assembly technology.
1.1.1 Tin-lead solder
Printed circuit board pad surface such as nickel, copper, gold, platinum and their alloys can form alloy with tin, so as to obtain good mechanical connection and electrical connection. Therefore, tin is an indispensable material in PCB assembly technology. However, pure tin has some physical shortcomings, so pure tin can not be directly used as solder for PCB assembly. A certain amount of lead is added to the tin metal to form a tin-lead alloy, which can obtain excellent properties, such as:
(1) Reduce the melting point:
Low melting point alloys are good for welding
(2) Improve mechanical properties
(3) Reduce surface energy
Due to the existence of lead, the expansion area of the alloy can be multiplied and the surface energy of the alloy can be reduced.
(4) can enhance the antioxidant capacity of solder, reduce the amount of oxidation.
In the process of PCB assembly, the purity of tin-lead solder should be strictly controlled to avoid the introduction of harmful metals which lead to the deterioration of solder properties.
1.1.2 No oxidized solder
Solder components often contain oxides of tin and lead, which, like other non-metallic impurities, have been neglected in the past. In recent years, it has been found that the oxide residue is contained in the solder, forming many small grains with impurities as the center, which seriously affects the welding quality. Non-oxidized solder (tin-lead solder series) is a coarse pure alloy, which is very important for highly reliable solder in terms of ultra-miniaturization and miniature components. This kind of solder is produced by vacuum melting. This kind of solder is much more diffusible than air - melted Korean. Especially after vacuum melting of tin and lead.
1.1.3 Lead-free solder
With the increase of environmental awareness, the issue of banning the use of lead in the electronic assembly industry due to the inherent toxicity of lead metal has been proposed, and research on lead-free solder is imminent.
(1) Lead-free solder should have the performance
According to the requirements of environmental protection and industrial practical application, the following conditions must be met to find the Sn-Pb lead-free solder that can be fully replaced in the electronic assembly industry:
(1) The melting point of the low melting point material must be low enough to avoid thermal damage to electromechanical components, but must also meet the requirements of good mechanical properties under the existing assembly process.
(2) Wettability A good connection can be formed only when the solder has a good wettability with the base metal
(3) The price of the metal used in the solder needs to be considered in combination with the actual engineering, but also consider the additional cost of changing the assembly line due to the new solder.
2 flux (flux)
2.1 Action of flux
The purpose of welding is to use solder to combine two or more, or even thousands of separated components to form a conduction circuit. In order to ensure the reliability of this combination, it is required that the solder joint is free from virtual welding. From a metallurgical point of view, the connection requires the solder to form a metallurgical bond with the substrate at the solder joint, rather than a mechanical connection.
Flux has three functions in welding:
(1) Remove the oxide film
(2) At welding temperature, prevent the substrate and solder surface from being oxidized
(3) Reduce the surface energy of solder, increase its fluidity, conducive to substrate infiltration, create conditions for alloying.
2.2 Properties of flux
(1) The melting point is lower than the solder before the solder melts, the flux should melt, play a transitional role.
(2) Surface tension, viscosity, density should be less than solder solder surface tension is less than solder, before solder can infiltrate the substrate; If the viscosity is too large, its fluidity will be hindered; When the density is greater than the solder, it cannot surround the solder, nor can it prevent oxidation of the solder.
(3) The residue is easy to remove. Many fluxes are corrosive and may corrode the substrate if not removed in time. It is not easy to remove, which increases the cost.
(4) The film formed by flux should be bright, dense, non-moisture absorption and good thermal stability.
3 Solder paste
Solder paste is a kind of paste or paste developed for SMT surface mounting technology, which is composed of alloy solder powder and paste flux. It is a complex formed by alloy solder and flux. It is widely used in reflow welding and has good viscosity at room temperature. The electronic components are bonded to the design position by welding paste, and are interconnected with the printed circuit board as solvents and additives volatilize in the welding process.
3.1 Performance requirements of solder paste
In the SMT assembly process, the solder paste must have good retention, printing and reflux performance. The details are as follows:
(1) Performance before use:
Before use, the solder paste must have good preservation stability. Generally speaking, after the preparation of solder paste, it needs to be refrigerated or at room temperature for 3 to 6 months to maintain its properties.
(2) printing performance
1) Welding paste should have good demoulding performance when printing. The particle diameter, particle distribution and shape of alloy solder powder have great influence on the demoulding. Generally, the alloy solder powder is spherical powder with particle diameter less than one quarter of the mask opening size, especially when mounting fine devices.
2) The solder paste is not easy to collapse during and after printing
3) Appropriate viscosity using SMT assembly process to use the solder paste viscosity to temporarily fix electronic components on the surface of the printed circuit board, therefore, the solder paste is required to have good viscosity, and in a long time to mount reflow welding will not reduce its viscosity with time.
3.2 Properties during reflow heating
(1) Good wettability
The flux in the solder paste is different from the flux in wave soldering. It may not remove all the oxide film on the welded surface. Under the influence of heating curve, its wetting situation is more complex, so it is necessary to correctly choose the type of flux and metal content, in order to meet the wettability requirements.
(2) Reduce the formation of solder balls
(3) less solder spatter when reflow welding temperature rises sharply, the solder paste will appear almost boiling phenomenon, causing solder particles to splash, it is required to avoid the problem of too high residual solvent and too low boiling point after preheating.
Hot melt technology of 4 Tin - lead alloy coatings
4.1 Hot melting of Sn-Pb coating on printed circuit board
Low melting point tin - lead compound has good corrosion resistance and excellent weldability, and its melting point (183 degrees Celsius) is also relatively ideal, is widely used as solder. In double-sided printed circuit boards, it is also used as "resist" in the "graphic electroplating - etching process". The printed circuit board produced by this method has good weldability. In subsequent welding processes, the Sn-Pb coating is used as a solder that can be welded directly with the leads of various electronic components or with SMDS (surface mounted devices) in the SMT process.
As a result of the "graphic electroplating - etching method" manufactured printed circuit board, the circuit graphic outside the tin lead alloy coating for sheet and granular, mostly porous structure, the appearance of dark gray in the process and after the welding process, easy oxidation discoloration, thus affecting its weldability
Heat treatment is required. It is heated to a temperature above the melting point of the tin lead alloy coating to remelt the alloy of this coating and promote the alloying of the molten alloy with the base material. At the same time, the coating becomes dense, bright, no pinhole structure. This process is often called hot melting.