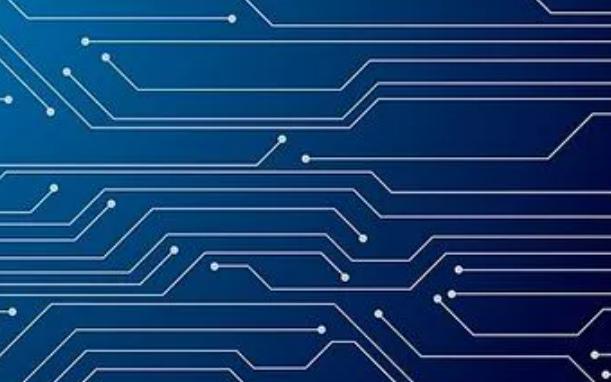
The ring resonator method is another method used for millimeter wave characterization. Although ring resonators are usually used below 10 GHz, with appropriate machining accuracy, it can also be used effectively at millimeter-wave frequencies. Machining accuracy is important because the effect of circuit size and dimensional tolerance is more pronounced at millimeter waves, and any variation will reduce accuracy. Most millimeter-wave ring resonators are thin (typically 5mil), and the gap between the feeder and the resonator ring is small. The thickness of the ring resonator, the copper plating thickness of the line, the change of the gap size will affect it, thus affecting the resonant frequency.
When comparing two circuits using the same circuit board material but with different copper-plated thicknesses, the circuit with thicker copper shows a lower Dk. Similarly, the resonant frequencies of the two circuits will be different, even though they use the same circuit board materials and test methods. Figure 7 is an example of this, where changes in the thickness of the final electroplated surface of the circuit lead to differences in the Dk calculated for the same material. The effect is similar whether the finish is chemically plated (ENIG) or other coated surfaces.
In addition to these machining problems, conductor width changes, etching coupling gap changes, trapezoidal effect and substrate thickness changes can also have similar effects. If all these variations are taken into account when testing the Dk with a ring resonator, a single ring resonator measurement can yield the correct Dk value. However, many tests tend to use nominal circuit sizes to test the calculated Dk, so it is not always correct. And at lower frequencies, these effects don't affect Dk accuracy as much as millimeter wave frequencies.
Another important variable for using ring resonators in the millimeter wave band is that the coupling gap varies with frequency. Normally, ring resonators are evaluated with multiple different resonators, and the coupling gap usually has significant frequency differences depending on the different resonators. Therefore, the change of coupling gap may be an important source of error. To overcome this problem, the differential circle method can be used. The two ring resonators used in this method are basically the same except for the circumference, and are integral multiples of each other. For two ring resonators, the higher order resonators have the same resonant frequency in Dk test. Since the feeders and clearances are the same, the effect of coupling clearances is lessened - theoretically eliminated - which makes the measured Dk more accurate. The formula for calculating Dk is as follows:
The ring resonator is a microstrip structure, and the feeders are tightly coupled GCPW to avoid the open end of the feeder resonance and avoid interfering with the resonance peak of the ring resonator. Usually if the feeders are open circuit, they will have their own resonance. The only way to avoid this is to make the feeders shorter or use tightly coupled GCPW feeders. Since the direct result of the differential circumferential ring resonator method is still the valid Dk of the circuit, it is still necessary to make accurate circuit size measurements and use the field solver to obtain the material Dk.
conclusion
The millimeter wave testing methods discussed here are all based on circuits. There are many other testing methods, such as raw material based testing methods. But most methods test the x-y plane of the material Dk rather than the Z-axis (thickness) Dk. Circuit designers more often use the Z-axis Dk, but for some applications requiring the use of material x-y plane Dk values, the free space test method, separated cylindrical resonator test method and waveguide perturbation test method are all x-y plane test methods.
It is also proposed to use the clamp wide-edge coupled strip-line resonator test method to determine the circuit board material Dk at millimeter wave frequency. However, this method is only most effective for a small range of materials under test (MUT), and is not suitable for a large number of tests. Therefore, testing methods for raw materials that can be used in millimeter-wave frequencies are continuing.
How to solve signal reflection in high speed PCB board design
In a high speed PCB, wiring is more than just connecting two points. As a qualified engineer, wiring is a hybrid knowledge carrier including resistance, capacitance and inductance. The signal line will have reflection in the transmission process. It must be understood that the reflection of the load end depends on the Z of the transmission line and the Z of the load.
The reflected size of the signal is measured by the reflection coefficient KR. The reflection coefficient of the load side is KRL=(ZL -- Z0)/(ZL+Z0). For open-circuit load, KRL=1; For short-circuited loads, KRL=-1 is visible, and for open and short-circuited loads, the signal is 100% reflected back. A negative KRL indicates that the reflected signal is in the opposite direction from the original signal. Similarly, the magnitude of the signal reflection at the source is expressed by the reflection coefficient at the source: KRS=(ZS -- Z0)/(ZS+Z0).
If the standard output level of the driver is 0.2V and the current is 24mA, its output impedance ZS is about 8.3Ω. If the input impedance ZL of the load is greater than 100KΩ and much larger than Z0 (about 67Ω), the reflection coefficient of the load end is KRL=1, and the signal is 100% reflected at the load end. The source reflection coefficient is KRS=-0.78. Bioneng belongs to Qinji Group, is the leading electronic industry service platform in China, providing online components, sensor procurement, PCB customization, BOM, material selection and other electronic industry supply chain solutions, one-stop to meet the comprehensive needs of small and medium-sized customers in the electronics industry.
The following is a detailed analysis of the driver generated from a 3.5V to 0.2V signal reflection process.
The first reflection: the driver voltage is 3.3V. According to the voltage division principle composed of ZS and Z0, the signal generated on Z0 is △V=-2.94V, and the signal voltage at the source end is VS=O.56V. The reflection coefficient at the load end is 1. When the signal reaches the load, VL=3.5-2.94-2.94=-2.38V.
The second reflection: the signal at the source end starts at 0.56V, and the second reflection occurs when the -2.94V signal reaches the source end. The reflected voltage is: VR=KPS*△V =-0.78*(-2.94)=2.29V. So the source voltage becomes VS=0.56+ (-2.94) +2.29=-0.09V.
Third reflection: When the second reflection signal reaches the load terminal, the load terminal voltage changes to VL =-2.38+2.29+2.29=2.2.V
On such impedance mismatched transmission lines, the signal bounces back and forth in this way, decreasing in amplitude with each reflection until it finally disappears. The vertical lines on the left and right represent the voltage at the source and the load, respectively, while the diagonal lines indicate the voltage of the transmitted and reflected signals. It can also be used to represent the specific reflection process of the signal, with one representing the source side signal and one representing the load side signal. It can be seen that after 5 cycles, the signal transmitted to the load end drops below the input threshold value, and the transmission delay is generally between 6 -- 16ns/m. If the transmission delay tPD=10ns/m, then the delay through a 0.15m transmission line is about 1.5ns. Then the signal can be considered valid after about 13.5ns has been transmitted.