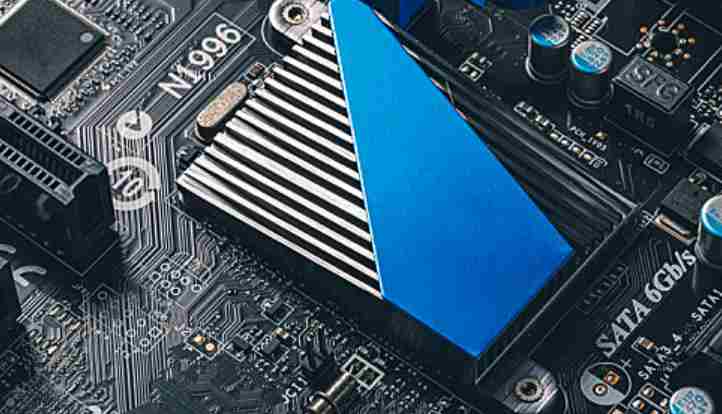
Viscosity and surface tension are important properties of solder. Good solder should have low viscosity and surface tension when melting. Surface tension is the nature of matter, can not be eliminated, but can be changed.
The main measures to reduce the surface tension and viscosity in PCBA welding are as follows.
① Raise the temperature. Increasing the temperature can increase the molecular distance in the molten solder and reduce the attraction of the molecules in the liquid solder to the surface molecules. So heating can reduce viscosity and surface tension.
② Adjust the proportion of metal alloys. The surface tension of Sn is very high, and the addition of Pb can reduce the surface tension. When the content of lead is increased in Sn-Pb solder, the surface tension decreases obviously when the content of Pb reaches 37%.
③ Add active agent. This can effectively reduce the solder surface tension, also can remove the solder surface oxide layer.
(4) Improve the welding environment. Nitrogen protected pcba welding or vacuum welding can reduce high temperature oxidation and improve wettability.
What is the role of surface tension in PCBA welding, and how to reduce the surface tension and viscosity
The role of surface tension in welding:
Surface tension is in the opposite direction of wetting force, so surface tension is one of the factors unfavorable to wetting.
Whether reflow welding, wave welding or hand welding, surface tension is a disadvantage to forming a good solder joint. However, surface tension can also be utilized in SMT patch processing and reflow welding -- when the solder paste reaches the melting temperature, Self Alignment effect occurs under the action of balanced surface tension. In other words, when the component placement position deviates slightly, the component can be automatically pulled back to the approximate target position under the action of surface tension. Therefore, the surface tension makes the reflow process more relaxed in the mounting accuracy requirements, it is easier to achieve a high degree of automation and high speed.
Meanwhile, due to the characteristics of "re-flow" and "self-positioning effect", SMT re-flow welding process has stricter requirements for pad design, component standardization and other aspects. If the surface tension is not balanced, even if the mounting position is very accurate, there will be component position deviation, monument, bridge and other welding defects after welding.
Wave soldering, due to the size and height of the SMC/SMD component body itself, or because the high component block the high component and block the oncoming tin wave flow, and by the influence of the tin wave flow surface tension caused by shadow effect, the formation of liquid solder on the back of the component body can not be infiltrated into the flow block area, resulting in leakage welding.
Make sure the signal line is as short as possible.
If the length of a signal cable is greater than 300mm, lay a ground cable in parallel.
Ensure that the loop area between the signal line and the corresponding loop is as small as possible. For long signal lines, the position of signal lines and ground lines should be changed every few centimeters to reduce the area of the loop.
Drive signals from a central location in the network into multiple receiving circuits.
Make sure that the loop area between the power supply and the ground is as small as possible by placing a high-frequency capacitor near each power pin of the integrated circuit chip.
A high-frequency bypass capacitor is placed within 80mm of each connector.
Where possible, fill unused areas by connecting all layers of fill at 60mm intervals.
Be sure to connect to the ground at the position of two opposite ends in any large ground fill area (approximately greater than 25mm×6mm).
When the length of an opening on the power supply or ground plane exceeds 8mm, connect the two sides of the opening with a narrow wire.
Reset cables, interrupt signal cables, or edge trigger signal cables cannot be placed near the edge of the PCB.
Connect the mounting holes to the circuit Commons or isolate them.
(1) When the metal bracket must be used with the metal shield device or case, a zero ohm resistor should be used to realize the connection.
(2) Determine the size of the mounting hole to realize the reliable installation of the metal or plastic support, the top and bottom of the mounting hole to use large welding pad, the bottom of the pad can not use solder resistance, and ensure that the bottom of the pad does not use wave soldering process for welding.
Protected signal cables and unprotected signal cables cannot be arranged in parallel.
Special attention should be paid to the wiring of reset, interrupt and control signal lines.
(1) High-frequency filtering should be adopted.
(2) Away from input and output circuits.
(3) Away from the edge of the circuit board.
The PCB should be inserted into the chassis. Do not install the PCB in the open position or inside joints.
Pay attention to the wiring of signal lines under the magnetic beads, between the pads and those that may come into contact with the magnetic beads. Some magnetic beads conduct electricity quite well and may produce unexpected conductive paths.
If a case or motherboard contains several circuit boards, the electrostatic sensitive circuit board should be placed in the center.