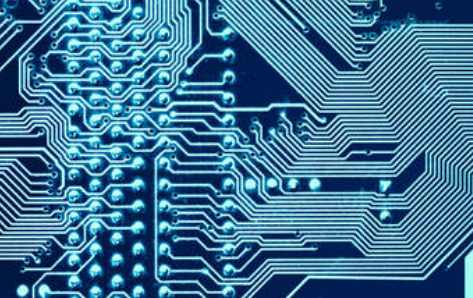
Due to the formation of a large number of monovalent copper ions during the etching reaction, and because the monovalent copper ions are always tightly bound to the complex group of ammonia, it is very difficult to maintain its content close to zero. Copper can be removed by converting it into bivalent copper through the action of atmospheric oxygen. The above purpose can be achieved by spraying.
This is a functional reason to vent air into the etching box. However, if there is too much air, the ammonia loss in the solution will be accelerated and the PH value will drop, which will still reduce the etching rate. Ammonia is also a controlled variation in solution. Some users use the practice of running pure ammonia into the etched liquid storage tank. To do so, a PH meter control system must be added. When the PH value is below a given value, the solution is automatically added.
In the related field of chemical etching (also known as photochemical etching or PCH), the research work has begun and reached the stage of structural design of etching machine. In this method, the solution used is copper divalent, not ammonia-copper etching. It will probably be used in the printed circuit industry. In the PCH industry, the typical thickness of etched copper foil is 5 to 10 mils, and in some cases the thickness is considerable. The etching parameters are often more demanding than those in the PCB industry.
One study from PCM Industrial Systems has yet to be published, but the results will be refreshing. With strong project funding, the researchers were able to make long-term changes in the design of etching devices and study the effects of these changes. For example, the best nozzles are fan-shaped compared to conical nozzles, and the nozzle chamber (the section of pipe into which the nozzle is twisted) has an Angle that provides a 30-degree injection of work entering the etching chamber. If this change is not made, the way the nozzles on the collector cavity are installed will result in the Angle of injection from each adjacent nozzle not being identical.
The spray surface of the second group of nozzles is slightly different from that of the first group. This makes the ejected solution shape superimposed or crossed. Theoretically, if the shapes of the solution cross each other, then the spray force of that part will be reduced and will not be able to effectively wash away the old solution from the etched surface while keeping the new solution in contact with it. This is especially true at the edges of the spray surface. The jet force is much less than in the vertical direction.
The study found that the latest design parameter was 65 pounds per square inch (4+Bar). There is a question of optimal injection pressure for each etching process and for each practical solution, and currently there are very few cases in which injection pressure exceeds 30 lb/sq inch (2Bar) in the etching chamber. There is a principle that the higher the density of an etching solution (i.e., specific gravity or permetropy), the higher the optimal injection pressure should be. It's not a single parameter, of course. Another important parameter is the relative mobility (or mobility) that controls the reactivity rate in the solution.
Four. On the upper and lower panel surface, the leading edge and the back edge etching state is different
A large number of problems related to etching quality focus on the etched part of the upper plate surface. It is important to know this. These problems arise from the effect of colloids produced by etching agents on the top surfaces of printed circuit boards. The accumulation of colloidal plates on the copper surface affects the injection force on the one hand, and prevents the replenishment of fresh etching fluid on the other hand, resulting in the reduction of etching speed. It is because of the formation and accumulation of colloidal plates that the etching degree of the top and bottom of the board is different. This also makes the first part of the board in the etching machine easy to etch thoroughly or easy to cause corrosion, because at that time the accumulation has not been formed, etching speed is faster. Conversely, the post-entry portion of the board enters when accumulation has formed and slows its etching rate.
V. Maintenance of etching equipment
The most critical factor in the maintenance of etching equipment is to ensure that the nozzle is clean, free of obstruction and smooth injection. Blocking or slagging will impact the plate under jet pressure. If the nozzle is not clean, it will cause uneven etching and scrap the whole PCB. Obviously, the maintenance of the equipment is to replace the damaged parts and worn parts, including the replacement of the nozzle, the nozzle also has the problem of wear. In addition, the more critical problem is to keep the etching machine without slagging, in many cases there will be slagging accumulation. Excessive accumulation of slagging will even affect the chemical balance of etching solution. Similarly, if there is excessive chemical imbalance in the etching solution, slagging will become more serious. The problem of slagging build-up cannot be overemphasized. The sudden appearance of a large amount of slagging in the etching solution is usually a signal that there is a problem in the balance of the solution. This should be properly cleaned or supplemented with a stronger hydrochloric acid.
Residual film can also produce slagging, a very small amount of residual film dissolved in the etching solution, and then form a copper salt precipitate. The formation of residual film slagging indicates that the previous film removal process is not thorough. Poor film removal is often the result of the combination of edge film and electroplating.